Creating the Dream Energy Source of the Future
- The Reality of the Megastructures and Millimeters of Fusion Power
Electricity is an absolute necessity for modern life, which explains why there are so many different kinds of infrastructure to provide it. Thermal power, hydroelectric power, nuclear power, renewable energy… But as a form of power generation that eliminates the CO2 emissions of thermal power generation, and the high-level radioactive waste produced by nuclear power generation, there’s no “dream” energy source dreamier than fusion.
What you are probably not aware of, is that there is a massive global project underway to build an experimental facility for fusion—that would not look out of place in a science fiction movie. This project is called ITER (originally the International Thermonuclear Experimental Reactor).
We covered the ITER project, with its seven member entities (including Japan), and the actual workings of fusion in the article ” A Star is Born. What’s Happening on the Front Lines of Fusion, the “Dream” Energy Source.” Here, we’ll dive a little deeper, getting into the front lines of the design/development process of the ITER equipment that Japan has been assigned to make. In doing so, we shed a light on the struggles and passions of the projects’ younger members, as they fight to realize the goals of this massively ambitious project.
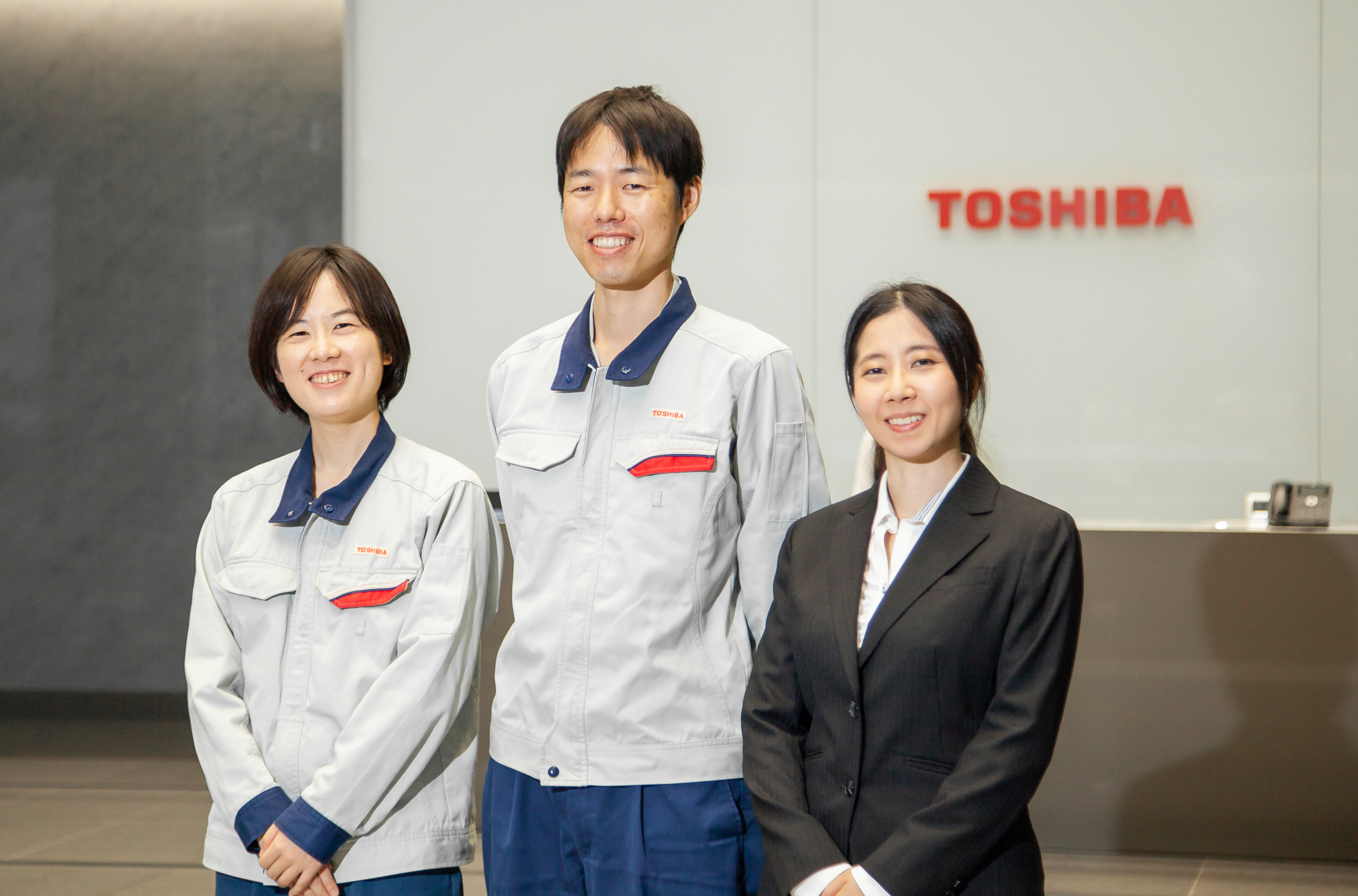
Yuichi Yoshizawa, Advanced Nuclear Equipment Design Group, Design Dept. 3, Keihin Product Operations, Toshiba Energy Systems & Solutions Corporation
Yumi Suzuki, New technology application system Group, New Technology Marketing & Sales Dept., Toshiba Energy Systems & Solutions Corporation
It is hardly surprising that bringing the sun to the Earth would be a massive undertaking.
Fusion reactors generate power by heating plasma to more than 100 million degrees Celsius. The process is essentially a recreation of what occurs inside of the sun, and the fusion reactors have even been referred to as “artificial suns.”. These fusion reactors, which are being designed and developed by countries all over the world using their most cutting-edge engineering technologies, are one of the most complex man-made structures ever to be built.
Japan is in charge of the superconducting coils, which are used to produce the magnetic fields that will contain the super-heated plasma. Toshiba Energy Systems & Solutions, have been commissioned by the National Institutes for Quantum and Radiological Science and Technology (hereafter “QST”)— to produce the toroidal field (TF) coils. More specifically, to produce 4 of the 18 TF coils to be used in ITER, and the 6 coil cases that will house the winding packs produced in Europe. Trial production for the project began in 2014, following a production verification phase.
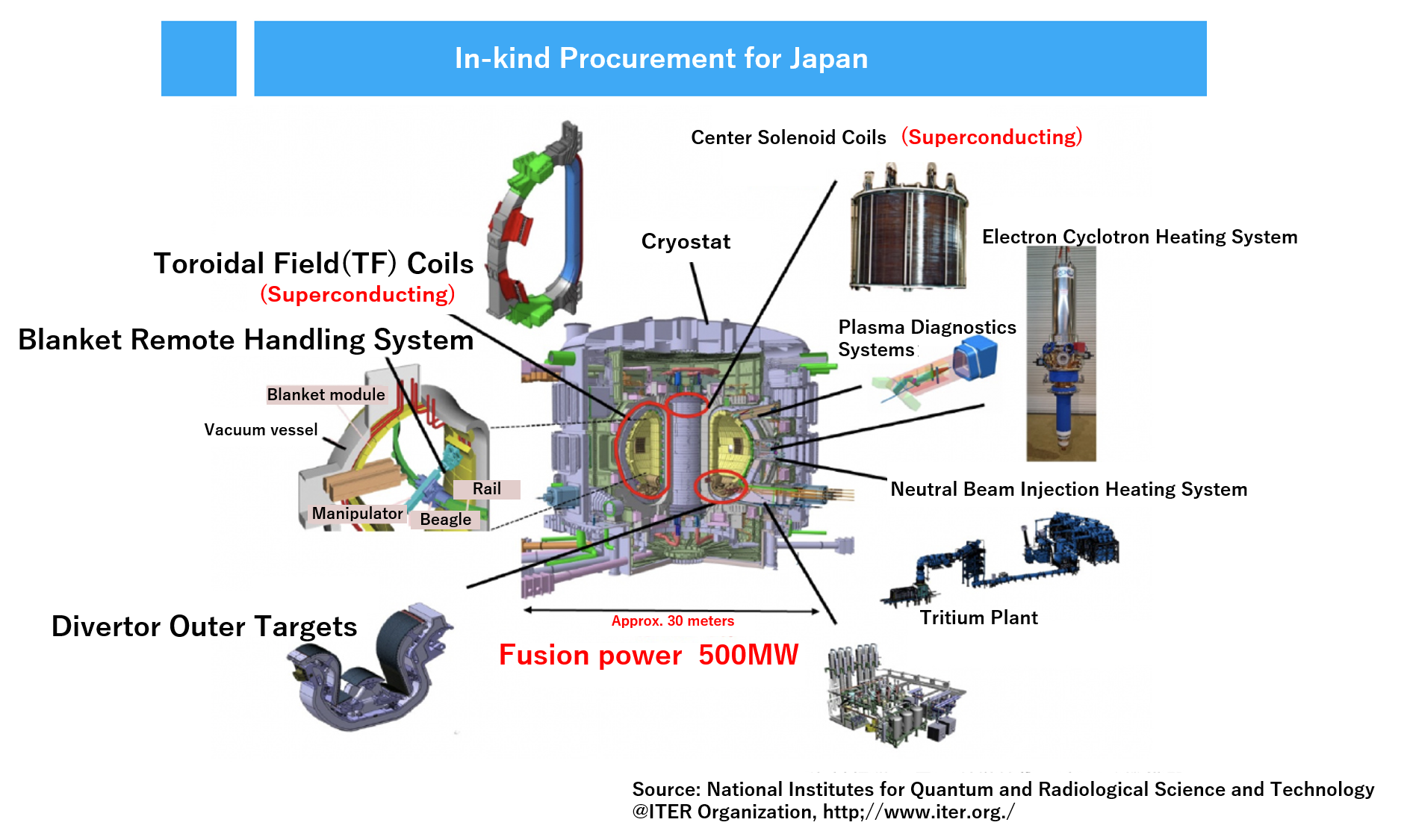
The TF coil is a D-shaped structure that stands 16.5 meters tall and 9 meters wide, with a total weight of 300 tons. The sheer size of the structure (being the height of a five-story building) makes it extremely difficult to produce the absolute precision required in the manufacturing technology. Yuichi Yoshizawa and Kaori Sakaguchi, who are involved in the production of the TF coil at Keihin Product Operations, tell us how difficult it was to handle this very issue.
“With the coils we need to wind around the D-shaped ‘winding pack’ part of the structure, our margin of error is only ±0.02%, which is ±2 millimeters out of a total of 10 meters. Here at Keihin Product Operations, we’ve never had a product this size—16.5 meters tall, 9 meters wide—that demanded this level of precision. Although this is a trial production, we still only had one shot at manufacturing and assembling these parts. So, our focus was on exactly how precise we could be through this entire process,” said Yoshizawa.
“It’s not just about the precision. There’s also the schedule that comes with working on an international project. All those countries, including Japan, worked responsibly and came up with the equipment that’s been asked of them. Here in Japan, we tried to move quickly and figure out how best to use the limited time we had, despite it being such a long project,” said Sakaguchi.
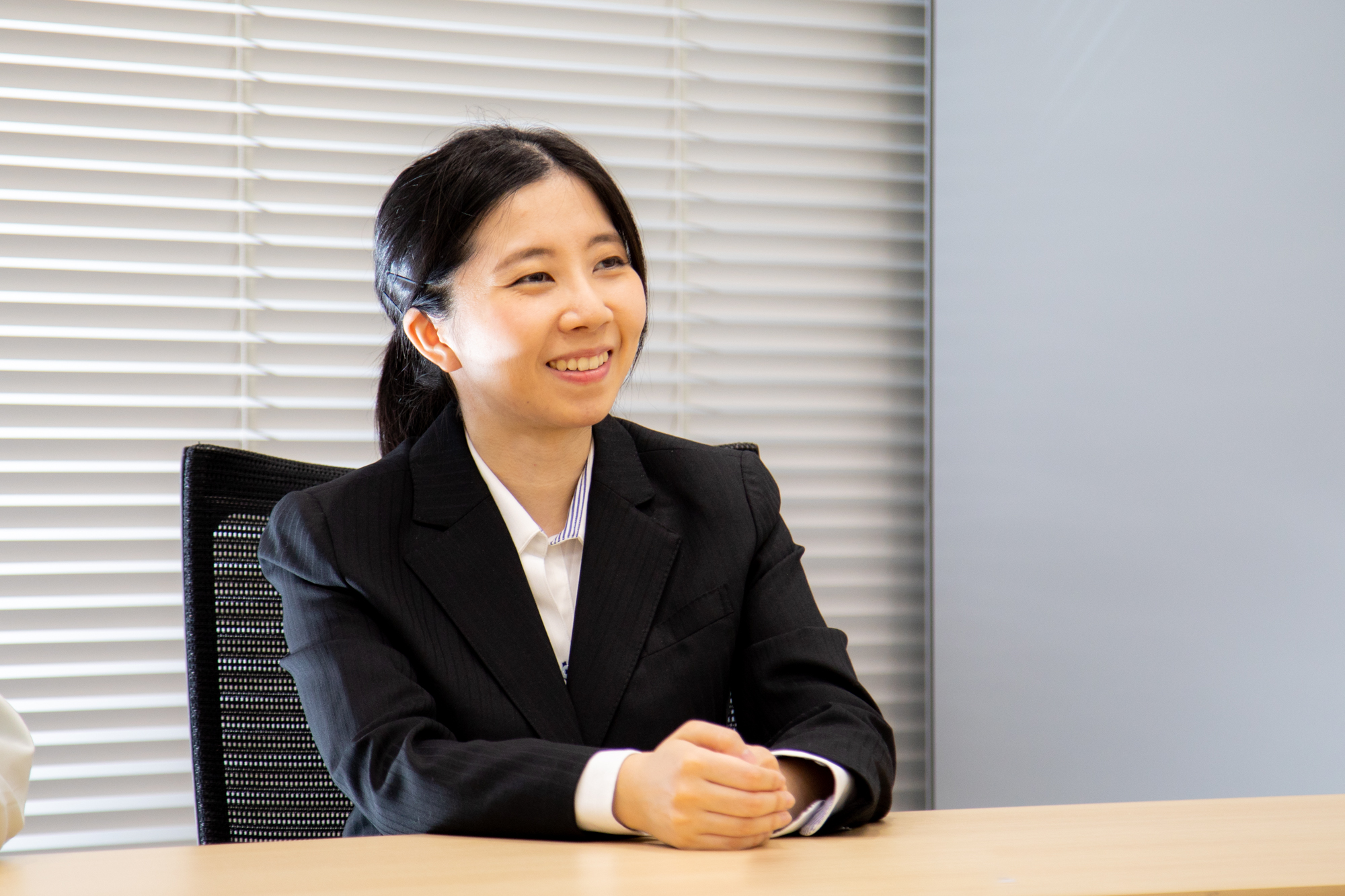
Yumi Suzuki, who’s involved in the project on the sales front, handling everything from bids to contracts to collation for the ITER project, said that the sense of unity within the team served as a driving force for the project.
“To make sure the work on-site goes smoothly, we have to be really accurate in communicating the specifications and requests of our client, QST. Here in sales, one of our major goals is to solidify contracts, but this project is one that’s going to go on for a long time. We focused on sharing the information and specifications we got, and took it one step at a time.”
Half a century’s worth of fusion equipment development, now paying dividends
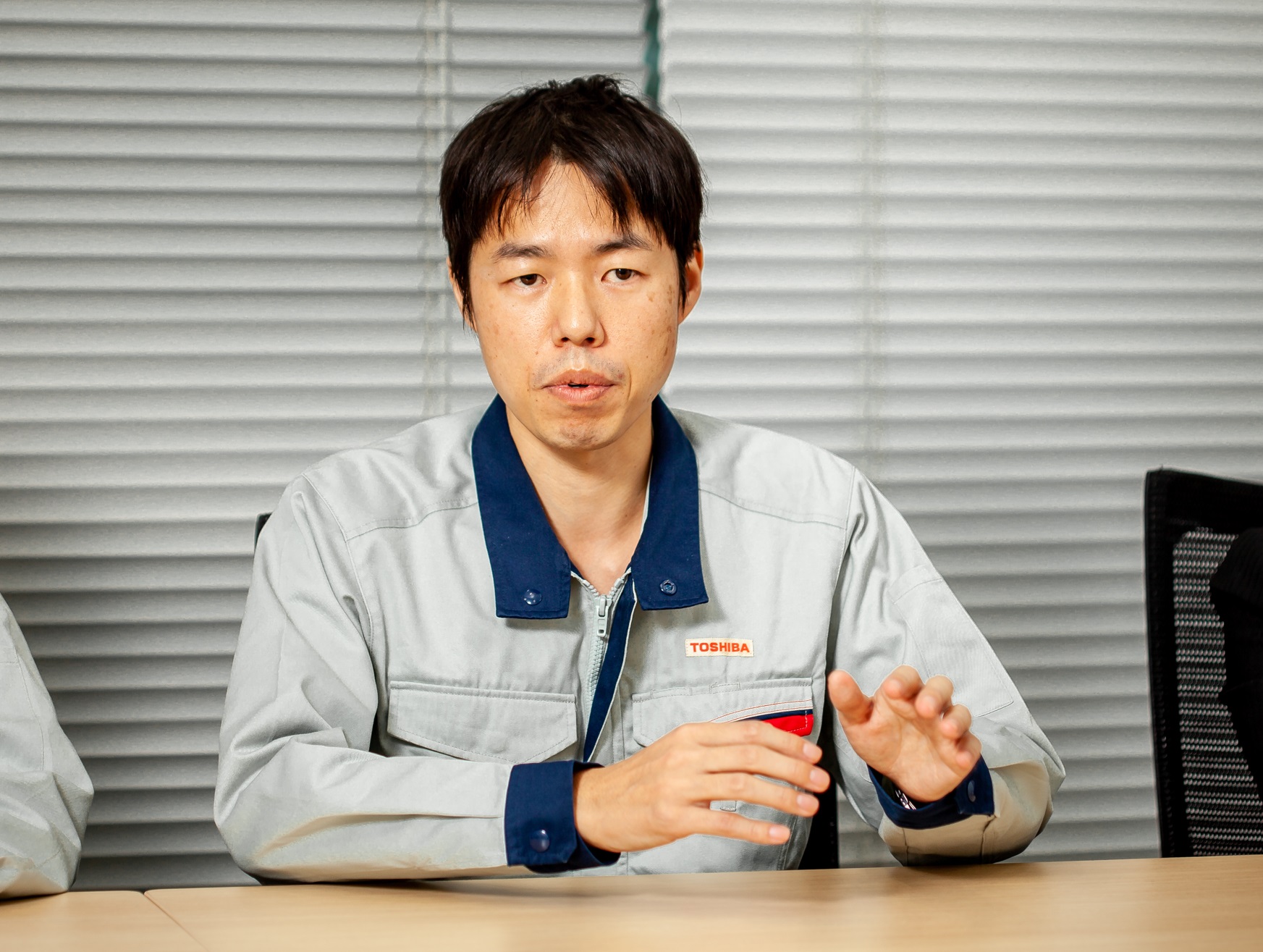
For Yoshizawa and the rest of the design team, trial and error was the name of the game. With every instance of small-scale trial production, they would learn something new. This was when Toshiba’s extensive experience with developing energy-related equipment, and its established design/development foundation, really came to the fore.
“Toshiba has been working on fusion-related equipment since the 1970s, when fusion research first began. What would take forever if we had to start from scratch, doesn’t take as long when you have the knowledge and know-how we have inherited from our predecessors. Take the TF coil, for example. The winding apparatus itself is something that’s new to us, but the basic structure of it is based partly on a large-scale coil we’d manufactured in the past. We’ve also been able to look beyond just Keihin Product Operations and utilize all of the knowledge available to us at Toshiba, whether it be from our research centers or the Corporate Manufacturing Engineering Center. This has truly been an all-Toshiba project,” said Yoshizawa.
TF coils are comprised of what’s called the winding pack, with its superconducting coils, and the coil case, which houses the winding pack. The manufacturing process for the winding pack can be divided roughly into six steps.
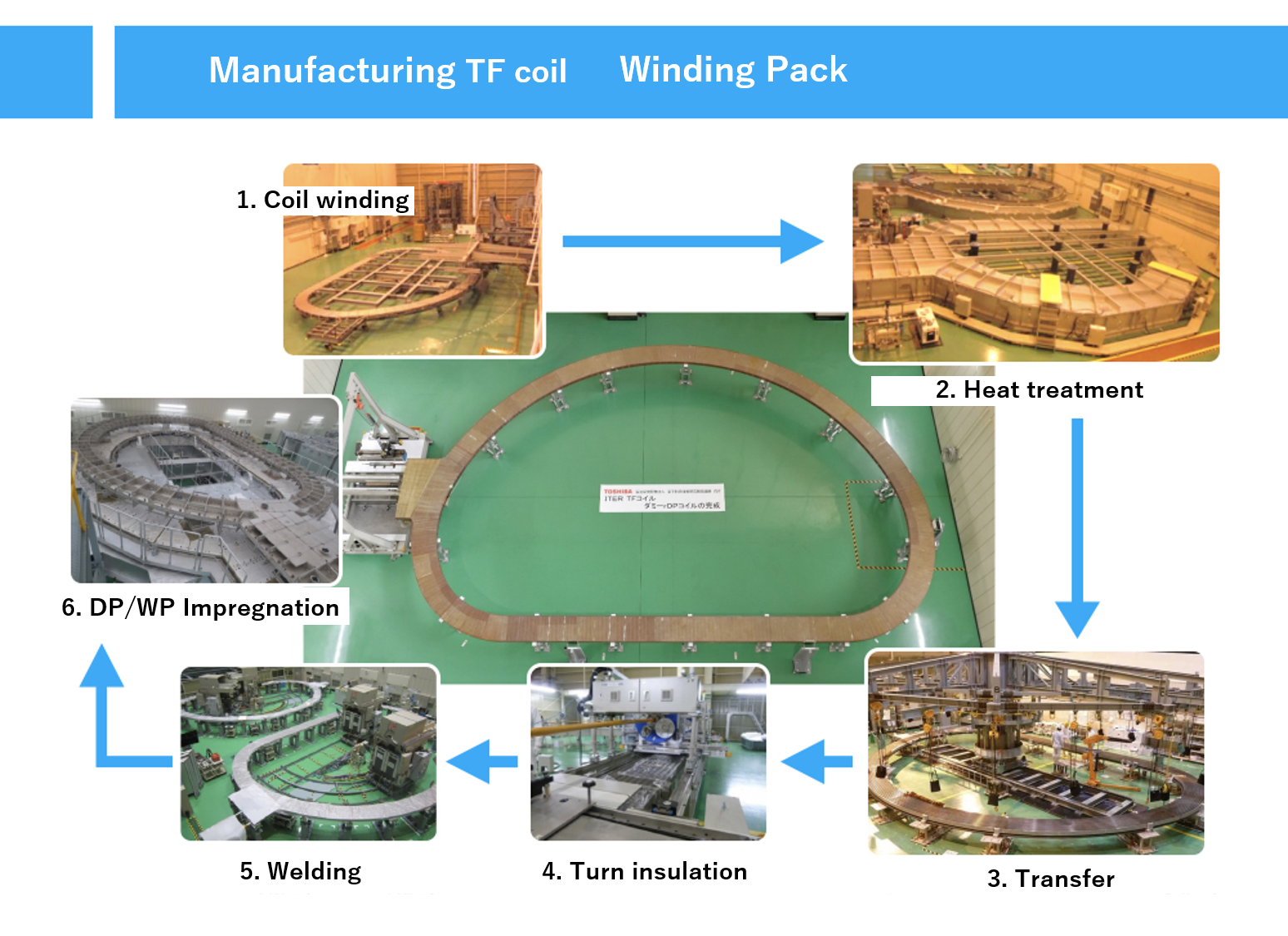
Each step takes about three weeks and involves highly complex processes. With the number of operations involved, each step requires that there be a designated manufacturing space established within the expansive grounds of Keihin Product Operations, with production occurring in a continuous, streamlined process. After combining the winding pack and the coil case (welding assembly and impregnation), the final machine processing is conducted, using a special kind of processing equipment for extremely large-scale equipment.
One process that’s particularly important in terms of ensuring the precision and speed of the TF coil is something called laser welding, which is conducted at various points in the manufacturing timeline. This was another process that shined a light on the expertise of Keihin Product Operations and its past experience with manufacturing large-scale equipment. They were, for example, able to design a welding machine specifically for the purpose of manufacturing TF coils.
“Even with laser welding that’s extremely fine and precise, engineers still can’t escape the minute deformations caused to the parts by the welding process itself. We’ve been in full collaboration with our research centers and the welding department on-site to make sure that these deformations are within range of the required precision. It’s impossible for us to do full-size trial production in terms of the entire TF coil we have to produce, but we’ve been doing actual-size trial production of the parts, going through our analyses and trying different welding sequences, different compositions for the jigs to keep the parts in place… Trial and error, over and over. The fact that we’re able to be this motivated and this confident in ourselves, even at this level of difficulty, all comes down to of those who came before us at Toshiba—their many, many endeavors and many, many achievements,” said Yoshizawa.
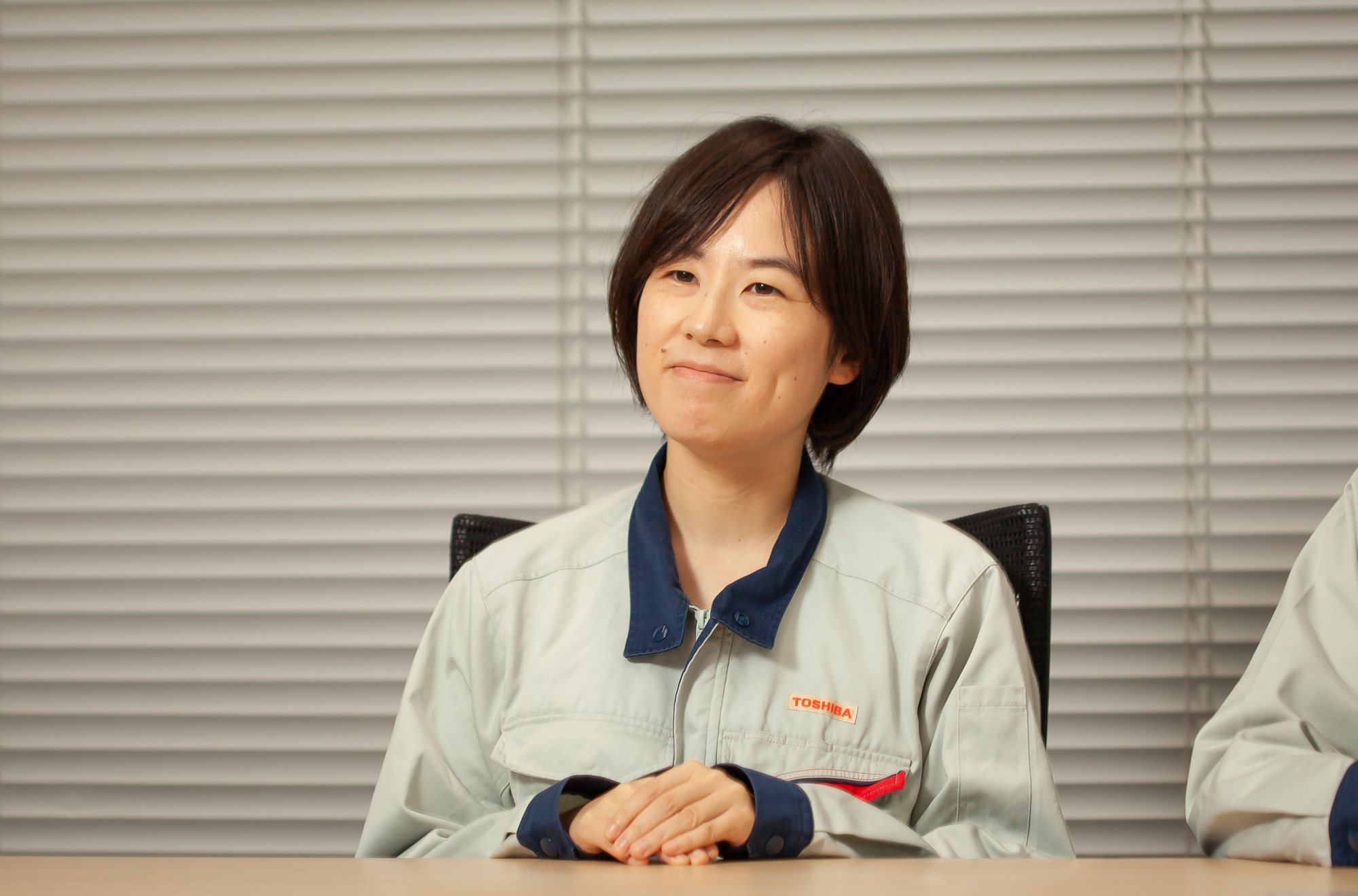
Sakaguchi was deployed to QST for two years. Her job has been to oversee the project from the outside, including negotiations with the ITER Organization. She uses Toshiba’s accumulated pool of knowledge in her design work, and has felt for herself the importance of Toshiba’s partnership with QST—an organization that exists at the cutting-edge of research into fusion power.
“It’s not like we can make one TF coil, then just make the second one using the same routine way. Every day we come across technological difficulties, to the point where they seem endless! But the work on-site stops for nothing and no one. We were able to complete the first TF coil, and overcame a lot of issues in that process, so we’re now able to recover from these issues much faster. The QST representative also comes to visit Keihin Product Operations almost every week, and is really passionate about working through the issues with us. The design team, the manufacturing site, the sales department, and the people at QST—we’re all working on this as one team,” said Sakaguchi.
All-Toshiba, all-Japan: All in on this next-generation energy source
This is a long-term project, with ITER’s First Plasma (start of operation) planned for 2025, and the actual fusion reaction to begin sometime in or after 2035—not to mention the fact that ITER itself is an experimental reactor. If the experiment goes smoothly, the next possible step would be the construction of a prototype reactor for fusion power.
“This is an all-Toshiba effort here at the technology development team for TF coil, and in fact this project as a whole has seen us all working together—everyone from design, manufacturing, and sales to those at QST—as a team. Toshiba has a long and illustrious history when it comes to the development of fusion technology, and our focus here is on taking this expertise from the past to the present, and then to the future,” said Suzuki.
“We’ve received a lot of praise from the QST representatives when it comes to the quality of our work. Our goal is to take the experiences and knowledge Toshiba has accrued from large-scale projects in the past, and use them here to maintain that trust, pass them down to the next generation—and to do all this in a way that would make our predecessors proud,” said Sakaguchi.
“This is my eighth year working with ITER. The winding pack that we’ve been working on only becomes a real product after it’s combined with the coil case. We still have such a long way to go before we complete all of the coils. Until the coils are installed on-site, until operation actually begins, until word goes around that ‘Hey, Toshiba’s coils were really good,’ we’d like to keep our focus, and work as hard as we can on this manufacturing process,” said Yoshizawa.
There’s still so much more to be done when it comes to fusion power, not just in terms of research, but also in terms of the design and development issues we face on-site. Fusion may be a “dream” energy source, a futuristic ideal, but ITER will be a massive step towards the realization of this dream. And when it happens, when the dream is realized, we’ll find that the leaders of this endeavor were those like the employees we interviewed here, that worked every day with their eyes fixed on that lofty goal, the promise to turn a dream into reality, and bring the future into the present.
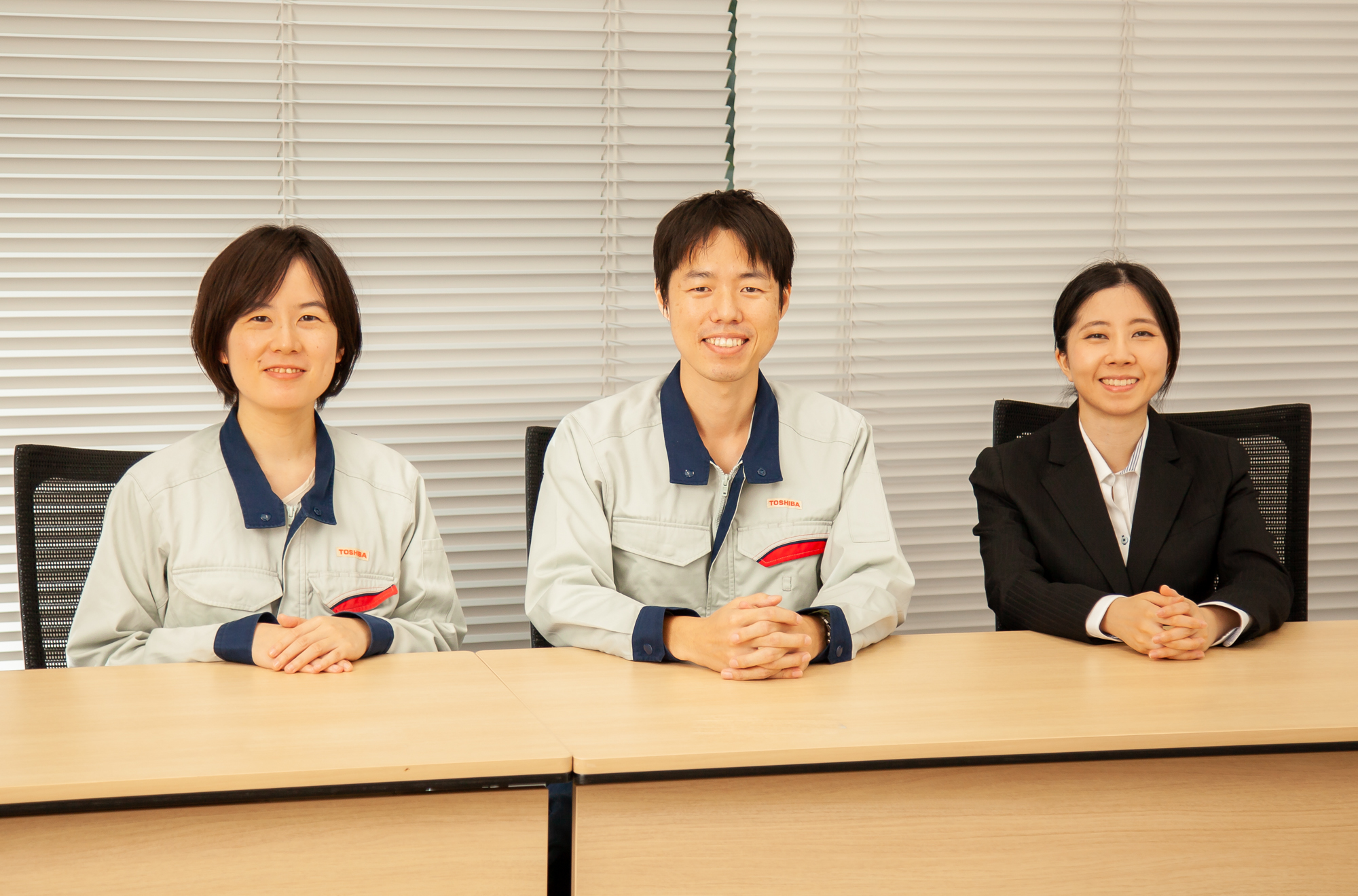
[Source]TOSHIBA CLIP (http://www.toshiba-clip.com/detail/8249) (Toshiba Corporation)