東芝アナリティクスAI*「SATLYS(サトリス)」と結晶した、東芝の産業用AI技術。その粋を集めたともいえるのが、東芝メモリの四日市工場における先進の事例です。大容量、低価格などNANDフラッシュメモリに対する市場の厳しい要求に応え、積極果敢な設備投資と開発投資を進めていた同工場では、AIの活用による半導体製造プロセスの革新に着手しました。東芝の研究開発センターが持つ最先端のテクノロジーに、東芝デジタルソリューションズのものづくりとシステムインテグレーションに関する豊富な経験とノウハウ、幅広い業務知識、そして現場の運用を熟知する東芝メモリの現場知識を結集。高精度な「歩留解析」や「欠陥検査」を通して製造現場の業務をサポートし、品質・管理レベルの向上と生産の合理化を高度に両立する、世界でも類を見ない製造プロセスを実現しています。東芝のAIが生み出した「超スマート工場」をご紹介します。
* AI:Artificial Intelligence(人工知能)
1日20億件のビッグデータを
見える化
三重県にある東芝メモリの四日市工場は、世界有数のNANDフラッシュメモリの生産拠点です。東京ドーム約10個分という国内最大規模の敷地内に建てられた4棟のクリーンルームでは、合計すると200機種5,000台を超える製造装置が稼働。各棟の間はコンベヤで接続され、それぞれの棟にある製造装置の能力を相互に補完しあうという、世界で初の統合生産を確立しています。
東芝が開発したNANDフラッシュメモリは、スマートフォンやタブレット端末、エンタープライズサーバー、データセンターなどへの導入で、急速に需要を伸ばしてきました。中でも、メモリチップの中のセル同士の間隔を狭くする「微細化」、ひとつのセルにより多くの情報を入れる「多値化」、さらにはセルを積み上げる「積層化」など、最新の高度な技術を凝縮して生まれた3次元フラッシュメモリ「BiCS FLASH™」は、世界最高水準の性能を実現。デバイスの高機能化や4K動画の普及などを背景に、さらなる需要の拡大が見込まれています。
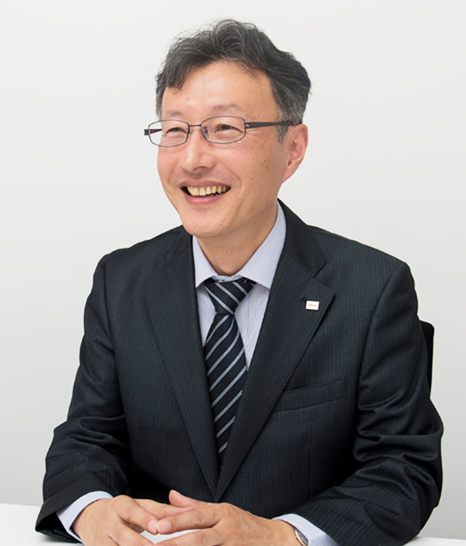
四日市工場では、小型・大容量・低価格という市場の要求に応えるため、徹底した生産の合理化に早くから取り組んできました。例えば、クリーンルームに設置された、半導体の回路を形成するウェハの搬送システムを完全に自動化。コンピューターによる集中制御を実現し、人手によるオペレーションを最小化したほか、搬送速度の高速化や微細化への対応期間短縮を図るなど、設備と開発への投資を積極的に行っています。
しかし、グローバルな厳しい競争に勝ち残っていくためには、歩留りを改善し、製品品質を高め、信頼性と安定性を最大限に向上させた生産・量産体制を築かなければなりません。そこで最初に取り組んだのが「ビッグデータの見える化」でした。
四日市工場では、5,000台以上の製造装置や数十品種/数万工程に対応した自動搬送システム、さらには検査装置、製品管理システムなどから、1日に約20億件を超える膨大なデータが発生しています。そこでこれら工場内のあらゆるデータ(ビックデータ)を統合データベースに収集し、装置の稼働率や生産ラップ、工程別の残分布などの項目別に、グラフや数表、ガントチャート*といった形で見える化。製造工程における問題の早期発見や、不良が発生した原因の特定などに役立ててきました。
*ガントチャート:工程管理のために作業の進捗を棒グラフなどで表わした図表
製品の品質と生産性の劇的な革新を
AIで目指す
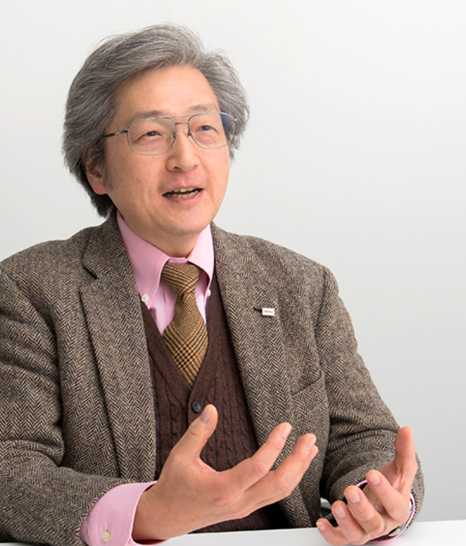
このビッグデータの見える化は、歩留りや品質の改善、生産リードタイムの短縮などに一定の効果をあげました。しかし、見える化されたデータを解釈し、最終的な判断を行っているのは熟練者をはじめとする技術者(人間)であり、その判断にかかる時間は従来と変わっていません。今後、3次元構造による大容量化に伴い製造工程が一層複雑になると、工場内で発生するデータの量は爆発的に増加していきます。人間の目視や経験によるデータ解析には限界があるため、ビッグデータを効率よく活用するための施策が必要でした。
そこで東芝メモリは、四日市工場にAI技術を導入したアナリティクス環境を整備し、ビッグデータを迅速に高い精度で解析することで、先端技術の速い転換サイクルや製造工程の複雑化や高度化に対応しようと考えました。しかし、それを東芝メモリだけで早期に実現することは難しい課題でした。
東芝には、AI技術をリードする研究開発センターがあります。先進のAI技術に日々取り組み、画像分類やビッグデータ解析のほか、学習用データの自動生成など、産業用途に最適化されたディープラーニングの基盤技術の高度化を早くから推進。AIを活用したさまざまな実証実験で、その効果を証明していました。
しかし、いかに優れたAIがあっても、これがそのままイノベーションをもたらすわけではありません。人とAIが協調して業務を遂行し、狙った効果を上げるためには、業務フローとシステムを再設計し、AIに最適化させる必要があります。
ここで力を発揮したのが、東芝デジタルソリューションズが持つ、ものづくりとシステムインテグレーションに関する豊富な経験とノウハウ、AI応用技術です。どのようなデータをどのくらい集めるべきなのか、各種解析においてどの程度の推論性能を求めるべきなのか、既存システムとどう連携させるべきなのかなど。現場の運用を熟知した東芝メモリと先進のAI技術を持つ研究開発センターの間に立ち、綿密な意見交換と密接なすり合わせをしながら、四日市工場に相応しいAIシステムのあり方を検討。導入のシナリオを策定し、アジャイル開発による効果検証と改善を繰り返しました。そして、導き出された適用方法や運用手法をシステムとして実現し、現場環境への展開を図ったのです。
高精度を極めた
「歩留解析」と「欠陥検査」
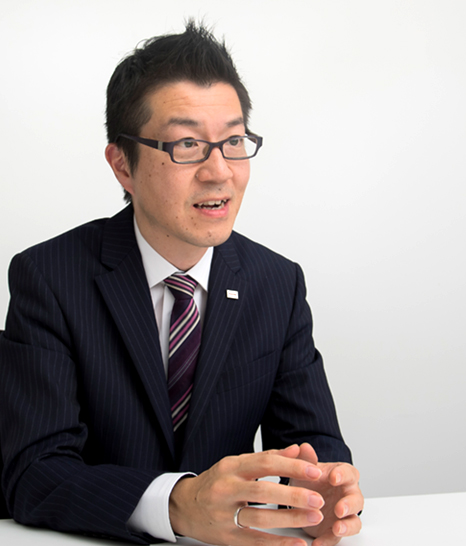
こうしてAI、現場、既存システムが三位一体となって連携する、画期的なシステムが実現しました。最新のAI技術を駆使した、東芝が誇る世界最先端の半導体製造プロセスの誕生です。品質の向上と生産の合理化を高度に両立するため、特に力点を置いたのが「歩留解析」と「欠陥検査」のAI化でした。
「歩留解析」
ビッグデータの見える化により作業効率の改善は得られましたが、歩留不良の原因となった工程の当たりを付ける解析には、熟練の技術者でも1件当たり6時間以上の時間が必要でした。そこで、解析にかける時間をできるだけ短くし、かつ判断レベルを上げるために、ビッグデータとAIを組み合わせた「歩留新聞」という自動化システムを開発しました。このシステムにより、今まで技術者が目で見ていたウェハの面内に起こった不良の分布を分かりやすく自動で分類し、その不良の原因となった工程や装置の関係が容易に分析できるようになりました。まさに、研究開発センターのAI基盤技術と東芝デジタルソリューションズのビッグデータ技術およびAI応用技術が融合された結果です。この「歩留新聞」により、解析時間が1/3の2時間以下に大幅に削減されました(図1)。
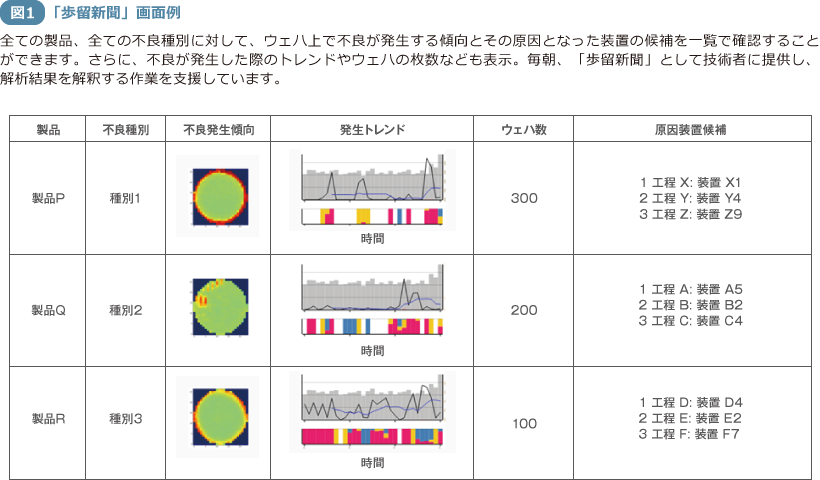
「欠陥検査」
ウェハ上の欠陥は、歩留りが低下する大きな要因のひとつです。しかし、製造工程が複雑になればなるほど、発生する欠陥の種類は多様化し、正確に分類することが難しくなります(図2)。
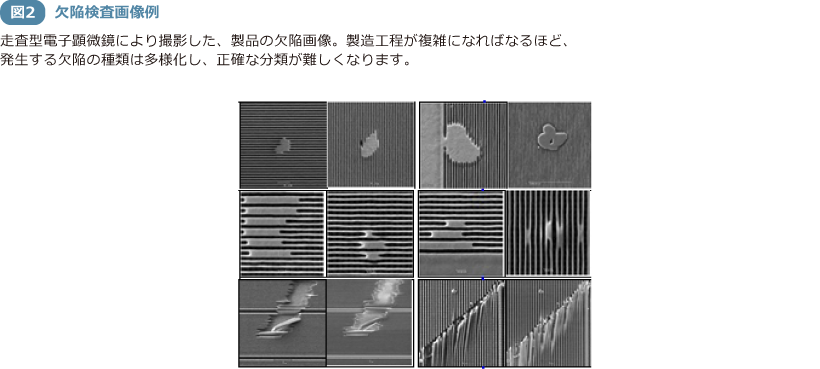
走査型電子顕微鏡による欠陥画像を自動的に分類するシステムは以前からありましたが、1日に発生する約30万枚の欠陥画像のうち、精度を満たして適用できたのは全体の約50%程度で、残る半数は人の目で分類していました。そこで、ディープラーニングを活用し、欠陥の微細で複雑な形状を正確に見分けられる新たな欠陥画像分類システムを開発しました。これにより、50%だった自動化率を83%まで向上させることができました。
「歩留解析」や「欠陥検査」以外にも、四日市工場では、製品品質の予測や、装置メンテナンス時期の自動決定など、高度な知見が必要だった領域に、AIによるサポートをふんだんに取り入れています。
AIで市場からの要求に徹底して応えるという、高度な競争力を備えた四日市工場。東芝は今後も時代に合わせた革新と改善を繰り返しながら、その成果をお客さまのデジタルトランスフォーメーションに生かしていきます。
※BiCS FLASHは、東芝メモリ株式会社の商標です。
※この記事に掲載の、社名、部署名、役職名などは、2018年2月現在のものです。