Restoring Power after Great East Japan Earthquake: Pride and Dedication in Maintenance Services
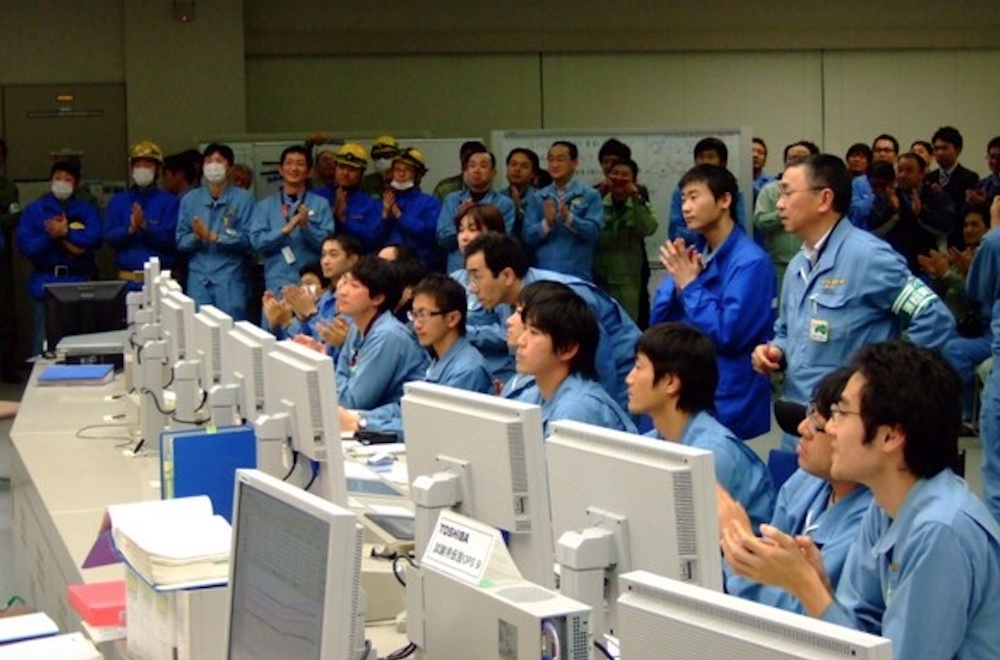
March 11, 2011 is a day that will live on forever in our memories. It was the date of the largest level of natural disaster in Japan’s recorded history: the magnitude 9 Great East Japan Earthquake triggered major fires and a huge tsunami that caused untold damage to life and property. As efforts to save lives and guarantee the safety of victims progressed, the need for the urgent restoration of electric power infrastructure grew as well.
Electricity provides light, heat and information. Modern society couldn’t function without it. In this article, we find out how the thermal power stations that were heavily damaged in the 2011 disaster were restored to service and explore the role that maintenance services played as they worked for the power companies in charge to restore and provide electric power.
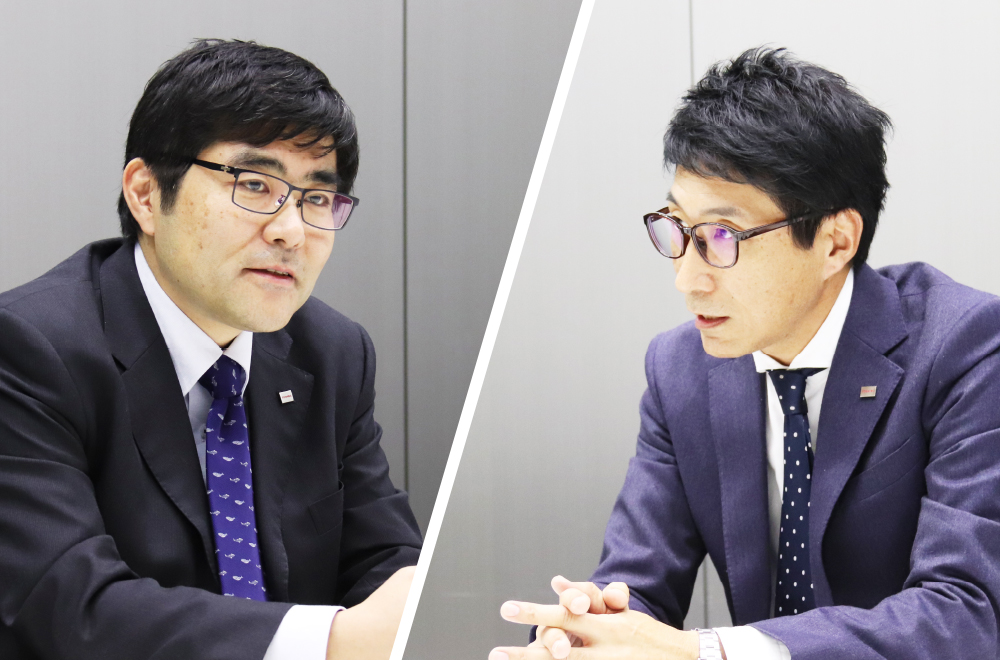
Tatsuya Doiguchi, Senior Manager, Field Engineering Department, Power Systems Div., Toshiba Energy Systems & Solutions Corporation
What happened to the thermal power stations on the Pacific coastline when the Great East Japan Earthquake struck?
Thermal power stations produce electricity by burning coal, petroleum, natural gas and other fuels in boilers, using the heat to convert water into steam, and using the steam to rotate turbines. There are several different power generation methods available, but thermal power remains an indispensable and reliable source of electricity.
Toshiba is heavily involved in the construction of power plants and the manufacture of turbines, generators and other main equipment for thermal power plants. It also provides a wide range of maintenance services after commercial operation starts. Ken Takagi, Head of the Thermal Power Services Engineering Department, and Tatsuya Doiguchi, Head of the Field Engineering Department, both in the Power Systems Division of Toshiba Energy Systems & Solutions Corporation, regard preventive maintenance at existing thermal power stations as their chief mission. However, in addition to their focus on maintenance plans and regular inspections, they also provide unplanned maintenance in the form of recovery services for the equipment after incidents occur.
This meant that they had a large role to play after the unprecedented events of the Great East Japan Earthquake.
Let’s turn back the clock to March 11, 2011 and zoom in on the Haramachi Thermal Power Station run by the Tohoku Electric Power Co., Inc. in Fukushima Prefecture. Through this we can look back on how the maintenance service engineers responded to the crisis and worked alongside Tohoku Electric Power, partner companies and equipment manufacturers to achieve their shared objective of resuming it to operations.
“We heard there was a power outage in the Tohoku region. That one piece of news was enough to tell us how serious things were. .Japan has a highly dependable power grid, so it’s extremely rare for an earthquake to cause a power outage. Watching the news made it clear that the Tohoku region had suffered great damage to its electric power infrastructure. Electricity usage restrictions were placed on the Tokyo metropolitan area as well. Because of that, Toshiba’s Keihin Product Operations, which manufactures power generation equipment, could not work at full capacity. We had to spend time searching for a solution, but eventually we were allowed to operate only those manufacturing lines related to recovery activities.” (Takagi)
With time, a clearer picture emerged of the damage to situation at thermal power stations on the Pacific coastline. The Haramachi Thermal Power Station, owned by Tohoku Electric Power Co., Inc., was one of the most severely damaged. Although a major tsunami warning was issued after the earthquake, Unit 1 (a 1,000MW, turbine and generator provided by Toshiba) continued to operate in order to provide a stable supply of electricity. But eventually the workers had no choice but to perform an emergency manual shutdown and evacuate once the coming of the tsunami was confirmed.
The 18 meter-high tsunami that struck the power station destroyed both the AC generators and the backup DC power sources. This stopped the supply of lubricant to the turbine and generator, which were running on inertia, causing the turbine rotor to burn out. What’s more, the first and second floors of the turbine building, where a lot of auxiliary equipment was installed, were flooded. This resulted in catastrophic damage to the overall turbine and generator.
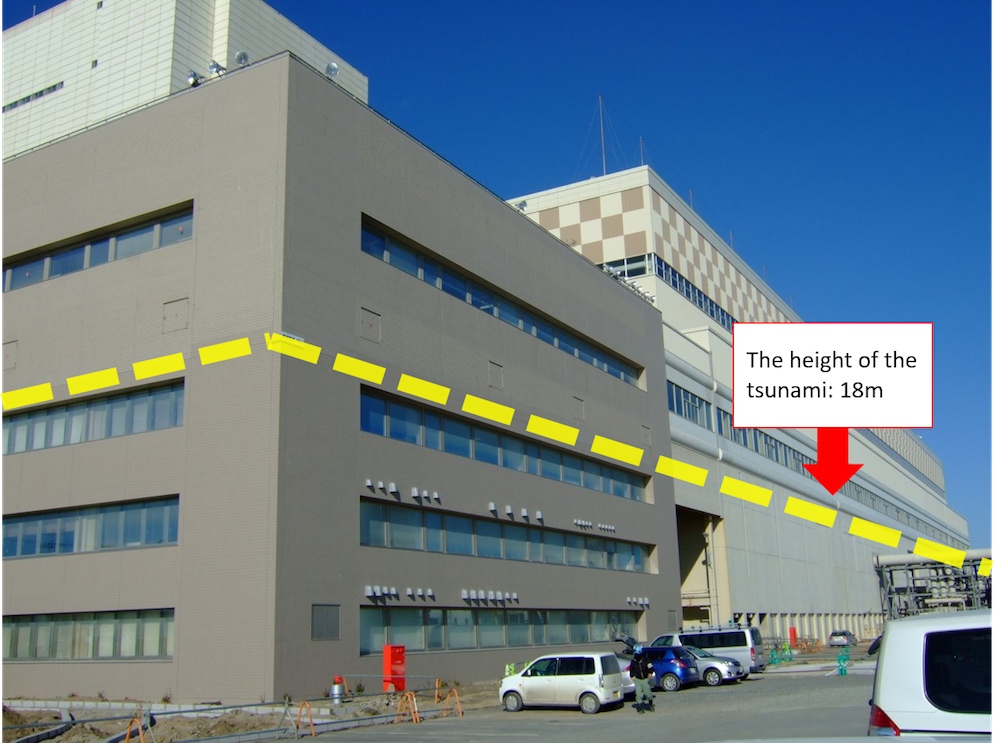
The Haramachi Thermal Power Station was within 30 kilometers of the Fukushima I Nuclear Power Plant, a restricted area. Thus Toshiba was unable to get a visual check of the damage for some time. While the damage was indeed enormous, the maintenance services team headed to the site with one thought in mind: getting the Haramachi Station back into service again.
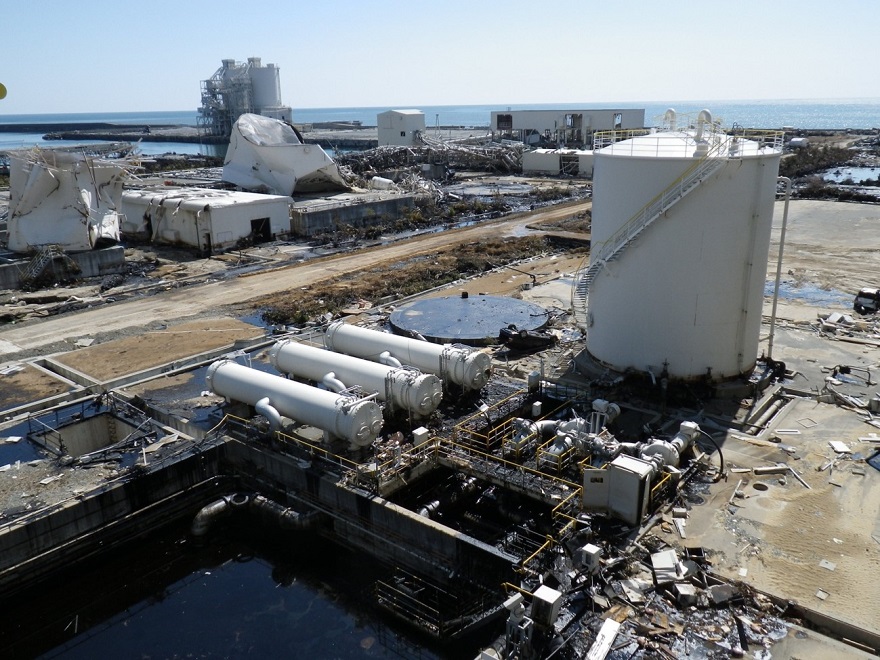
One goal in mind! Restarting after the severe disaster
“The power company did a lot by removing debris, routing around dangerous areas and securing the roads, and once the safety of the site was assured, two weeks after the disaster, we headed there in a chartered minibus. Even getting fuel was a struggle. It was hard to find a gas station, and when we did there was a long line. We warmed the food we’d brought with us on a gas stove and stayed without meals at a hotel where the showers were not working. In short, the circumstances were quite difficult when we went to check the damage in the power station. The station had been left untouched after the disaster, so the damage to the turbine was even worse than we had imagined.” (Doiguchi)
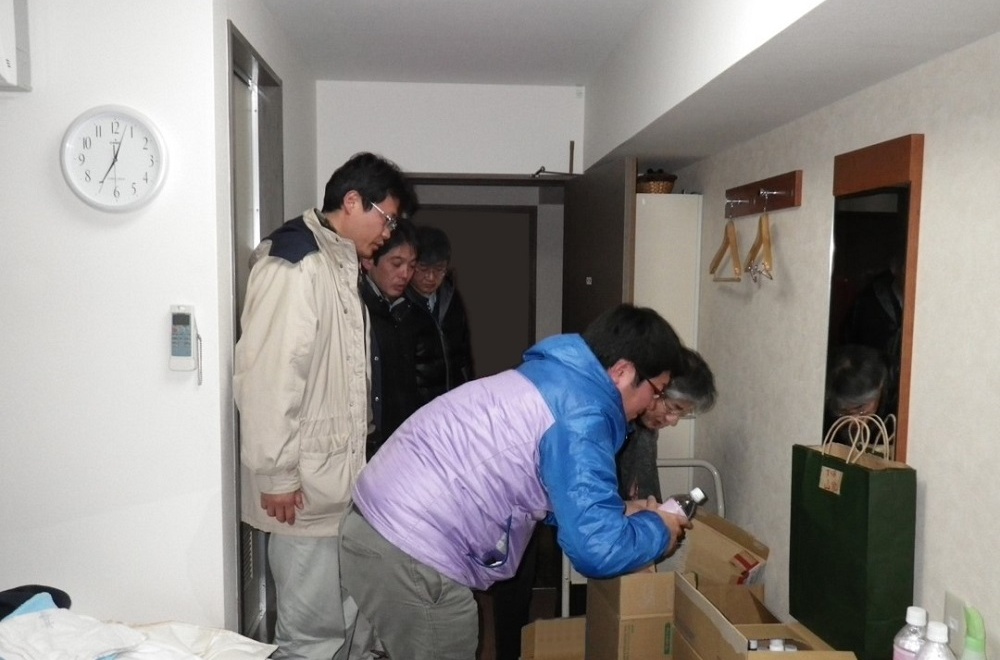
The tips of the steam turbine blades had flown off in all directions and the bearings that supported the approximately 160-ton rotor had melted down and were damaged. The submerged equipment and piping had not been treated for some time, so they had begun to corrode. Despite all this, the maintenance services team, led by designers, conducted field surveys of the situation over several sessions. They brought in expertise from relatively less damaged power stations which had been restored earlier, and then created a road map for getting the Haramachi Station back online.
“As maintenance services professionals, we live by the following creed: ‘Don’t stop the power.’ From field surveys, we determined that it was possible to restart power generation, so despite of this being an unprecedented project, we, the power company, our partner companies and the equipment vendors united around the common goal of restoring the power.
And so we got down to work.” (Doiguchi)
Doiguchi was posted to the area to provide construction support, handle various matters such as preparing parts and cope with the daily problems that occurred. At first he commuted to the site on a scheduled bus from Fukushima City, a three-hour journey. He shared the ride with students on the way to high school from their shelters, passing by entire villages that had been designated as planned evacuation zones. Many of the families and the homes of the workers involved in the plant recovery had also been hit by the disaster.
To get the Haramachi Station working again as soon as possible, Doiguchi and his team members focused their energies on cooperating with other companies. Since the steam turbine in a thermal power plant works in a high-temperature, high-pressure environment, it is made with highly specialized steel to practically custom-made specifications. Each one normally takes over a year to manufacture and deliver. Since it was an emergency, however, they asked the manufacturers to speed up the process, and prepared the necessary materials and parts one by one. Occasionally they had to perform field surveys on behalf of equipment suppliers who could not enter the site.
“It gave me a fresh understanding of the fact that a power plant is developed and maintained through the cooperation of a lot of organizations, including equipment, parts and material suppliers. We told them, ‘We want to get the power station back on line as soon as possible. To that end we’ll be making some unreasonable requests, but we hope you will work with us here.’ Expressing these strong desires in our communications with them deepened our determination to restore the station to normal.” (Doiguchi)
“Power companies adopted a variety of initiatives to ensure power, such as repairing and restarting stopped power stations, increasing turbine output, and hurriedly constructing new stations to help with recovery efforts after the disaster. So I was involved in over a dozen thermal power stations at the same time. We listed the units at each power plant on a whiteboard. Every time we managed to get something operational, we would draw a flower mark on it to help visualize our progress. It took a while, but we were finally able to draw a flower mark around the Haramachi Station, the last one left on the list.” (Takagi)
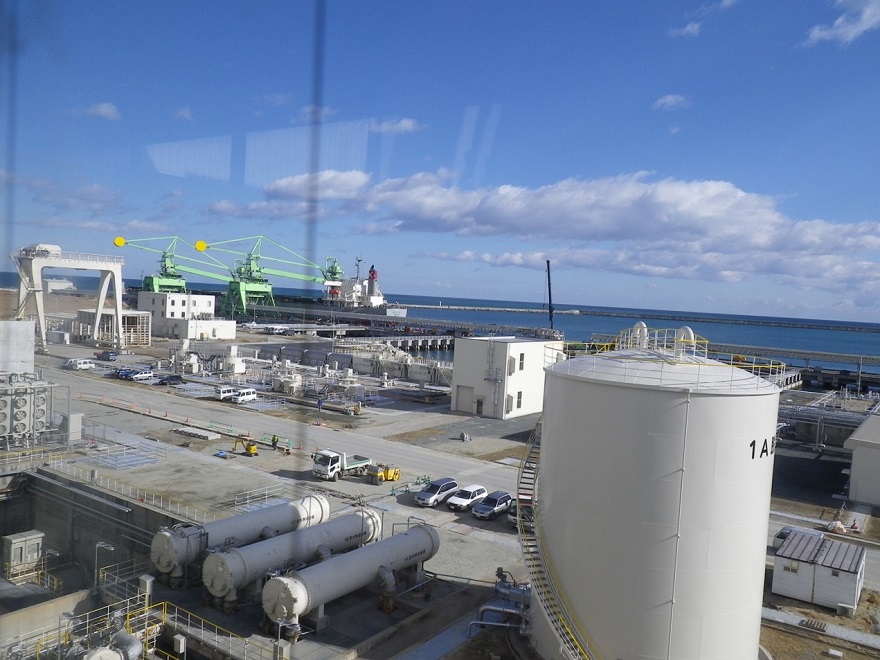
On January 28, 2013, the Haramachi Thermal Power Station finally resumed the commissioning operation. It had taken 22 months from the earthquake disaster to get it operational again. It was the result of concentrated expertise in maintenance technology and operational know-how, as well as the culmination of a tremendous amount of communication with the client and all of our partners.
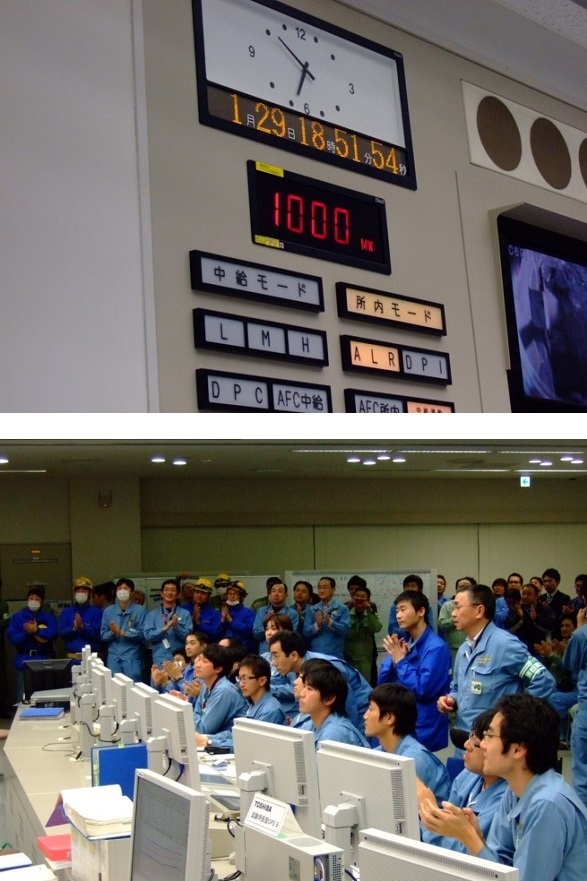
“When we finally managed to restart the station, I was so happy I almost cried. There are cases where a power station can’t operate simply because a single meter isn’t working. This restoration project helped me appreciate the existence of the power stations that support our lives and societies, and to find greater meaning in the work that supports them. There are a lot of people in the commemorative photo we took when the station resumed operation, but they only represent a small percentage of the people who helped with this project. We followed the project until the very end, but there are many other people in other Toshiba departments and among our partners who were involved in various stages of the project and who struggled together with us to get the station back in business. We worried a lot as we worked with the machines because the recovery wasn’t going as we had expected, but in the end the deciding factor was the people involved. We succeeded because everyone on board shared one ambition and worked together to achieve the restoration. I am extremely grateful to every single person who worked with us to make this possible.” (Doiguchi)
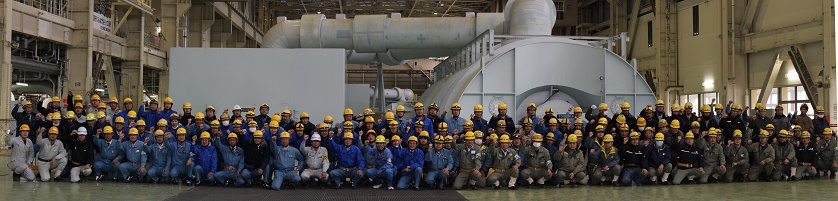
Naturally, the work of the maintenance services team goes beyond disaster recovery. They also provide regular maintenance support on a global level. In March 2013, a problem occurred with a steam turbine at a thermal power station in Malaysia. The rotor needed to be replaced as soon as possible.
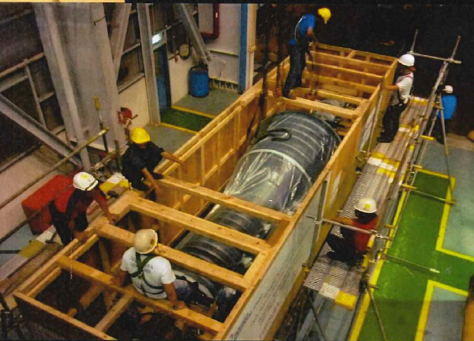
“The power station in Malaysia was extremely important to the client, so to shorten the delivery time as much as possible, we reduced the delivery date for special materials, diverted prepared materials meant for other products and re-purposed them at the factory. This, along with other measures, allowed us to deliver the product within the period specified by the client without affecting the delivery of other products. Moreover, although large rotors are usually transported in ships by sea, but since our highest priority was the delivery time, we chose to charter a huge Russian transport plane and transport it by air.
As a result of all this, we were able to manufacture and deliver two rotors in six and a half months instead of the twelve months we initially estimated.
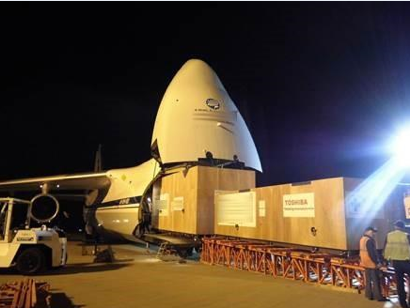
Although the client was worried that we wouldn’t be able to respond because we were busy with recovery from the Great East Japan Earthquake, we were able to eliminate those fears and deliver the product in a very short time. We owe it all to the cooperation of the manufacturing factories, our partners and the client.” (Takagi)
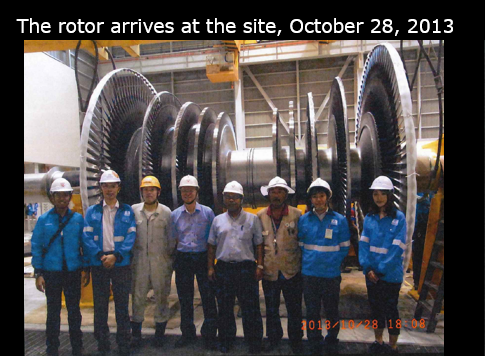
The maintenance creed, “The power must not go off” is not just Japanese, it’s followed by maintenance service engineers worldwide, in every region. With this sense of purpose, they support the infrastructure of thermal power stations and keep their eyes fixed firmly on the lives of the people that rely on that infrastructure.
“Maintenance services evolve with the times. Now that we’re in the age of IoT, we are able to monitor the operation and the aging status of the machines in a power station in detail. This helps us to carry out preventive maintenance and stop problems before they occur. We create maintenance plans and propose regular inspections covering the long 30- to 40-year life cycle of thermal power stations. Additionally, we’re always supporting the infrastructure by suggesting ways to incorporate new technologies and expertise. We do this because contributing to society is our job, our mission and our joy.” (Takagi)
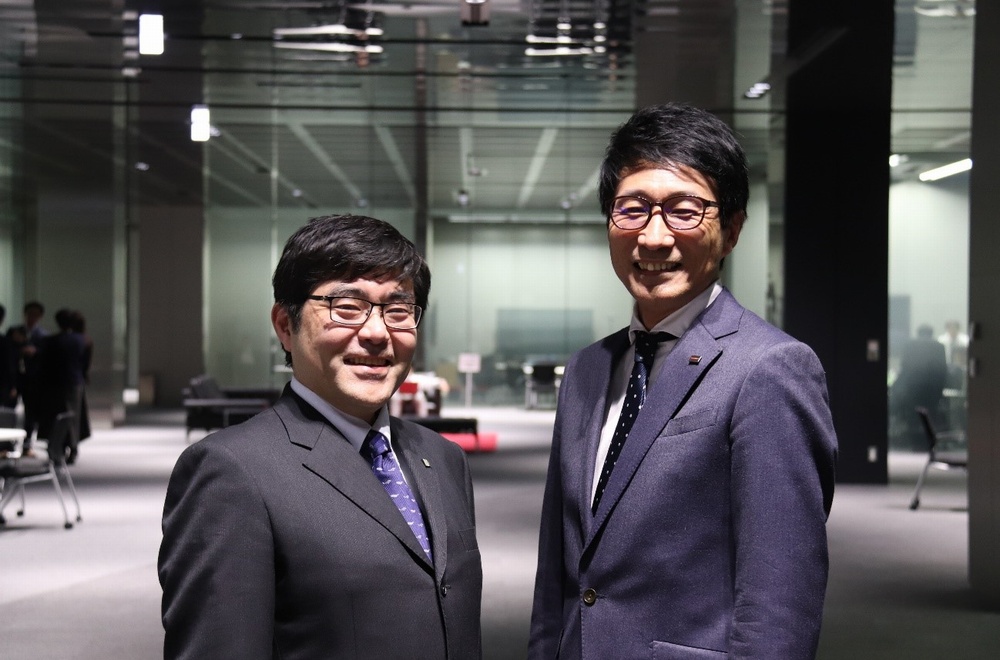
Source : Toshiba Clip(https://www.toshiba-clip.com/en/detail/7112)(Toshiba Corporation)
■Related link(Pride and Dedication in Maintenance Services: the Lifeline that Supports Social Infrastructure)