導入事例とユースケース
自動車メーカーや設備メーカーでのユースケースをご紹介します。
他にも様々な業種・業務でのユースケースがありますので、詳細についてはお問い合わせください。
株式会社サンテクノス様 事例
コンクリート製品型枠及び関連機械を製造販売しているプラントメーカーである株式会社サンテクノス。市場のニーズに合わせて多種多様な製品やサービスをグローバルに展開するため、業務効率化と品質向上に取り組んできた。検査業務においては、目視検査にかかる時間の短縮や手戻り率の削減を目指し、デジタル技術の活用検討を進めてきた。そこで導入したのが、3D CADデータを活用した検査が可能な「Meister MR Link」だ。
Before
これまで、製品の品質検査は、穴の位置の違いや取り付け部品のずれなどを最終工程で目視で行ってきた。
そのため、上流工程に起因する異常が発生すると、莫大な修復作業コストが必要となっていた。また、検査を行うための準備や作業負荷も高かった。
After
Meister MR Linkの導入により、上流から最終工程まで手軽に検査が行えるようになった。
これにより、品質異常が次工程に流れる前にすぐに発見可能となり、修復コストを削減。また、現場で品質異常箇所をタブレット上で簡単に確認できるため、作業負荷の軽減につながった。
- 計測しにくい箇所のダブルチェックとして
使用することにより検査時間を短縮 - お客様からのクレーム減
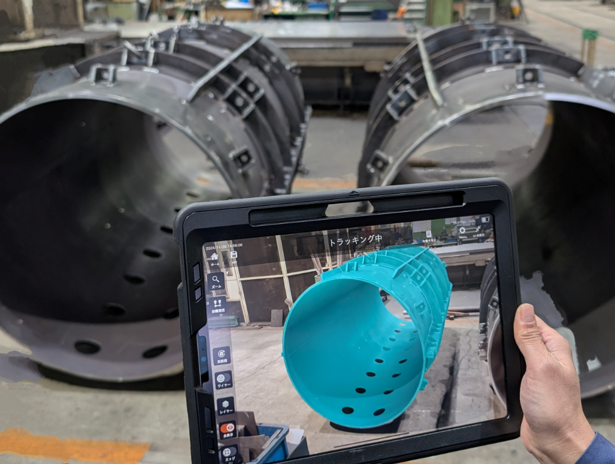
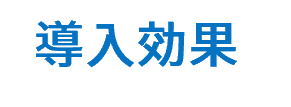
- 計測しにくい箇所のダブルチェックとして使用することにより検査時間を短縮
- お客様からのクレーム減
お客さまの声
「Meister MR Link」の導入により、これまで課題であった最終工程で発生する品質異常とその修復工数が大きく削減されました。また、簡単に導入することができ使いやすい点にも満足しており他の検査にも早速適用したいと考えています。
(株式会社サンテクノス 代表取締役社長 小山 剛器 氏)
COMPANY PROFILE
会社名 株式会社 サンテクノス
(URL:https://www.suntechnos.co.jp/)
※株式会社サンテクノス公式サイトへ遷移します。
設立 昭和21年11月15日
会社名 株式会社 サンテクノス
(URL:https://www.suntechnos.co.jp/)
※株式会社サンテクノス公式サイトへ遷移します。
設立 昭和21年11月15日
代表者 代表取締役社長 小山 剛器
事業概要
コンクリート製品型枠及び関連機械を製造販売しているプラントメーカー
代表者 代表取締役社長 小山 剛器
事業概要 コンクリート製品型枠及び関連機械を製造販売しているプラントメーカー
ユースケース
溶接打点の品質チェック
サプライヤーから受け入れた部品にタブレットをかざすだけで打点検査ができるため、作業時間短縮を短縮しガバリ作成が不要になります。

検査治具(ガバリ)を実物と重ねあわせて品質確認
- ガバリ作成に時間がかかり設計変更のたびに修正が必要になる
- 見比べ作業のため作業の抜け漏れや手戻りが発生しやすい
- 新人など経験の少ない作業員は時間がかかり、品質がバラバラになりやすい
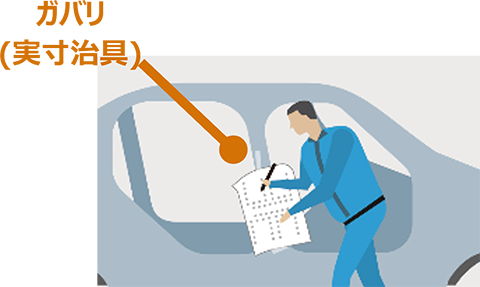

実物に3Dモデルと打点データを表示して検査
- タブレット画面上で見比べ作業を行うことでガバリ作成が不要になる
- 現場で実績登録からレポート業務まで行うことで作業効率が向上する
- 作業結果の可視化により作業の抜け漏れや手戻りが削減できる
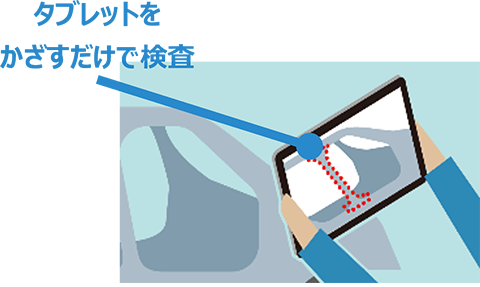

検査治具(ガバリ)を実物と重ねあわせて品質確認
- ガバリ作成に時間がかかり設計変更のたびに修正が必要になる
- 見比べ作業のため作業の抜け漏れや手戻りが発生しやすい
- 新人など経験の少ない作業員は時間がかかり、品質がバラバラになりやすい
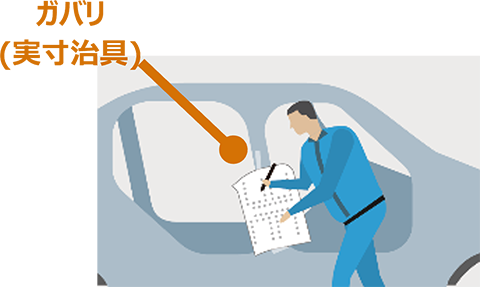

実物に3Dモデルと打点データを表示して検査
- タブレット画面上で見比べ作業を行うことでガバリ作成が不要になる
- 現場で実績登録からレポート業務まで行うことで作業効率が向上する
- 作業結果の可視化により作業の抜け漏れや手戻りが削減できる
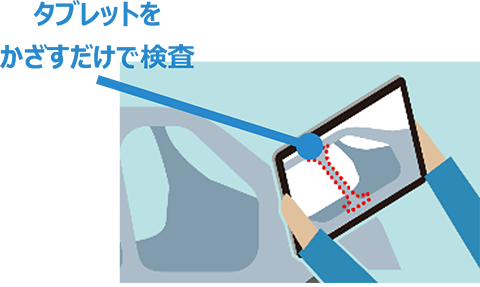
4人で行っていた作業が2人で対応可能に
基板の良品判定
検査から入力作業までタブレット上で完結するため、基板の全数検査をに要する時間が大幅に削減します。

図面との比較で全数実物チェック
- 現場で全数チェックするため作業負荷が高い
- 紙情報をもとにした作業になるので抜け漏れや手戻りが発生する
- 手書きした作業をPDFに記録するのみでデータの活用ができていない
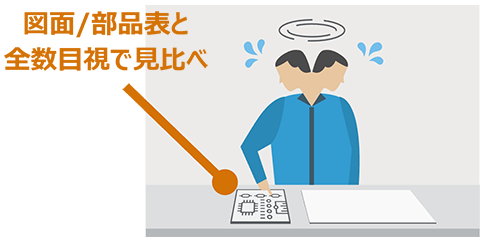

タブレット上で検査業務が完結
- タブレット上で比較作業と結果入力がまとめてできることで検査にかかる時間が短縮ができる
- 作業に不慣れな人でも直感的に作業が行えるため品質が平準化できる
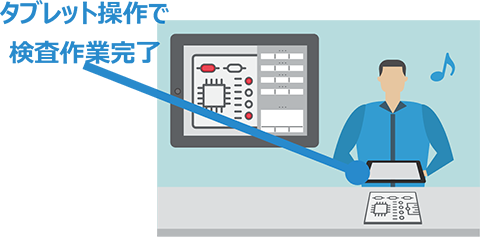

図面との比較で全数実物チェック
- 現場で全数チェックするため作業負荷が高い
- 紙情報をもとにした作業になるので抜け漏れや手戻りが発生する
- 手書きした作業をPDFに記録するのみでデータの活用ができていない
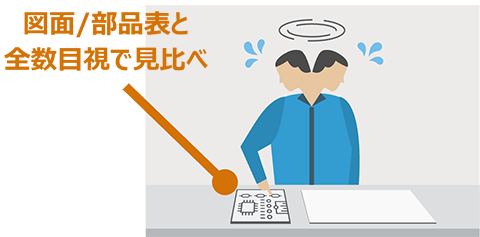

タブレット上で検査業務が完結
- タブレット上で比較作業と結果入力がまとめてできることで検査にかかる時間が短縮ができる
- 作業に不慣れな人でも直感的に作業が行えるため品質が平準化できる
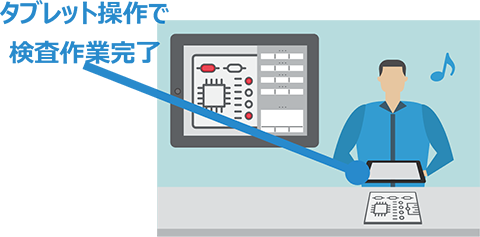
1基板あたり5~6時間かかっていた作業が1時間弱に短縮、チェック漏れ“0”に
製品の出荷検査/部品検査工程
商品出荷や工程完了時にタブレットをかざすだけで外観チェックができるため、検査時間の短縮と検査漏れの抑制がはかれます。

図面を見ながら出荷前に目視で全数チェック
- 図面との見比べ作業のため確認が漏れる
- 検査数が多いと全ての製品を同じ品質で検査できない
- メジャーやノギスを使って位置やずれ量を計測している
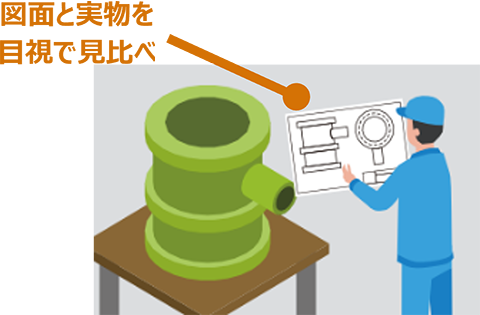

タブレットをかざせば外観チェックが完了
- 未チェックデータがフォローされるため検査漏れを抑制できる
- 画面のチェックだけで検査できるため効率よく進められる
- あるなしだけでなく部品表にしかないCAD以外のデータも確認できる
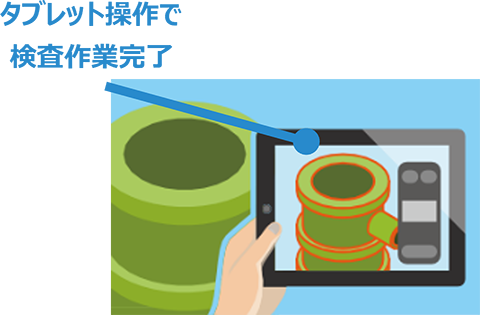

図面を見ながら出荷前に目視で全数チェック
- 図面との見比べ作業のため確認が漏れる
- 検査数が多いと全ての製品を同じ品質で検査できない
- メジャーやノギスを使って位置やずれ量を計測している
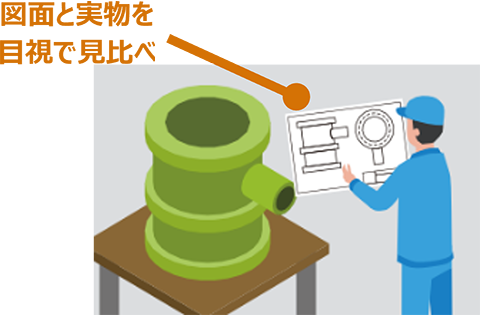

タブレットをかざせば外観チェックが完了
- 未チェックデータがフォローされるため検査漏れを抑制できる
- 画面のチェックだけで検査できるため効率よく進められる
- あるなしだけでなく部品表にしかないCAD以外のデータも確認できる
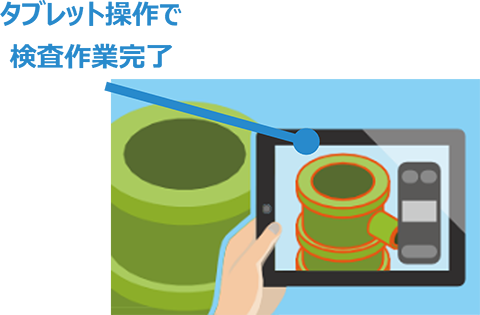
全数チェックが可能になり、手戻りが“0件”に
製品メンテナンス工程
金型などの製品メンテナンス時に加修箇所の指摘内容と位置情報を見える化することで、抜け漏れを防止に役立ちます。

メンテナンス情報は写真とレポートで記録・引継ぎ
- 事務所と現場を往復して加修の指摘箇所の確認・作業記録を行うため、レポート作成に時間がかかる
- 写真とコメントだけでは作業内容がわかりずらく手戻りが頻発する
- 紙情報をもとにした作業になるので抜け漏れが発生する
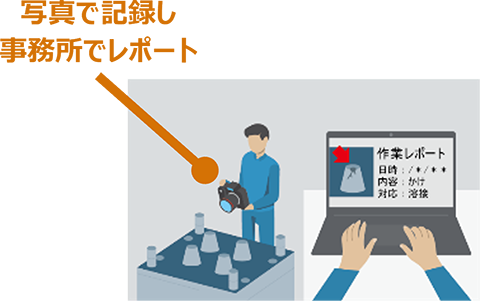

メンテナンス情報と位置情報を組み合わせて
一元化・共有
- 点検やチェックの記録だけでなく加修作業もすべて現場完結できる
- メンテナンス時の不具合や加修情報は関係部門にフィードバックすることで品質改善につながる
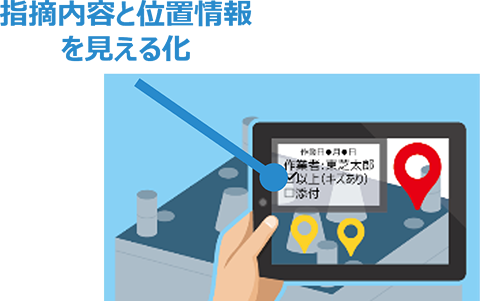

メンテナンス情報は写真とレポートで記録・引継ぎ
- 事務所と現場を往復して加修の指摘箇所の確認・作業記録を行うため、レポート作成に時間がかかる
- 写真とコメントだけでは作業内容がわかりずらく手戻りが頻発する
- 紙情報をもとにした作業になるので抜け漏れが発生する
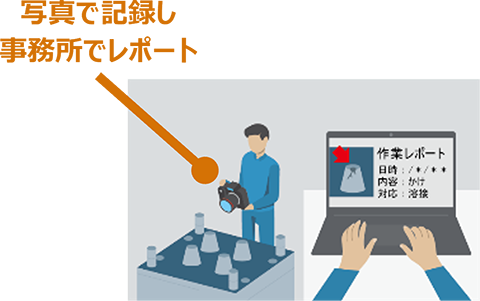

メンテナンス情報と位置情報を組み合わせて一元化・共有
- 点検やチェックの記録だけでなく加修作業もすべて現場完結できる
- メンテナンス時の不具合や加修情報は関係部門にフィードバックすることで品質改善につながる
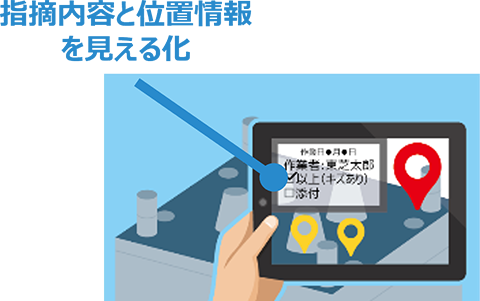
3人で行っていた作業が1人で対応可能になり、抜け漏れ“0”に
資料ダウンロード
商品紹介のリーフレットをダウンロードいただけます。
関連リンク
産業領域でのAR・MRの活用に向けて、長年にわたり研究開発とグループ内での実証実験に取り組み、製造業ほか広い分野でご活用いただけるソリューションを提供しています。
設備のオペレーションやメンテナンスでの現場業務の効率化や、熟練者からの技術継承などの課題を、ARを活用したデジタルコンテンツで解決します。
東芝独自の良品学習方式を使ったAI画像検査技術により不良品の見逃しや過検出を抑えつつ、誰でも簡単に短期間で外観検査自動化を実現します。