Toshiba Digital Solutions is working to realize Cyber-Physical Systems (CPS) and commercializing an innovative solution to the automobile industry, in which global competition is intensifying. Model-based development is becoming popular among automobile manufacturers and automotive components suppliers. "Distributed Co-Simulation Platform" advances the model-based development and makes it possible to share "digital prototype" of vehicle across various design teams in OEM companies and suppliers. It also makes it possible to perform a vehicle test of large-scale and complex automotive embedded systems, such as autonomous driving and advanced driver assistance system, with a virtual simulation in the cyber working space. "Distributed Co-Simulation Platform" is an embodiment of digital twins for automotive system development which can eliminate the costly reworking and improve the quality and productivity dramatically. In this article, we present this innovative platform, "Distributed Co-Simulation Platform" and its managed services.
The rapid popularization of model-based development
In recent years, vehicle driving support systems such as automated driving and advanced driver assistance systems (ADAS) lead to increase the number of electronic control units (ECUs). Besides, the scale of control software is getting larger and larger. Vehicular motions such as driving, turning, and stopping are implemented by automotive components such as engines, accelerators, and brakes. These physical components have their own ECU and control software. Every year, their performance is upgraded and multi-functioned.
According to a governmental study, in the last ten years the percentage of electronic parts in automotive components has doubled. In around 2000, the software used in one vehicle consisted of roughly one million lines of code. According to recent survey, the number is now over 100 million. The number of components and software which need to be developed continue to grow, meanwhile the automotive component suppliers are required to shorten delivery times while keeping the high-quality.
Model-based development (MBD) has rapidly grown in popularity as a powerful method of automotive system development. MBD uses a numerical vehicle model to represent real-world phenomena so that product design and evaluation can be performed using virtual simulation on a computer (in cyberspace). It is the embodiment of digital twins of cyber-physical systems. In MBD, numerical vehicle model is designed at the very early stage of defining the product specification. Then the numerical model is evaluated and revised repeatedly. Simulation can make the physical and virtual world closer. MBD approach has the advantage of enabling to speedy and accurate performance evaluation that is like performing evaluation using real vehicles and real devices.
The conventional approach of control software development requires structural design, module design, detailed design, and a lot of tests with real vehicles and devices so that the specifications are verified. With MBD approach, control software is automatically generated from the numerical vehicle model after it has fully tested and verified with the virtual simulation. It has dramatically speeded up the development and reduced human errors such as misinterpretation or misunderstanding of specification and bugs in the program. MBD is now widely used to stabilize quality while suppressing the increase in development costs.
Click here to move to the top of this page.
Going beyond the limits of model-based development
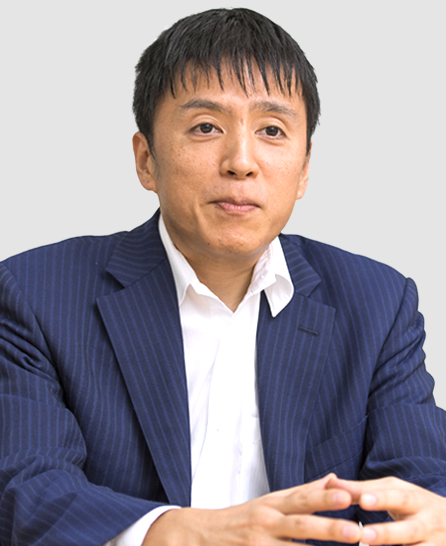
In recent years, the automotive systems have become more advanced and reliability of individual component has come to have a greater impact on overall reliability of vehicles. Even if an individual component has been tested and confirmed to follow the specifications, the total vehicle system which consists of plural components often causes unexpected failures due to factors such as driving patterns, road surface conditions, vehicle body structure, vehicle weight, or characteristics of each component.
Furthermore, advanced and complex functions such as autonomous driving and ADAS need huge numbers of integration test which must work together with the engine, power train, and chassis components. At this time, OEM companies spend a lot of time on vehicle test traveling to achieve optimal performance and high safety before putting it on the market. If some failures are found in this final stage of development, it may cause much rework and time loss.
Many of these problems could be resolved by collaborative "digital prototyping" which means that manufacturers and suppliers cooperate in performing vehicle integration test on a cyberspace during the development phase. Collaborative digital prototyping can be realized by exchanging the models of vehicle component among companies and design teams of vehicle development.
However, the model exchanging among OEM and suppliers has its own challenges. Models often have confidential information including intellectual property of the company, so that such confidentiality should be ensured in the model exchanging. Furthermore, connecting many components of models and signals often requires significant time and effort. There is also risk of power shortage in simulations of all models connected to a single simulator (Fig. 1).
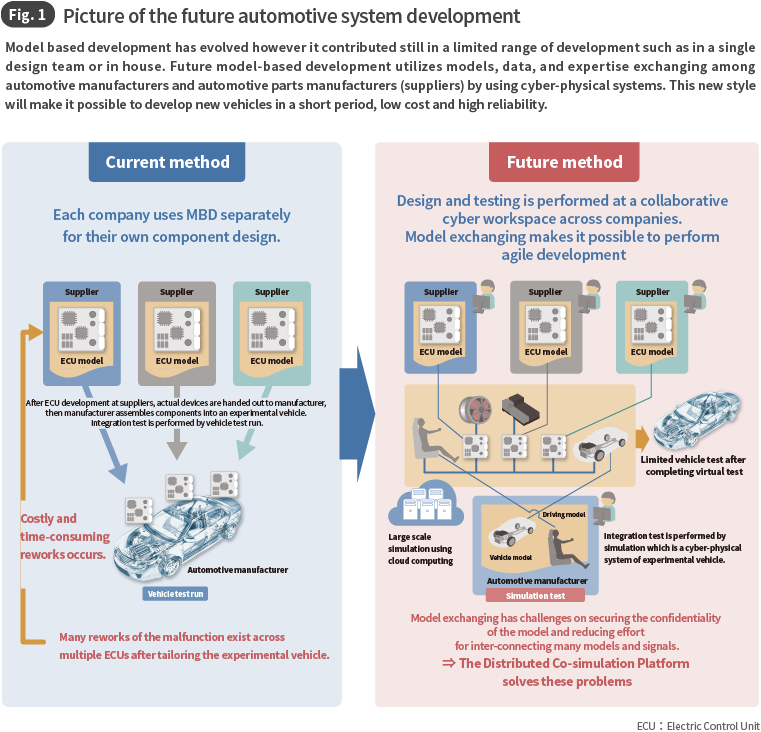
That's why Toshiba Digital Solutions developed the “Distributed Co- simulation Platform”.
Click here to move to the top of this page.
Minimizing vehicle test process and reducing development time
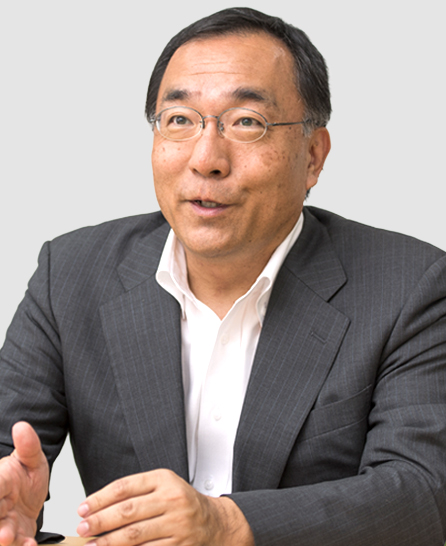
The Distributed Co-simulation Platform enables to connect various models and tools owned by separate teams and companies over the internet and compose a cyberspace for integrated test.
This platform doesn't need to collect any model which contains confidential design information. It connects simulation tools, then only model operation data is shared with other teams. Data necessary for testing and evaluation is shared via a network. It enables to perform collaborative test by companies that are physically far from each other. Distributed Co-simulation platform can connect various commercial simulation tools each other such as MATLAB®/Simulink® by The MathWorks, Inc.
The platform generates communication bridges based on the vehicle communication specification sheet. Models can be connected by these bridge parts of model. The user can connect their models with a single-click operation. The platform uses in-vehicle network simulator "Venet" as the virtual communication bus for co-simulation. "Venet" has much experience in automotive industry. As Venet can simulate CAN network which is an industrial standard of in-vehicle network protocol. Venet performs accurate simulation of CAN protocol bus and enables to evaluate loads, throughput and delay in in-vehicle network communication.
Distributed simulation can build a simulation for a larger scale purpose by combining and synchronizing several simulations. Distributed simulation makes it possible to perform high-speed and large-scale vehicle simulation. It eliminates concerns about simulation stopping due to the large consumption of memory and computing resources. The platform also supports to use cloud server as the environment for distributed parallel simulation. Instead of connecting simulators and models to remote company sites via LANs, higher speed and secure simulations can be performed by connecting models and simulators on the cloud (Fig. 2).
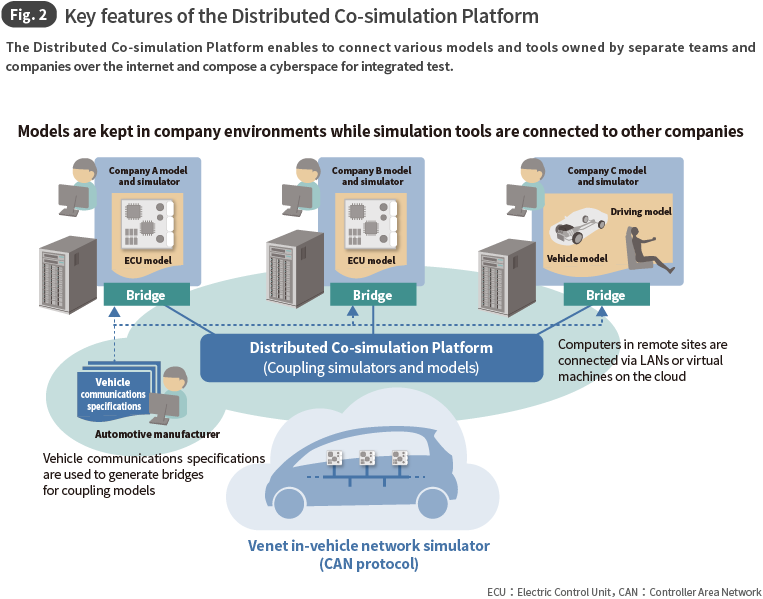
In the past, model based development has implemented still in a limited environment such as in a single design team or in house. Distributed Co-simulation Platform offers an innovative environment to perform collaboration of model based on development between manufacturers and suppliers or design teams. This solution filled with our experience and expertise fuses the physical and cyber spheres at a high level.
The Distributed Co-simulation Platform realizes CPS for the automotive system developments through the collaborative digital prototyping between manufacturers and suppliers. It has drawn attention of the automotive industry, and we feel that it will become a powerful platform for our customers who seek to strengthen capabilities for their development.
We are certain that model-based development using cloud computing will become popular style and that distributed co-simulation will be necessary. We are creating managed services that can provide optimized operation environments to automotive manufacturers and numerous suppliers.
We are doing our utmost to contribute to the automotive industry, which continues to pursue safety, comfort, low energy and high-performance mobility.
* MATLAB and Simulink are registered trademarks or trademarks of The MathWorks, Inc. in the U.S.
*
The corporate names, organization names, job titles and other names and titles appearing in this article
are those as of October 2019.
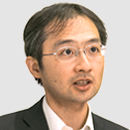
