Evolving Model-based Development to enable
Collaborative Digital Prototyping across Corporate Boundaries
VenetDCP provides an environment that connects large numbers of simulation models and varied development tools.It realizes collaboration cyberspace of model-based development (MBD) across multiple teams and companies.
For example, in the development of complex vehicle systems such as autonomous driving which link together numerous sub-systems, VenetDCP enables large-scale simulations from the product’s planning phase to the testing phase. This can reduce reworking of the design, improve quality, and improve productivity. Toshiba Digital Solutions propose a new work style of product and service development through the sharing of design information and knowledge in cyberspace.This new workstyle can promote collaborative development across various industries from manufacturing to social infrastructure, energy and more.
Challenges and Solutions in Collaborative Digital Prototyping
Collaborative digital prototyping process often involves large-scale co-simulations that combine multiple models owned by different companies and teams.
There are many barriers to accomplishing this. VenetDCP overcomes these issues by combining models and simulation tools owned by product manufacturers and part suppliers in “distributed” arrangements, connecting them as one and “coupling” them in cyberspace.
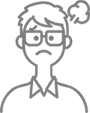
Connecting simulations
The migration and connection work required to combine multiple models is both labor intensive and costly.
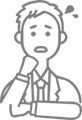
Protection of confidentiality
Many companies possess confidential models that they do not want to show or provide to other companies.
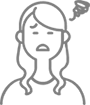
Development team organization & environment
Development through collaborative evaluation at multiple locations can be inefficient because it is affected by differences in development styles, such as locations or schedules.

High interconnectivity
Bus connectors reduce man-hours of work connecting different models and tools.

Protection of model confidentiality
Cross-company distributed co-simulation prevent confidential models from being disclosed to other companies.

Automated operations
Co-simulation work can be performed from a single location by operating tools at other locations through remote batch processing.
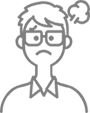
Connecting simulations
The migration and connection work required to combine multiple models is both labor intensive and costly.
High interconnectivity
Bus connectors reduce man-hours of work connecting different models and tools.
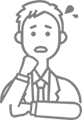
Protection of confidentiality
Many companies possess confidential models that they do not want to show or provide to other companies.
Protection of model confidentiality
Cross-company distributed co-simulation prevent confidential models from being disclosed to other companies.
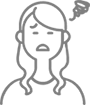
Development team organization & environment
Development through collaborative evaluation at multiple locations can be inefficient because it is affected by differences in development styles, such as locations or schedules.
Automated operations
Co-simulation work can be performed from a single location by operating tools at other locations through remote batch processing.
Secured co-simulation in cyberspace enables model exchange and design collaboration!
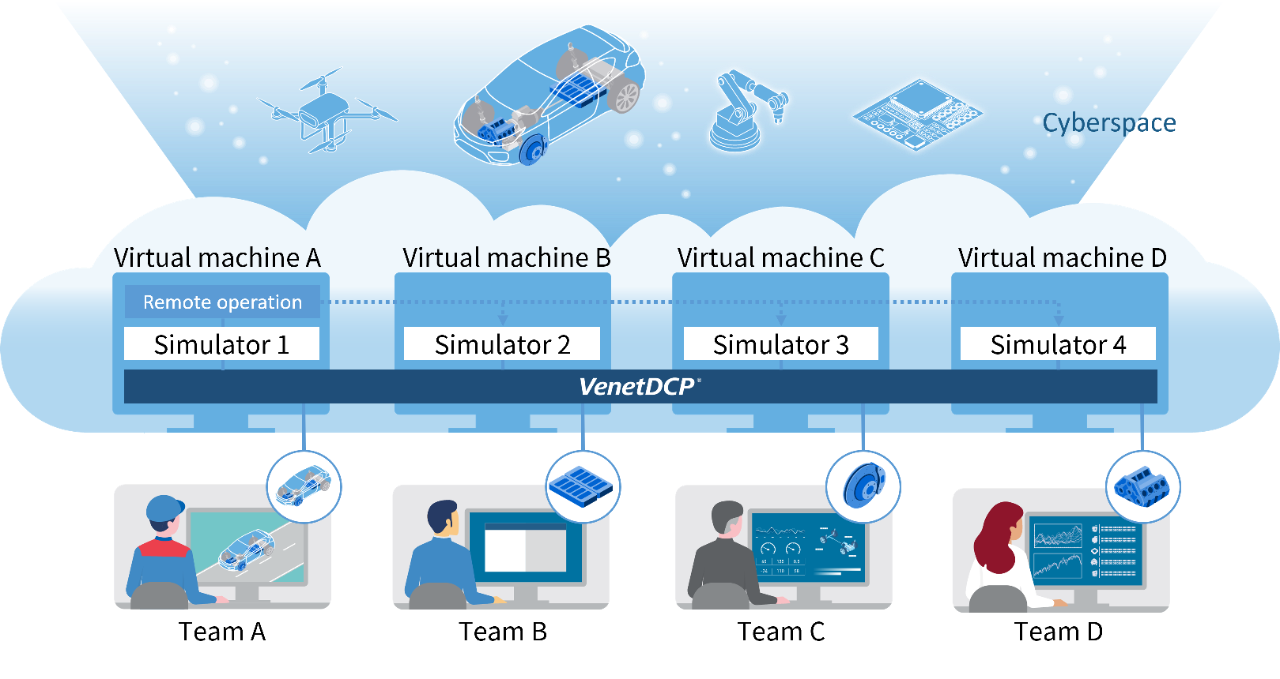
* Distributed co-simulations can be executed in the same way in an on-premises environment or a cloud environment.
In cases of cross-company and multiple design team co-simulation, use of a cloud environment is highly recommended due to the communication speed and security (including model confidentiality).
Numerous experiences in cross-tool coupling
Supported simulators
Altair Twin Activate, ANSYS Twin Builder, AVSimulation SCANeR, AVL CRUISE M, Dassault Systèmes Dymola, dSPACE VEOS, dSPACE SCALEXIO, dSPACE MicroAutoBox, ESI SimulationX, ETAS COSYM, Gamma Technologies GT-SUITE, IPG CarMaker, MathWorks Simulink, Modelon Impact, National Instruments LabVIEW, OpenModelica, Python, Siemens Simcenter Amesim, Siemens Simcenter STAR-CCM+, Unreal Engine, Vector CANoe
Supported cloud services
Microsoft Azure(Microsoft), AWS(AWS), Moderix (Nexty Electronics)
* The names of products and services above are registered trademarks or trademarks of those respective companies in Japan or other countries.
Watch Video
Technology summary of VenetDCP
(Video - 10:36)
How to use VenetDCP
(Video - 11:11)
Use case of distributed co-simulation
(Video - 7:13)
News
Related Links
(Japanese Only )
- VenetDCP™ is a registered trademark or trademark of Toshiba Digital Solutions Corporation in Japan and other countries.