研究開発・技術の現場から
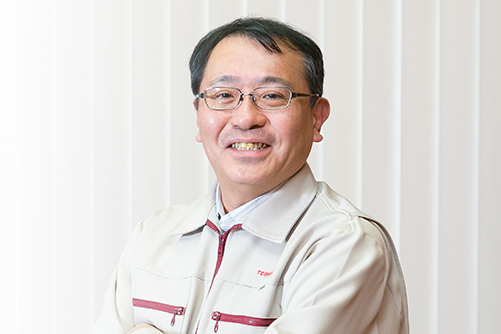
東芝グループの力を結集して取り組む、
製造現場の自動化・ロボット化
宮内 孝製品の多様化や製造プロセスの高度化の一方で、少子高齢化により労働人口が大幅に減少し、人材確保が一層厳しくなることが予想されています。こうした課題の解決のために、東芝グループでは製造現場が真にもとめる自動化機器・ロボットの開発と実用化を進めています。さらに最近は、ロボットの開発と活用を起点としたソリューション活動にも取り組んでいます。
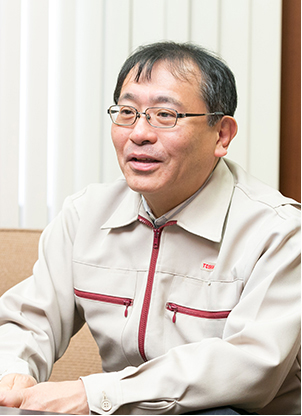
モノづくりの立場からお客様の要求に応えるために
多くのお客様に、製品を使って頂くためには、良いモノを、お客様が必要な時に、より適切な価格でお届けする必要があります。良いモノを作ろうとすれば、時間も労力もかかるので価格が上がりますし、すべての要求に応えることは簡単ではありません。解決策として、製品の価格を抑えるためにロボットを導入して自動化することで、作業の人件費を減らすことが考えられます。あるいは品質向上のために、より精度の高い装置を開発することも考えられます。しかし、ロボットや装置の開発にかける費用や期間を増やすと、結局コストが上がってしまいます。
例えば、電子基板にコネクタを挿入する作業は人間には簡単なことですが、ロボット化することは案外難しいのです。人間は目でコネクタの位置を見て、コネクタを指でつかみ、姿勢を合わせて、指で倣わせながら、カチっという感触を得るまで挿入します。これをロボットで実現するためには、多くの関節やセンサ、動かし方のプログラムが必要です。このようなロボット開発に挑戦することは魅力的ですが、その費用が得られる効果よりも多くなってしまう可能性があります。こうした時は、コネクタをはんだ付けに変更できないか、そもそもここにコネクタは必要なのか、あるいは作業が楽になる方法はないか、などを関係者で議論して最も良い方法を見つけ出します。多くの人と議論する中で、お客様の要求に応えられる解を見出していくのです。
課題の解決には、製造現場はもちろん、製品の開発者や設計者、営業や品質部門担当者とも議論します。難しい課題であればあるほど、狭い範囲の活動では解決が難しく、組織の力が必要になります。苦労はありますが、多くの人の協力を得て練り上げた製造ラインを作り、それが動き出して製品を産み出すときの喜びはとても大きいものがあります。
適切な方法を選ぶための考え方を共有
モノづくりの課題解決には多くの人が関わるので、様々な立場・組織の人と話を進めるにあたり、対象となる製造工程に適切な手段を選ぶ考え方を整理しました(図1)。横軸は加工点・作業内容の汎用度を、縦軸は人手作業の難易度を示し、4つの象限に分けています。
図1:製造工程の特性に応じた自動化
(引用:【東芝レビュー】VOL.73 2018年1月号(PDF形式:563KB))
第1象限は、人による作業が難しく、また特定製品の製造工程に限定された領域です。社内で開発した製造プロセスによる電池製造や、超電導など特殊な用途向けのコイルを作る工程などがあります。
第2象限は、人による作業が難しく、既に世の中に活用できる良い装置がある領域です。半導体製造における薄膜プロセス装置や、電子部品の実装装置がこれに相当します。自力で装置を開発することもできますが、時間や費用の圧縮を優先して既存の装置を選定・構成します。その場合も必要な機能を付加したり、一部を加工したりすることで、東芝ならではの生産ライン・装置に仕立てます。
第3象限は、人による作業が可能だが、自動化によって費用の低減や品質向上が期待される領域です。東芝グループ内の代表的な製造拠点を調査したところ、物品搬送、組み立て、検査などの工程は人による作業が多いことがわかりました。そこでこの分野について、ロボットや汎用部品を組み合わせて、費用を抑えた自動化を進めています。例えば既存品を活用したAGV(無人搬送車)や、様々な形状の品を持てる汎用性の高いハンドを開発し、各拠点に展開しています。
第4象限は、汎用度が低いために既存の装置も無く、自動化装置を開発するには費用と時間が必要になります。ですから製品設計を自動化しやすいように変更したり、人の作業をサポートする方法を考えたりします。
このマップを基とした自動化推進の考え方を東芝グループ内で展開し、製造工程の自動化、設備導入を進めています。
部品・ユニットの搬送を自動化する各種AGV
写真奥左より、アーム付きAGV1号機、高機能AGV、アーム付きAGV2号機
手前左より、ローコストAGV、同高可搬重量仕様
様々な形状のシールを貼り付けるロボット
根底にあるのは「いいモノを作りたい」という情熱
私自身は入社後、製造装置の制御ソフトウェアの開発を担当していました。製造装置は、機構、電装、ソフトウェアでできています。当時、製造装置の設計は、機構の設計者が主導して進め、ソフトウェア技術者は設計に従って担当範囲を開発するのが一般的でした。いくつかの装置開発に携わる中で、装置設計の段階からソフトウェア技術者が参加すればもっと良いモノを早く作ることができると感じていました。そこで、ソフトウェア技術者が最初の設計段階から携わることを提案し、組織を越えた生産性向上の取り組みを進めてきました。
また、装置の種類によりソフトウェアの作り方が異なっていましたが、これを標準化し、ソフトウェアの再利用性を高め、他の装置のソフト開発に容易に参画できるようにすることで、開発期間の短縮と品質の向上を図りました。
さらに装置の3DCADデータと制御ソフトウェアを組み合わせることで、パソコン画面上で仮想的に装置の機構を動かすシステムを開発しました。これにより、機構などのハードウェアが完成する前に、ソフトウェアの検証作業を実施することができるようになり、開発期間を3割以上短縮することができました。これは、サイバーフィジカルシステムの先駆けと言える試みだったと思います。
こうした初期の設計段階での機構とソフトの融合、標準化、開発プロセスの改善などにより、液晶パネルの製造装置、半導体の工程内検査装置、DVD用光学素子の実装・検査装置、医用機器の実験装置、3D液晶ディスプレイの製造装置、携帯電話用のガラス貼合せ装置などを開発してきました。多数の装置開発に関わることで、自分の専門分野だけでなく、機構をはじめとするハードウェア設計や、様々な製品の構造や造り方について、深く広く知識を得たことで、装置に直接関わる人だけなく、製品設計や製造現場の人々とも様々な議論ができるようになりました。
技術者や研究者は、持ち場や方法論が異なっても、「いいモノを作りたい」という想いは共通です。それぞれ専門性が高い者同士、互いの主張がぶつかる場面もあります。それでも常に課題の解決に向けて諦めずに議論します。こうした場面でも東芝グループの人々は非常に前向きで、組織や職能に関わらず相手の意見に耳を傾け、それを受け入れる度量の広さがあります。互いに納得できるまで徹底的に話し合える。それが東芝の強さだと感じています。
東芝の技術力と総合力で新たな価値をつくりたい
これまで日本の企業は産業用ロボットの開発と活用で世界をリードしてきましたが、最近は新たな局面を迎えています。モノづくりの現場では、製造プロセスの高度化や製品の多様性が拡大することにより、従来の単純作業型のロボットでは対応できないことが増えてきました。もっといろいろなことを賢くできるロボットが必要になってきているのです。さらにロボットは作業をすると同時に、データを数値的に収集・分析することができます。AIやIoTと組み合わせることで、お客さまの要望に柔軟に対応する、不良の発生を予防するなど、今まで以上にきめ細かなサービスや効率化につなげることが期待されています。
少しでも早く、多くの方に新しいロボットや新しいロボットを活用したソリューションをお届けするために、東芝グループでは、研究所や事業部門、工場のメンバが、横断的に力を合わせた活動を始めました(図2)。これが、ロボット技術横断PJです。ここでは製造分野だけでなく物流、流通分野の自動化を進めるロボットも開発しています。様々な組織に所属するメンバが、お互いに刺激しあいながら、ロボットを通じて新しい時代を創るという夢に向かって進んでいます。
図2:東芝グループ内の関連部門が連携してロボット技術横断PJを推進
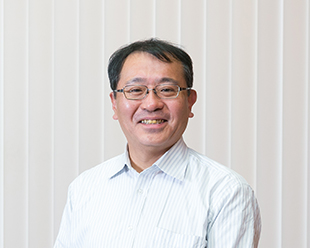
宮内 孝
- 分野
- ロボティクス、メカトロニクス
- 所属研究所
- 研究開発本部 ロボット技術横断プロジェクト プロジェクトリーダー
生産技術センター 副所長(自動化推進責任者) - 登録特許
- 国内外登録特許:28件(液晶パネルの実装方法と装置、検査、DVD光学素子の実装方法と装置、3次元画像装置の製造方法と装置など)
- 論文
- ”実機レス検証技術の設備制御ソフトウェア開発への適用”. 宮内 孝、 小林 大介、 宮本 雄介、 藤田 和明. 日本機械学会 設計工学・システム部門 講演論文集.(2009年)
”微分干渉顕微鏡画像を用いた液晶ディスプレイ実装部の自動検査技術”. 宮内 孝 ・ 鈴木 智夫 ・ 妹尾 勝己.
精密工学会 View2010 講演論文集.(2010年)
”グラスレス3D-LCDの貼り合せ技術”. 宮崎 健太郎、 宮内 孝、 成谷 元嗣、 守田 健. 日本機械学会 設計工学・システム部門 講演論文集.(2013年)
※2018年5月15日公開。ページの内容は公開当時のものです。