Small-to-middle Scale PLC [type1 light]
The Integrated Controller V series Model 2000 Sequence Control Module S2 (S2) has a proven track record in a wide range of fields as thecore component of social infrastructures and industrial systems. As well as handing down existing assets such as S2 applications, I/O and wiring, type1 light offers enhanced control performance and supports transition to next-generation control systems.
![Small-to-middle Scale PLC [type1 light] image](/content/dam/toshiba/migration/infrasolution/www/infrastructure/industrial/assets/spec2_img_01.jpg)
Standard Sequence Control Module type1 light S
The type1 light S CPU mounts in a standard V2000 I/O rack (3 I/O, 5 I/O or 8 I/O racks are available). It can replace a S2E module.
The type1 light S does not support racks with station bus, or I/O modules that require a station bus.
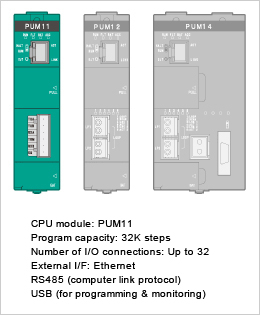
Compact CPU Module
The type1 light S CPU has both a RS485 port and an Ethernet port which supports Toshiba's ASCII computer link protocol. This allows connection by any HMI or SCADA software that has the Toshiba computer link driver.
Basic System Configuration
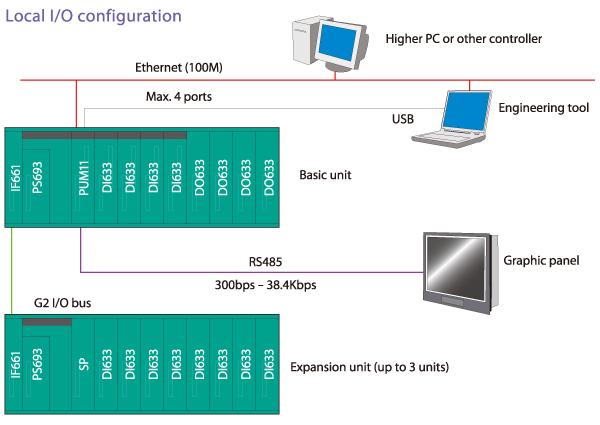
Local I/O unit
- BU668 Basic base
- PUM11 CPU module
- IF661 G2 I/O interface
- PS693 Power source unit
- DI633 G2 I/O DI 16 points
- DO633 G2 I/O DO 16 points
- BU668 Expansion base
High-Performance Sequence Control Module type1 light H
The Unified Controller nv series™ TC-net™ I/O is built-in to the type1 light H CPU. It can be applied to I/O systems to provide enhanced performance. The master station, built into the CPU module, enables direct connection of the TC-net™ I/O loop. A 4 km-long remote I/O system than can be installed at low cost. The connected I/O can be selected from Integrated Controller V2000 series I/O (G2 I/O) or Unified Controller nv series™ TC-net™ I/O.
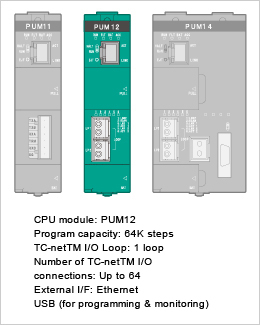
Remote I/O System Configuration
TC-net™ I/O collects and controls remote field I/O in real time. The TC-net™ I/O is a high-speed, robust communications I/O system which uses a fiber optic cable which is highly resistance to electrical noise.
Basic System Configuration
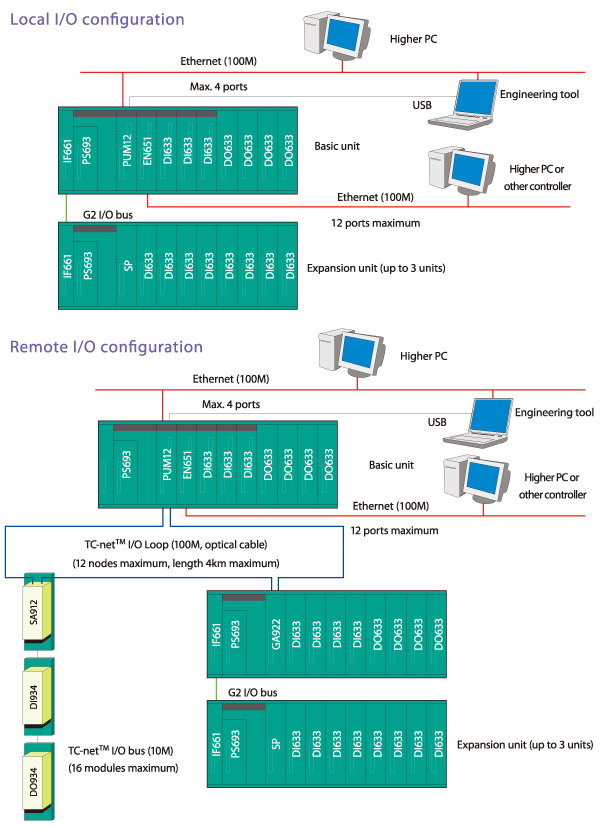
Local I/O
- BU648E Basic base
- PUM12 CPU module
- IF661 Expansion interface
- PS693 Power source module
- EN651 Ethernet 100M
- DI633 G2 I/O DI 16 points
- DO633 G2 I/O DO 16 points
- BU668 Expansion base
Local I/O unit
- BU648E Basic base
- PUM12 CPU module
- IF661 Expansion interface
- PS693 Power source module
- EN651 Ethernet 100M
- DI633 G2 I/O DI 16 points
- DO633 G2 I/O DO 16 points
- BU901 TC-net™ I/O adapter base
- SA912 TC-net™ I/O adapter
- BU905 TC-net™ I/O base
- DI934 TC-net™ I/O DI 32 points
- DO934 TC-net™ I/O DO 32 points
- BU668 Expansion base
- GA922 G2 I/O adapter
Redundant Sequence Control Module type1 light D
The type1 light D CPU supports redundancy.
Redundancy enables greater productivity by providing the highest system availability. With a program capacity of 128K steps and the ability to connect up to 192 I/O modules, the type1 light D is ideal for critical medium and large-scale systems.
The module can also be used in a single module configuration.
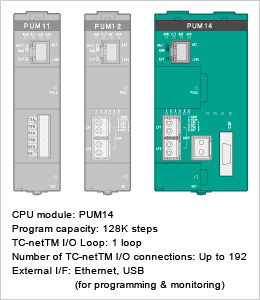
High Performance and Critical System Reliability
Automatic switching to the secondary CPU occurs if a problem is detected in the primary CPU.
Duplex System Configuration
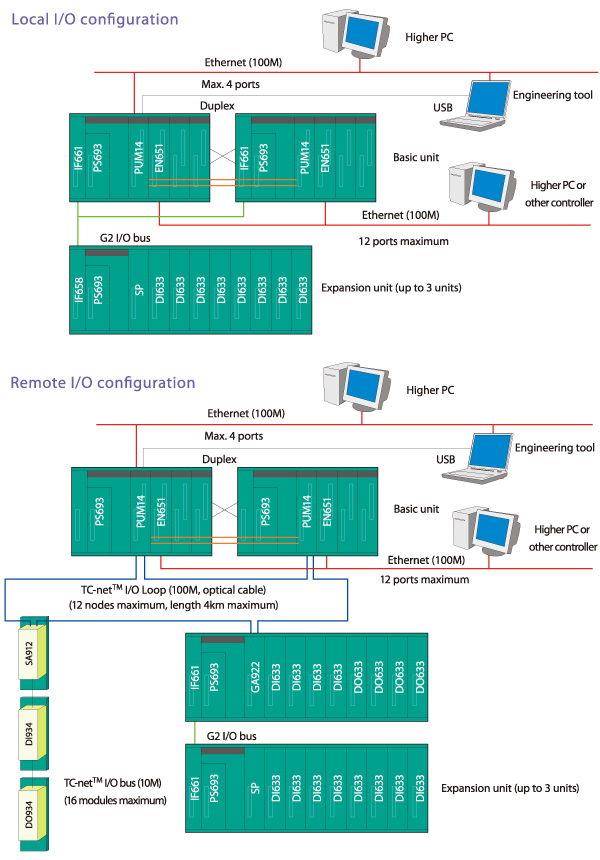
Local I/O
- BU643D Basic base
- PUM14 CPU module
- IF661 Expansion interface
- IF658 Expansion interface (2 ports)
- PS693 Power source module
- EN651 Ethernet 100M
- BU668 Expansion base
- DI633 G2 I/O DI 16 points
- DO633 G2 I/O DO 16 points
Local I/O unit
- BU643D Basic base
- PUM14 CPU module
- IF661 Expansion interface
- PS693 Power source module
- EN651 Ethernet 100M
- BU668 Expansion base
- GA922 G2 I/O adapter
- DI633 G2 I/O DI 16 points
- BU901 TC-net™ I/O adapter base
- DO633 G2 I/O DO 16 points
- SA912 TC-net™ I/O adapter
- BU905 TC-net™ I/O base
- DI934 TC-net™ I/O DI 32 points
- DO934 TC-net™ I/O DO 32 points
Environmental specifications
This table can be scrolled horizontally.
Item | Specifications |
---|---|
Operating ambient temperature | 0 - 55℃ (24-hour average temperature 40℃ or less) |
Storage temperature | -40~70℃*1 |
Relative humidity | 5-95% RH (with no condensation) |
Dust | 0.3mg/m³ (no conductive dust) |
Pollution degree | 2 or less IEC 61131-2/JIS B 3502 |
Corrosive gas | No corrosive gas shall be present*2 |
Vibration resistance | 5<=f<8.4Hz: 3.5mm, 8.4<=f<150Hz: 9.8m/s2 (Compliant with IEC 60068-2-6 / JIS C 60068-2-6, test Fc) |
Impact resistance | 147m/s2 (Compliant with IEC 60068-2-27 /JIS C 60068-2-27, test Ea) |
Noise resistance | 5<=f<8.4Hz: 3.5mm, 8.4<=f<150Hz: 9.8m/s2 (Compliant with IEC 60068-2-6 / JIS C 60068-2-6, test Fc) |
Insulation resistance | DC500V mega 10MΩ or more*3 |
Withstand voltage | AC2000V per minute*3 |
Grounding | 100Ω or less (type D grounding) |
Cooling system | Natural cooling |
- *1 For long-term storage, spare parts should be kept in a dark place away from high temperature and humidity. The temperature and humidity for storing products for long periods should be 0-40℃ and 20-80% RH (with no condensation) and the rate of temperature change should be no higher than 10℃/h. The service life of batteries and power sources, in particular, may be affected by high ambient temperature. Store at room temperature (25℃) or below.
- *2 No materials containing silicon; hydrogen sulfide, sulfurous acid gas, chlorine gas, nitrogen oxide (Nox), sulfur oxide (Sox), ammonia, silicon gas, etc.
- *3 Power terminal - ground terminal
Function specifications
This table can be scrolled horizontally.
Item | Specifications | ||||
---|---|---|---|---|---|
type1 light S | type1 light H | type1 light D | |||
Control system | Stored program cyclic scan system | ||||
Processor | Control processor | 32 bit general purpose processor | |||
Language processor | Exclusive language processor (LP) | ||||
Execution method | Scan method | Ultrafast scan | 1 - 500ms (1ms unit) | ||
High-speed scan | 1 - 500ms (1ms unit) | ||||
Main scan | Floating scan | Selectable | |||
Scheduled scan | 1 - 1000ms (1ms unit) | ||||
Input/output system | Batch input/output: Yes (only MS task synchronized), direct input/output: Yes | ||||
Interruption | I/O | Number | 8 | ||
Multiple interrupt function | I/O multiple interrupt | Not possible | |||
Interrupt response | 1ms or less | ||||
Program type | EV/SS/IP/HS/MS | ||||
Program capacity | 32K steps | 64K steps | 128K steps | ||
Number of tasks/programs | EV | 8 tasks, 1 program/task | |||
SS | 1 task, 1 program/task | ||||
IP | 8 tasks, 1 program/task | ||||
HS | 1 task, 128 programs/tasks | ||||
MS | 1 task, 256 programs/tasks | ||||
Data volume | Local/global variables | 64KW | 96KW | 128KW | |
Special register (S) | 1KW | ||||
Data register (D) | 8KW | ||||
Station global variables | - | ||||
I/O variables (IQ) | 3KW | 3KW | 8KW | ||
Index register | 8 types | ||||
Number of timers | Arbitrary size setting function for user data domain | ||||
I/O [G2 I/O] | Number of connections | System | 1 system | ||
Maximum number of units | 4 units (1 basic + 3 expansion) | ||||
Maximum number of slots | 32 slots | 32 slots | 31 slots (single) / 24 slots (dual) | ||
Batch input/output | I/O update time | 22μs/W or less (at 64-point I/O, 4 consecutive accesses) | |||
Transmission update time | 22μs/W or less (at 64W consecutive accesses) | ||||
Direct input/output | Instruction time | 10μs/W or less | |||
Transmission update time | 15μs/W or less | ||||
TC-net I/O Loop | - | 1 loop (up to 12 nodes) | 1 loop (up to 12 nodes) | ||
I/O [via TC-net I/O Loop] | Maximum number of G2 I/O points | - | 12 nodes, 64 slots | 12 nodes, 192 slots | |
Maximum number of G3 I/O points | - | 1 node, 77 slots | 1 node, 77 slots | ||
Maximum number of TC-net I/O points | - | 12 nodes, 64 slots | 12 nodes, 192 slots | ||
Program languages | LD (ladder diagram), FBD (function block diagram), SFC (sequential function chart), ST (structured text) | ||||
Execution speed | Bit | Contact | 0.08μs | 0.04μs | 0.04μs |
Coil | 0.16μs | 0.08μs | 0.08μs | ||
Integer | Transmission | 0.08μs | 0.04μs | 0.04μs | |
Calculation | 0.08μs | 0.04μs | 0.04μs | ||
Multiplication | 0.24μs | 0.12μs | 0.12μs | ||
Floating | Calculation | 0.4μs | 0.2μs | 0.2μs | |
Multiplication | 0.4μs | 0.2μs | 0.2μs | ||
System configuration | Single | Single | Single/dual | ||
Ethernet | Channel | 1ch built-in (100Mbps) | 1ch built-in, via external EN module (100Mbps) | ||
Tool connection | Possible (built-in) | Possible (built-in/EN651A) | |||
Computer link | Possible (built-in) | Possible (built-in/EN651A) | |||
Socket communication | Possible (built-in) | Possible (built-in/EN651A, EN911) | |||
PC link | Possible (built-in) | Possible (built-in/EN651A) | |||
RS485 | Channel | 1ch built-in (300bps - 38.4Kbps) | - | - | |
Tool connection | Impossible | - | - | ||
Computer link | Possible | - | - | ||
Free port | Impossible | - | - | ||
USB | Channel | 1ch built-in | |||
Tool connection | Possible | ||||
Computer link | Impossible | ||||
Free port | Impossible | ||||
Support network | Station bus | - | Ethernet, TOSLINE-S20, TOSLINE-S20LP | ||
G2 I/O bus | TOSLINE-S20, TOSLINE-F10, TC-net 100LP, FL-net, Profibus, DeviceNet | ||||
TC-net I/O | - | TC-net 100LP, FL-net, Profibus, MODBUS RTU, Ethernet | |||
RAS function | Diagnosis | Battery check, I/O non-sync, I/O parity check, I/O package check, language processor function check, unauthorized order detection, WDT, peripheral LSI check, etc. | |||
Surveillance | Logs (error log, event log, transmission event log), program execution time measurement, program congestion detection | ||||
Debugging & maintenance | Program monitor, data tracing, input/output force |
(Caution)
- Unified Controller nv series is a registered trademark of Toshiba Corporation.
- Other company names and product names herein are trademarks or registered trademarks of the companies concerned.
- The information contained herein is as of June, 2014.
- The information contained herein is subject to change without notice.
- The information contained herein is presented only as a guide for the applications of our products. No responsibility is assumed by TOSHIBA for any infringements of patents or other rights of the third parties which may result from its use. No license is granted by implication or otherwise under any patent or patent rights of TOSHIBA or others.
- TOSHIBA products should not be embedded to the downstream products which are prohibited to be produced and sold, under any law, and regulations.
- TOSHIBA does not take any responsibility for incidental damage (including loss of business profit, business interruption, loss of business information, and other pecuniary damage) arising out of the use or disability to use TOSHIBA products.
- Please use the product properly after thoroughly reading and understanding the instruction manual.
- Export or provision to overseas of this product is restricted by foreign exchange law and foreign trade law.
- This product is under restriction of US Export Administration Act, and permission from US government is necessary for export depending on the exporting destination.
- This product is not manufactured for systems that is directly related to human lives such as described below. If you need to use this product for such purpose, please contact our sales representative.
[Example]
- The propulsion machinery control system of a nuclear power plant, safety protection system of a nuclear facility, and any other systems important to safety
- Control system of collective transport system operation and air traffic control system
- Medical control system that is related to human lives