From the Frontiers of R&D and Engineering
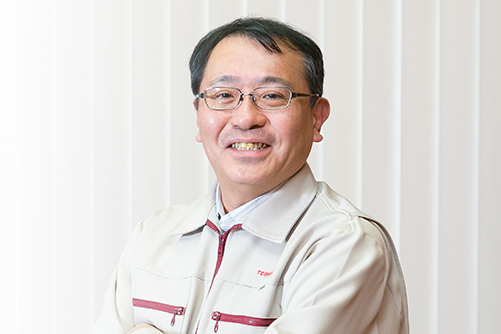
Automation and Robotization of Manufacturing Processes Undertaken by Cross-Functional Teams of Toshiba Group
Takashi MiyauchiAs a consequence of population aging combined with a declining birthrate, Japan’s working population is shrinking. Therefore, industry is expected to face greater difficulty in obtaining the workforce necessary to cope with increasingly diverse products and complex manufacturing processes. To solve this problem, the Toshiba Group is committed to the development and practical applications of automation systems and robots genuinely required by individual manufacturing sites. Its recent focus also includes the development and utilization of robots and robot-based solutions.
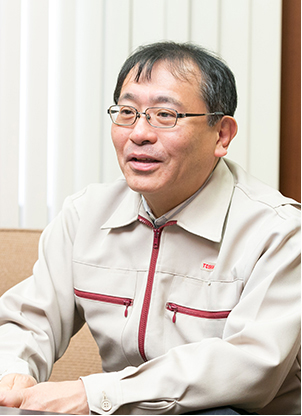
Meeting customer requirements with manufacturing technology
It is necessary to offer good products at reasonable prices when needed so that many customers purchase them. It takes much time and effort to make good products; so good products become expensive. It is therefore not an easy task to meet all requirements. One of the ways to cut prices is to reduce labor costs by automating manufacturing processes using robots. It may also be necessary to develop equipment with higher accuracy in order to improve product quality. The catch here is that spending much time or money on the development of robots or equipment pushes up product prices.
For example, human operators can easily insert connectors into electronic circuit boards, but this task is more difficult for robots than you might expect. Humans find a connector with their eyes, pick it up with their fingers, hold it at a right angle, and insert it into a board until it clicks while relying on a delicate sense of touch. To imitate the actions of a human being, a multi-articulated robot with many sensors and sophisticated software algorithms is required. Indeed, it would be fun to try to develop such a robot, but the development cost might not be justifiable for the given benefit. In such cases, you should discuss with the people concerned to find the optimal solution. For example, you should consider whether you could solder components on a board instead of using a connector, whether a connector is necessary in the first place, and whether there is any way to simplify the operation. You need to find a solution that satisfies customer requirements through discussion with various people.
To solve a problem, I discuss not only with people in manufacturing but also with product developers, designers, salespeople, and quality assurance engineers. The more difficult a problem is, the more difficult it is to solve it, if your activities are confined to a specific area. To seek solutions to great challenges, the organizational power must be utilized. It is worth all your efforts to work out a plan for a sophisticated production line in cooperation with many people. I feel so happy when I see a new production line come on stream, turning out products.
Sharing ideas to select an appropriate method
Many people are involved in finding a solution to a manufacturing problem. Since they come from different departments and have their own points of view, it is important to have a framework for the selection of an appropriate manufacturing method (Figure 1). In Figure 1, the horizontal axis represents the universality of processing points or tasks whereas the vertical axis represents the difficulty of performing them manually. The chart in Figure 1 is divided into four quadrants.
Figure 1 Automation according to characteristics of manufacturing processes
Reference: Toshiba Review, VOL. 73 No. 1 (2018) (PDF: 563 KB)
The first quadrant represents tasks that are difficult to carry out manually. The manufacturing processes of only specific products fall in this quadrant such as batteries developed in-house and superconducting and other special-purpose coils.
The second quadrant also represents tasks that are unsuitable for manual work. However, good machines are commercially available that perform these tasks such as thin-film deposition machines for semiconductor device fabrication and electronic part mounters. It is possible to develop these machines on our own, but they are generally purchased and configured to reduce the time and cost required. Even in that case, we add necessary functions to these machines or modify them in order to create unique production lines or facilities.
The third quadrant represents tasks that can be handled manually but may as well be automated to reduce costs or improve quality. A survey of major manufacturing sites of the Toshiba Group revealed that the goods conveyance, assembly, and inspection processes are often performed manually. Therefore, Toshiba has been automating these processes economically by combining robots and off-the-shelf components. For example, we have developed and deployed automatic guided vehicles (AGVs) using existing components and versatile robot hands capable of picking up items of various shapes.
The fourth quadrant represents tasks that are so specialized that no machines are available that perform them. It requires much cost and time to develop equipment that automates these tasks. To simplify these tasks, we modify product designs so as to facilitate automation or work out a method for assisting human workers.
The Toshiba Group has been promoting the automation of manufacturing processes based on this four-quadrant chart.
AGVs for automating conveyance of parts and units
From back left: Armed AGV Unit 1, versatile AGV, armed AGV Unit 2
From front left: Low-cost AGV, low-cost AGV with high load capacity
Robot for affixing labels of various shapes
Driven by a passion for making good things
When I joined Toshiba, I developed control software for manufacturing equipment. Manufacturing equipment is composed of mechanical and electronic subsystems as well as software. At that time, mechanical designers generally took the initiative in designing manufacturing equipment whereas software engineers developed software modules conforming to the mechanical design. In some projects, I felt software engineers could have done a better job if they had been involved earlier in the equipment design phase. In view of this, I proposed that software engineers participate in equipment design and endeavored to promote productivity improvement, transcending organizational barriers.
Back then, software for different types of systems was coded in different ways. We standardized coding styles to improve software reusability and make it easy for software engineers to develop software for various systems. This helped reduce the development time and improve software quality.
In addition, we developed a PC program that simulates the operation of the manufacturing equipment and control software on the computer. This enabled us to verify software before mechanical and other portions of hardware are completed, reducing the development time by more than 30%. This virtual system can be said to be a frontrunner of cyber-physical systems.
As demonstrated by the above example, we have promoted hardware/software integration early in the design cycle, standardization, and improvement of development processes. These results were applied to the development of manufacturing equipment for liquid crystal display (LCD) panels, in-process inspection equipment for semiconductor devices, mounting and inspection equipment for DVD optical pickups, laboratory equipment for medical systems, manufacturing equipment for 3D LCD displays, and glass bonding machines for cell phones. As I have been involved in the development of various systems, including those outside my specialty, I have acquired deeper and wider knowledge about hardware design, and the configurations and manufacturing methods of various products. As a result, I have acquired the ability to have extensive discussions not only with the people directly involved in this equipment but also with product designers and people at manufacturing sites.
All engineers and researchers share the same passion and commitment to make good things irrespective of their posts or methodologies. People with professional expertise sometimes have different opinions. We always discuss and discuss without giving up in order to find a solution. People in the Toshiba Group are very constructive, listen to others’ opinions without regard to their affiliations or positions, and are so broad-minded as to be prepared to accept different opinions. We place importance on talking things over until we are satisfied. That is where Toshiba’s strength lies.
Leveraging Toshiba’s technologies and comprehensive expertise to create new value
Japanese companies have led the world in the development and application of industrial robots, and industry is now embarking on a new chapter. Due to the increasingly sophisticated manufacturing processes and diversification of products, conventional robots that simply replicate routine work cannot often satisfy manufacturing requirements. In this situation, we are under pressure to develop smarter and more versatile robots. Robots can collect and analyze numerical data while performing a task. Robots are expected to enable us to offer more finely tuned services and improve efficiency by combining them with artificial intelligence (AI) and IoT technologies. For example, such robots will make it possible for us to flexibly respond to customers’ requests and prevent defects.
In order to deliver new robots or robot-based solutions to many people as soon as possible, the Toshiba Group has launched a cross-functional project, uniting the forces of its laboratories, engineering departments, and factories (Figure 2). This is called the Cross-Functional Project for Development of Robot Technology. This project is developing robots for manufacturing, logistics, and distribution automation. In this project, people from different departments draw inspiration from one another while they strive to achieve their dreams of opening up a new era with robots.
Figure 2 Cross-Functional Project for Development of Robot Technology of Toshiba Group
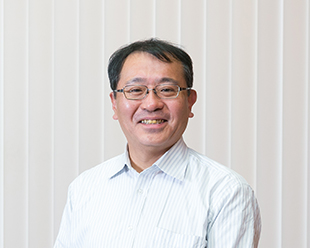
Takashi Miyauchi
- Fields:
- Robotics, mechatronics
- Offices:
- Research & Development Division: Leader of the Cross-Functional Project for Development of Robot Technology
Corporate Manufacturing Engineering Center: Deputy Director (Chief of Automation Promotion) - Registered patents:
- 28 (Japanese and foreign patents: “Assembly method and apparatus for and inspection of liquid crystal display panels,” “Assembly method and apparatus for digital video disc (DVD) optical pickups,” “Manufacturing apparatus for three-dimensional image display and three-dimensional image display manufacturing method,” etc.)
- Papers:
- Takashi Miyauchi, Daisuke Kobayashi, Yusuke Miyamoto, Kazuaki Fujita. 2009. “The Use of Virtual Software Verification Technology for the Development of Manufacturing Equipment Control Software.” The Proceedings of Design & Systems Division Conference, Japan Society of Mechanical Engineers (JSME).
Takashi Miyauchi, Toshio Suzuki, Katsumi Senoo. 2010. “The Use of Differential Interference Microscopy Images for Automatic Inspection of the Mounting of Liquid Crystal Displays.” View2010 Proceedings, Japan Society for Precision Engineering (JSPE)
Kentaro Miyazaki, Takashi Miyauchi, Mototsugu Narita, Takeshi Morita. 2013. “Technique for manufacturing glassless 3D-LCDs.” The Proceedings of Design & Systems Division Conference, Japan Society of Mechanical Engineers (JSME). - Related links:
-
- Toshiba Review: Rationalization of Automated Equipment and Manufacturing Facilities Appropriate to Characteristics of Manufacturing Processes (PDF: 564 KB)
- Toshiba Review: Enhanced Development of Manufacturing Equipment by Use of 3D CAD Data (PDF: 467 KB)
- Toshiba Review: Bonding Inspection Technology for Liquid Crystal Displays (PDF: 429 KB)
- Toshiba Review: Virtual Debugging System for Manufacturing Equipment Control Software Development (PDF: 451 KB)
- Toshiba Review: LD/PD Precision Inspection Machines Contributing to Improvement in Quality of DVD Optical Pickups (PDF: 131 KB)
* Went live on May 15, 2018. This webpage is based on the latest information available as of that date.
From the Frontiers of R&D and Engineering