High-voltage Direct Current (HVDC) Power Transmission Reaches across 400 km to Link Italy and Montenegro <Part 1> Deciding on a Method That Lays a Groundwork Focused on the Future
High-voltage Direct Current (HVDC) Power Transmission Reaches across 400 km to Link Italy and Montenegro
<Part 1> Deciding on a Method That Lays a Groundwork Focused on the Future
Connecting the 400 km from Italy to Montenegro undersea
Lacking in energy resources, Italy currently relies on importing large amounts of electrical power from other countries – its shortage of domestic energy must be solved. Furthermore, in many cases, from such perspectives as the environmental issues in Europe, including Italy, it is difficult to construct new power plants. For that reason, it is required to reduce the risk of power shortage by increasing the number of options for importing sources. This time, it has become necessary to construct a power plant in Montenegro and supply electricity to Italy.
Across the Adriatic Sea, the distance between Cepagatti, Italy and Kotor, Montenegro is approximately 400 km. First, at the Montenegrin transformer facility, as much as one gigawatt of power is converted from alternating current to direct current, which then passes through the undersea cables to the Italian transformer facility where the direct current is converted back to alternating current.
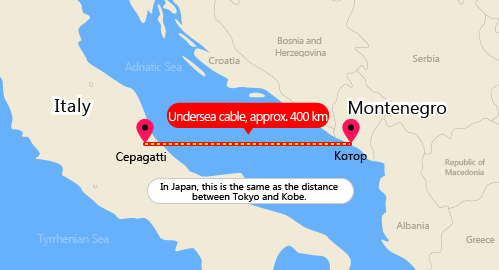
The only enterprise in Japan to bid on this colossal project was Toshiba, Japan's leader in DC power transmission projects. The achievements of delivering AC-to-DC converters for HVDC power transmission systems in which undersea cables have been used between Hokkaido and Honshu, as well as Shikoku and Honshu, were highly acknowledged, and, as a result, Toshiba received the order.
Method Analysis Creates Awareness of the Current Situation That is Fundamental to the Project
Part one of our story introduces our efforts surrounding the project for DC power transmissions between Italy and Montenegro and describes the "Method Analysis", "System Study", and "Functional Specification" we carried out after the bid was received.
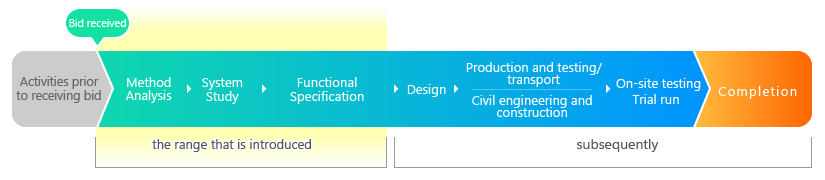
The current contract has been bid as "full turnkey" (a contract in which a single contractor does all of the work – from design to the procurement of equipment, resources, and workers, as well as construction and trial runs, and undertakes the responsibilities for performance guarantees, warranties, and delivery). This means that the technologies that Toshiba has can be applied, in their entirety, in order to create power converter stations. This project involves every bit of technology, and encompasses converters, protection and monitoring control systems, transformers, switchgears, arresters, as well as Toshiba's business organization for its electric power distribution system.
The first thing that was done after finalizing the received bid was the "Method Analysis". We carried out analyses to substantiate what kind of functions or specifications are required for a power converter station, based on information about the power grids in Italy and Montenegro. Afterwards, we confirmed the goal of the whole project by surveying and analyzing the entire power converter station. It is crucial to extract potential problems and issues in the first stage. Our awareness of the current situation at this stage was the whole foundation for how to proceed with the project.
Discovering What the Client Truly Requires
Once the Method Analysis was finished, we set about the "System Study" step, in which we laid out and inspected the facilities. First and foremost, we had to give the clients the numbers they needed. We held multiple consultations to establish carefully what we needed to do to achieve the requirements and what objectives existed along the way. We established the ratings for each piece of equipment, which would be supporting as much as 1 GW of high power, based on the stresses of the voltages and currents applied to it.
However, power is not the only thing that we must consider. While also keeping in mind the effects that electric fields and magnetic fields have on humans and how we should limit the generation of noise pollution and electrical noises, we decided on layouts for physical equipment. We must also be prepared for problems or unforeseen situations. Other important elements we needed to satisfy were having a level of reliability required for the frequency of malfunctions that could occur due to the stress applied to the equipment, as well as a system response time that could increase the speed to provide support if a neighboring facility were to go offline. It is precisely because this system is to always continue running, over a long period, that there are items that we must bear in mind; as a result, the most important step, involved from the very foundation, is the "System Study".
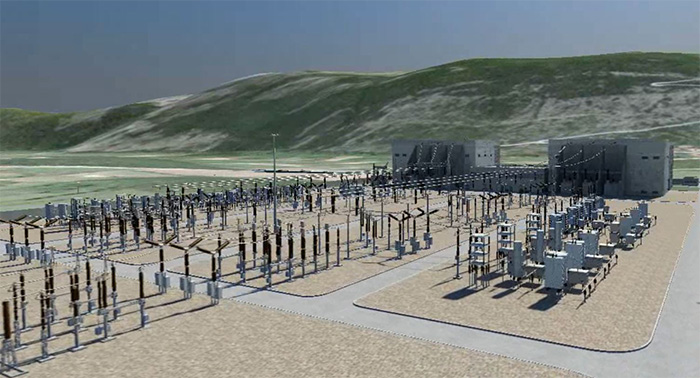
Engineers from both Italy and Japan worked together on the System Study. These engineers seemed to progress despite having to repeatedly overcome such obstacles as communication between the two countries and creating software to analyze data in the different formats provided by the client.
We moved on to the "Functional Specification" step to further apply the specifics of the entire layout, derived from the System Study. Envisioning the conditions in which the equipment would actually be used, we made a proposal for the interfaces and links for each piece of equipment. In this stage, we decided on "the equipment's user-friendliness" and established the details of the equipment's implementation. We would not be exaggerating if we said that the entire project is coming together seamlessly, including the actual operations, as we enter this phase of the process.
Establishing the Client's Specifications Leads Us to the "Design" Phase
Engineers concerned with steps related to the these specifications said, "We are glad to have been connected, from the start, to such a large-scale project that transmits DC power, at as much as 1 GW of high power, between two different countries. We are grateful to have participated in a project that could be done thanks to Toshiba".
With the specifications practically decided, we started to design the equipment for the project to reliably transmit power levels as high as 1 GW of DC power across a distance of nearly 400 km. Next time, we will report on new challenges that occurred in "Building to Specifications" as the project took shape, such as design and production, as well as the processes of the project, including performance tests at the site at which all the efforts up to now have been tested.