Process Control Optimizer nv-ADCOP
What are the hidden values that can be brought out in your process control system?
For example, in water treatment plant added value may be achieved by minimizing the dispersion of pH concentration in a pool.
In a coal fired boiler it may be attained by stabilizing and increasing the main steam temperature within the operation range.
The improvement will bring both cost and energy savings for the plant owner.
nv-ADCOP helps you to bring this value-adding performance by providing the control function blocks for such applications, identifying the process parameters and optimizing the control ones.
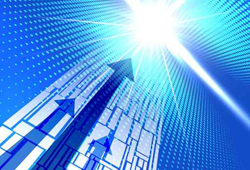
Features
nv-ADCOP Library for Advanced Applications
Provides advanced control function blocks that including MD-PID, (Model-driven PID), executes much improved control performance than conventional control and the other useful function blocks as well as samples programs for typical applications.
System Identification of the Target Process
Identifies the parameters of the specified processes by sampling a set of manipulated value, disturbance values and process values.
Parameter Optimization for the Target Controller
Optimizes the parameters of specified controller for the identified process. This is available for optimizing MD-PID as well as two-degree-of-freedom PID and conventional PI-D, eliminating manual tuning.
Application Example
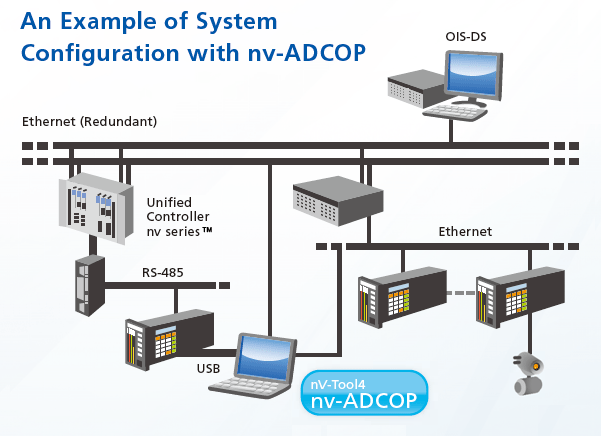
Applied PID algorism in nv-ADCOP Library
PI-D Control
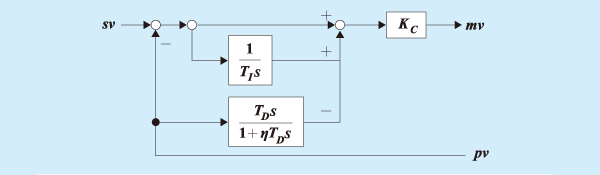
Is amongst the most common PID algorism which can be implemented in world wide DCS. Compared with conventional PID, the merits of PI-D are to prevent differential shocks to target process when the SV (set point value) is changed.
Two degree of freedom PID Control
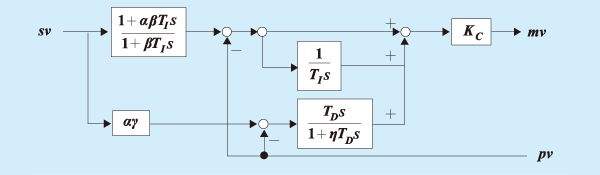
Is a type of two degree of freedom PID algorism developed by TOSHIBA. Compared with a general PI-D algorism, the merit of TDOF-PID is in its ability to optimize control performance for both set point change and process disturbance.
Model Driven PID Control
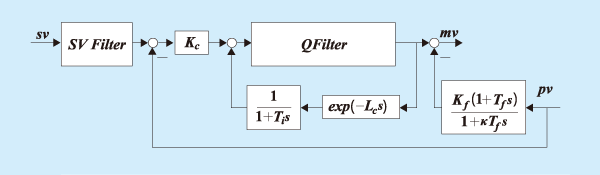
Is a type of IMC (Internal Model Control) algorism developed by TOSHIBA. Compared with PI-D, the merits of MD-PID are to provide optimal control for
- long dead time process.
- disturbance as well as set point changes.
- various process dynamics.
Feed Forward Control
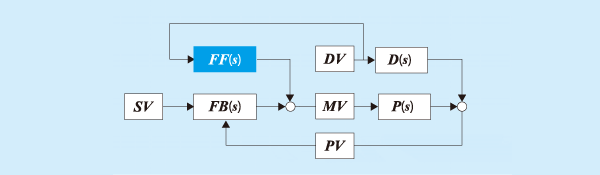
Is a type of disturbance suppression algorism. DV (Disturbance Value) affect PV (Process value). The disturbance components of PV can be compensated by this FF control.
(Caution)
- Unified Controller nv series are trademarks of Toshiba Corporation.
- Other company names and product names herein are trademarks or registered trademarks of the companies concerned.
- Model Driven control system is the control concept proposed by Mr. Hidenori Kimura, the former professor of Tokyo University, in 2000. Model Driven PID (MD-PID) is a control algorism developed by TOSHIBA, based on his concept.
- The information contained herein is as of January, 2013.
- The information contained herein is subject to change without notice.
- The information contained herein is presented only as a guide for the applications of our products. No responsibility is assumed by TOSHIBA for any infringements of patents or other rights of the third parties which may result from its use. No license is granted by implication or otherwise under any patent or patent rights of TOSHIBA or others.
- TOSHIBA products should not be embedded to the downstream products which are prohibited to be produced and sold, under any law and any regulations.
- TOSHIBA does not take any responsibility for incidental damage (including loss of business profit, business interruption, loss of business information, and other pecuniary damage) arising out of the use or disability to use TOSHIBA products.
- Please be sure to read and comply with instruction manuals before using the products herein.
- The products herin are subject to Foreign Trade Laws.
- The products herin are subject to export control regulations of the U.S. authorities. Export and re-export may require approval of U.S. authorities.
- The products herein are not manufactured for systems that require such a high degree of safety as would directly endanger human life in case of failure or malfunction. Atomic energy and safety control, operation controls for mass transportation and airplanes, and medical equipment control are examples. If you intend to use the products in this document for such systems, please consult with our department in advance.