AI imaging inspection technology using Toshiba’s proprietary no-defects learning system automates and improves the accuracy of inspection processes in short periods of time
AI imaging inspection technology with the no-defects learning system is a solution that automates inspection processes at manufacturing sites. No-defects learning through Toshiba’s proprietary threshold optimization methodology can keep defects from being overlooked while reducing false detections. Automating and saving labor in inspection processes, this technology is helping to bring about a brand-new style of manufacturing site for the COVID-19 era.
It takes time to gather and learn large volumes of defective and acceptable product teaching data
Learning from teaching data comprised only of acceptable product images over short periods of time with few images to use
High-level specialized skills are needed to create and adjust the accuracy of acceptable product models
Image input and parameter settings can be done on the screen without any special skills
Implementation to existing lines and maintenance are a hassle
Since it is not a dedicated inspection device, it can be installed in limited spaces and maintenance is not needed
Features
Toshiba’s proprietary no-defects learning system reducing false detection
Proprietary threshold optimization methodology keeps defects from being overlooked while reducing false detections
Intuitively create acceptable product models on-screen
Easy-to-use GUI for acceptable product model creation, accuracy verification, checking inspection results and more, provided as standard
Easy to install by retrofitting to existing lines
Quick to set up and start using right away by retrofitting cameras, lights, and other devices available on the market, without needing to revamp existing lines
What is Toshiba’s proprietary no-defects learning system?
■ This inspection compares optimized acceptable product models that have learned the thresholds of inspection criteria with images of actual products
Statistically learns the allowable thresholds as acceptable products from differences in the images of acceptable products, based on which it judges products that fail to meet that threshold as defective
■ Threshold optimization methodology reduces false detections (*patent pending)
Detects areas susceptible to false detections and preforms repeated learning to optimize the threshold of the acceptable product model so false detections no longer occur in that area
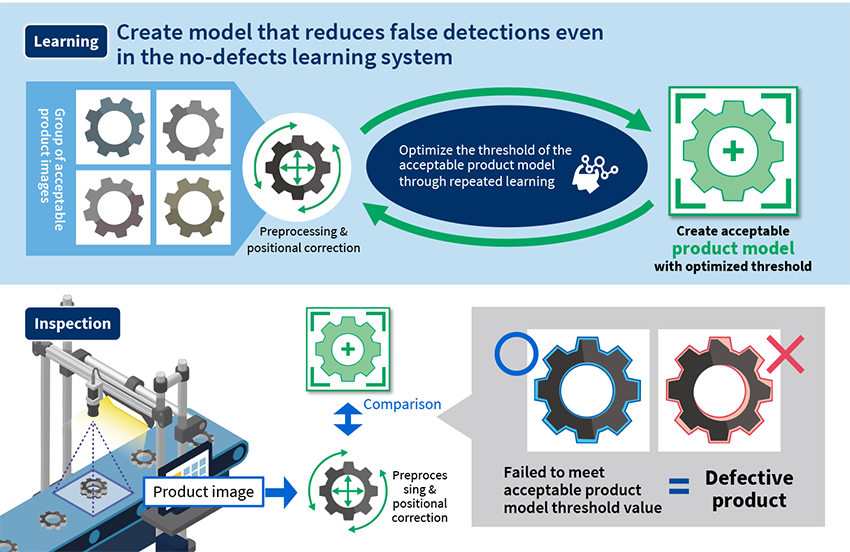
Functions
◆Machine learning tools
Enter image information to be learned on-screen and configure the parameters to create the acceptable product model
◆Rejection decision engine
Compares the acceptable product model with the image of the product being inspected and decides whether the product is acceptable or defective
◆Image preprocessing
Handles positional correction and other preprocessing for the image to be inspected
◆Camera I/F
Receives images to be inspected which were photographed by cameras and sends them to be preprocessed
◆Decision results display screen
This screen shows acceptance or rejection results in real-time, along with past results
The software for the functions above is provided as a package with a yearly subscription license
* Package does not include non-software items such as cameras, lights, and other hardware (quoted separately)
Usage Cases
・Gathering knowledge for auto parts manufacturers’ welding inspections
Utilized to inspect welding in which it is easy for differences in workmanship to arise even among acceptable products, and inspections cannot easily be performed by non-skilled workers
・Automating visual inspections by inspectors
For inspection processes in which inspectors had conventionally performed visual inspections and defect corrections, automating visual inspections reduces inspection workload while maintaining the same level of quality