Systems & Solutions
Plant maintenance service and support business
We provide maintenance and support services throughout the power plant's life cycle. Our business includes a wide variety of services using preventive technologies for ensuring stable operation of existing thermal power plants, as well as many new technologies, analysis technologies and inspection/diagnosis technologies in order to realize more advanced and reliable systems.
Maintenance and support services to maximize value of thermal power plants by means of preventive maintenance technologies and optimized and economic power generation scheduling systems
Many thermal power plants have continued to support our society. We offer service solutions supported by preventive maintenance technologies to stabilize plant operations, analyze, inspect, and diagnose, and various new technologies to boost plant efficiency and reliability. Our optimized and economic power generation scheduling systems based on IoT technologies are another engineering capability that support thermal power plant operations.
Steam turbine maintenance services mainly include the following four activities:
-
1. Support for periodic operator's inspection
-
2. Support for developing maintenance plans
-
3. Investigate the deterioration of facilities and replace spare parts
-
4. Retrofit and improve performance by applying new technologies
Toshiba's cutting-edge technologies to improve performance
Steam turbines can run over a long period of time for tens of years through repeated maintenance and parts replacement to address unavoidable aging deterioration; however, no one can avoid creep damage due to high temperature steam, fatigue due to turbine load fluctuation or start-and-stop operation, wear, deformation, corrosion or erosion with age. The new technologies developed by Toshiba will improve performance of these steam turbines, leading to an improved economy, increased environmental performance and stable supply of our customers' power plants.
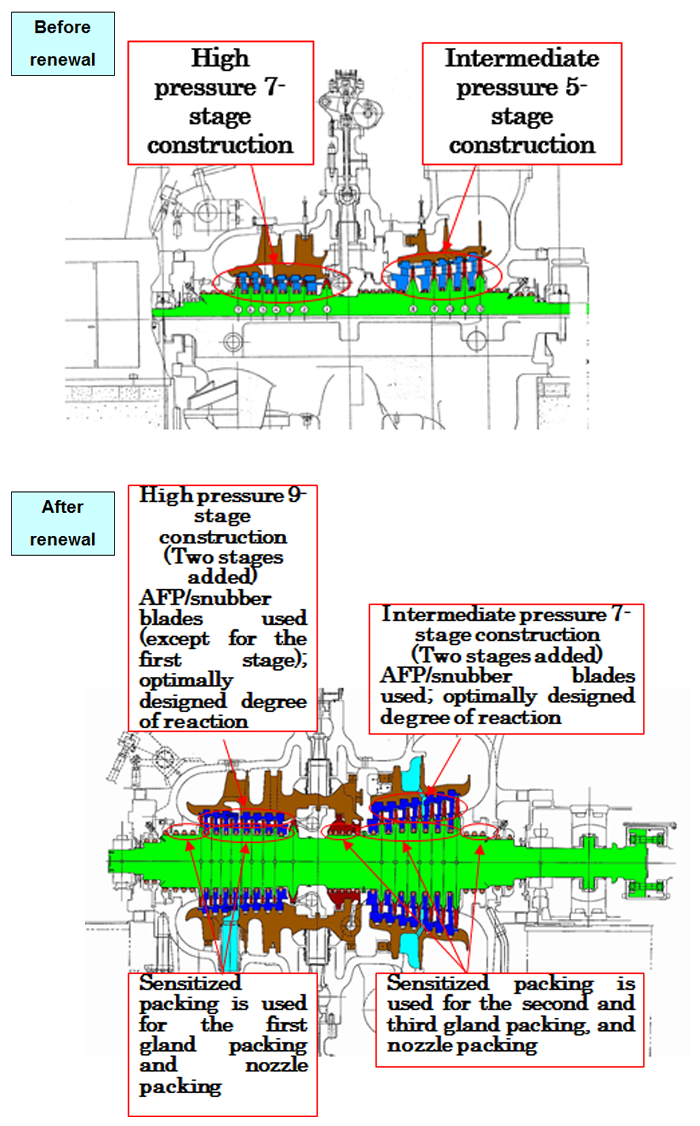
* Colored areas show the renewed equipment.
The following four technologies are applied to improve the performance of the turbine case shown in the above illustration:
-
1. Increasing the number of stages and optimizing reactions at each stage
To optimize heat drop and reactions at each stage, the rotor was redesigned by increasing the number of wheels. -
2. AFP
Advanced Flow Pattern is the high efficiency steam flow passage designed by fully 3-dimensional calculations through computational fluid dynamics analysis. In this flow pattern, especially the secondary loss, which is caused by large-scale vortices and boundary layer growth, is reduced by controlling steam flow lines and mass flow distribution. -
3.Snubber Blade and newly designed Tip Fin
Snubber blade has integrally machined shroud on each blade tip portion. These shrouds compose continuously coupled covers on the whole blades on the wheel by contacting adjacent blades. This structure contributes to mechanically reduce vibration stress. Tip leakage can be also reduced by applying multifin of Hi-Lo type over the blade tip covers. -
4.Sensitized Packing
Conventional packing between nozzle diaphragm inner ring and rotor is supported with relatively rigid flat springs. That is why the gap between diaphragm and rotor is restricted to avoid rotor vibration due to rubbing.
Sensitized packing is supported by flexible springs balancing with the weight of the packing. This type of packing can be applied to reduce leakage loss without increasing rotor vibration.
Gas turbine maintenance services mainly include the following four activities:
-
1. Repair/sales of hot gas path components
-
2. Investigation of the deterioration of facilities and the replacement of spare parts
-
3. Support for periodic operator's inspection
-
4. Support for developing maintenance plans
Toshiba's blade life extension technology - BLE Process™ for gas turbines
The Blade Life Extension Process (BLE Process™) recovers creep life using the HIP (hot isostatic pressing) treatment. The BLE Process™ can be applied to some blades that are at the end of their life cycle (i.e. scrapped) as well as those before the end of their recommended life. With pre/post-processes, such as coating strip, recoating and precise inspections, degraded blades are regenerated. The regenerated blades can be treated as new products in principle. We believe the BLE Process™ is an excellent solution to reduce the customers' gas turbine maintenance cost.
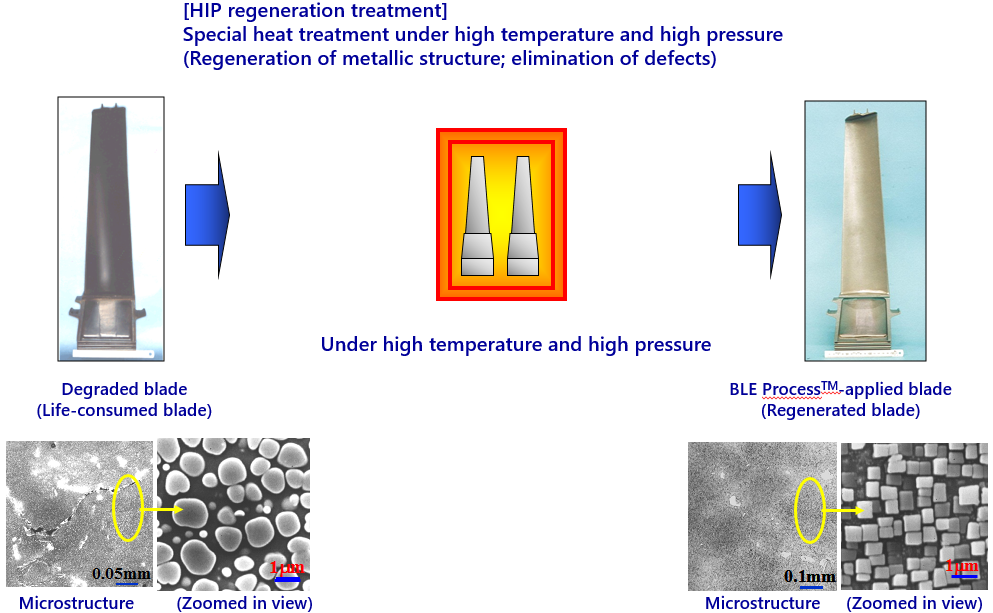
Contribution to the global environment
Thermal power generation uses fossil fuels such as oil, natural gas and coal; therefore improved turbine performance can contribute to reduce CO2 emissions. For example, when the performance of a 700 MW turbine generator increases by 2%, a coal-fired thermal power plant with the usage rate*1 of 80% can reduce CO2 emissions of 77,000 tons per year. In addition, the hot gas path components of gas turbines can be easily damaged by high-temperature oxidation or heat stress and need to be repaired and replaced periodically; however, the hot gas path components are very expensive. Therefore, using these components as long as possible through repeated repair/regeneration leads to a reduction to the load on the environment.
*1: Ratio of the actual power generation amount to the generation capacity on a 24-hour/365-day basis at rated operation
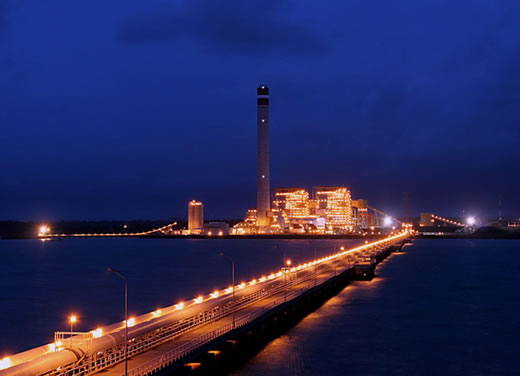