The position of operation & maintenance (O&M) is rapidly changing from a cost to a value, and then on to a source of corporate competitiveness. Toshiba Digital Solutions has a series of solutions that provides powerful support in O&M digitalization for customers in the manufacturing industry. That is the manufacturing IoT solutions, Meister Series. The Meister Series has produced countless digital transformations in manufacturing sites where products are made. Let's look at how it also provides optimal solutions for O&M digitalization at sites where products are used. This special feature also explores the solutions and advanced technologies Toshiba Digital Solutions supplies for tackling the numerous challenges companies face in digitalizing O&M, such as personnel, budgeting and the collection of data from old type equipment.
The Meister Series – the optimal solution for factory O&M digitalization
O&M in the production workplace is growing more advanced. The manufacturing IoT solutions, Meister Series, is playing a central role there and providing support to customers.
The growth of high-mix, small-lot production and the shortening of product lifecycles is creating a need for business transformation. Eyes are turning to digital transformation (DX) using advanced digital technologies such as the internet of things (IoT) and artificial intelligence (AI).
Entire value chains, including not only processes such as product and service planning, design and manufacturing, but also logistics, sales and post-sales service, are being integrally managed and optimized. This strives to dramatically improve operations and quality by visualizing processes and expertise, which have in the past been black boxes, highly dependent on the capabilities of individuals.
There is an urgent need in the O&M business field as well to make it more sophisticated and optimized through the DX, prompted by social issues such as population aging and workforce shortages. The goal of this, in the manufacturing industry, is to reduce labor costs, increase operation rates and lower energy consumption. This is achieved by efficiently managing all resources, such as production equipment and facilities in plants, maintenance workers, and the like, making highly accurate failure and lifetime predictions, and carrying out optimized operation.
The Meister Series meets these customers' needs. These solutions offer across-the-board support for the DX in manufacturing industry, both in manufacturing and product usage processes. Since its launch, the Meister Series has been introduced in various companies, contributing to operation and quality improvements. The advanced technologies and features of the Meister Series, including digital twins and so on, can also make significant contributions to O&M digitalization. Not only does the use of IoT and big data in manufacturing processes increase yield and improve production efficiency, but data regarding past and present events and situations in production sites is collected and accumulated to assist with the optimal operation of the equipment, devices and facilities used at the sites. Worksites are replicated in detail in digital space, and the high precision analysis capabilities of Toshiba's "SATLYS" analytics AI are used to digitalize the worksite knowledge of veteran engineers and to predict and forecast future events. Feedback can be rapidly provided to sites, contributing to O&M optimization on a global scale.
Click here to move to the top of this page.
Support from data collection to storage and use of them
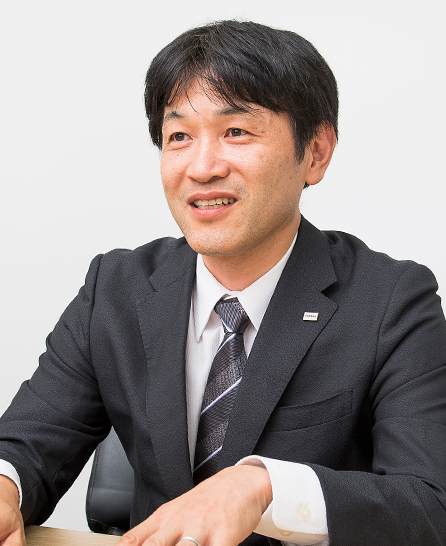
One of the major advantages of the Meister Series is that it defines three layers – data collection, data storage and data use – with optimal components for each.
"Meister IoT" is used to collect data. It supports edge computing, and connects products and devices to networks. It comprehensively collects a diverse range of data and performs real-time data processing on worksites.
"Meister DigitalTwin" supports data storage. Equipment usage data, operation data such as production and facility management, information related to facilities and operators are linked with a high level of accuracy and projected onto digital space. Development, component procurement, temperature and humidity, and inspection results are utilized to link, manage, analyze and track the site operation status and maintenance/inspection contents.
Moreover, this Meister Series offers a variety of components for using the data on Meister DigitalTwin. There is a rich lineup of applications such as on-screen visualization from various perspectives, traceability functions, big data analysis modules, and the AI service "SATLYS". Toshiba Digital Solutions are ready to provide these applications, offering the best combination of them based on customer needs.
Click here to move to the top of this page.
Challenges faced in O&M digitalization
However, no matter how exceptional solutions may be, it is no easy matter for customers to advance digitalization and maximize the value that it creates. For example, consider personnel shortages and securing budgets. Not only is it difficult to find enough maintenance and inspection personnel, but hiring personnel that are highly knowledgeable about the ICT and data analysis technologies needed to manage and utilize data is also becoming a significant problem. It is also difficult in the O&M area to guarantee that digitalization will produce benefits, and companies often struggle to calculate return on investment (ROI) and are unable to commit to deployment.
The companies that do actually deploy systems also face various challenges. On the data acquisition side, these include how to collect data from old equipment to which sensors cannot be directly connected. Another issue is how to assure network connectivity that can handle the collection of data in millisecond increments, transmitting the data while providing sufficient security. It is also difficult to verify the accuracy of models for evaluating feature value and normal/abnormal conditions in data extracted from equipment which has operated stably for years and for which therefore there is little failure or malfunction data. We work together with customers to consider, from worksite-focused perspectives, O&M digitalization approaches that can address these problems. We bring together diverse staff and advanced technologies to contribute to the steady evolution of these solutions. We provide unique support and services linked to Meister Series solutions.
Click here to move to the top of this page.
Deployment styles and advanced technologies that tackle issues
In digitalizing customer O&M, we recommend a multi-stage system deployment using various Meister Series components based on DX evolution scenarios (Fig. 1).
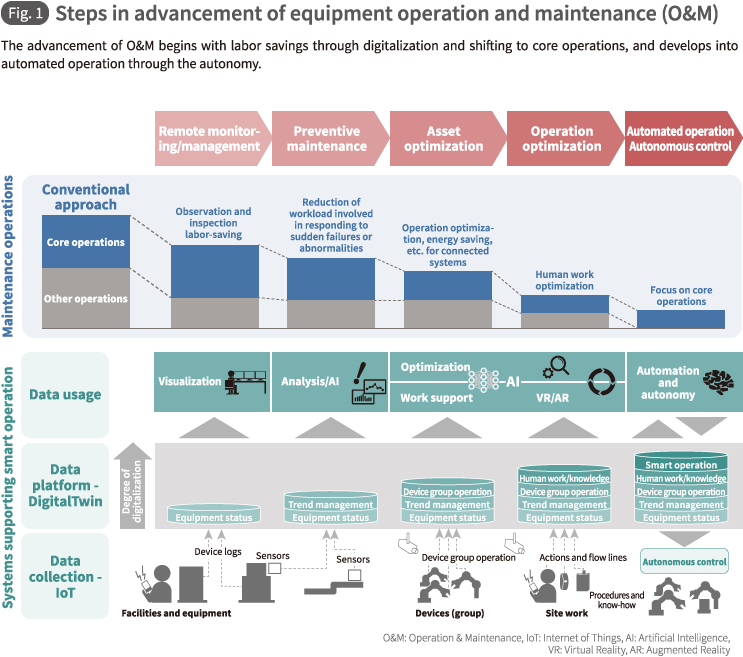
The first step is reducing workloads and shifting to core operations through the visualization of equipment operating conditions. We visualize operating conditions and perform remote monitoring for core equipment, and gradually expand the scope of equipment from which data are acquired. We confirm results through verification testing or small starts in preparation for next steps of predictive maintenance and optimization. Subsequently we use Meister IoT and Meister DigitalTwins to collect and use data. We then move onto managing information related to worksite assets and personnel, such as incidental utility equipment, spare equipment, and operator behavior, in a systematic and visualized form. Through this, we optimize, automate and autonomize factories and overall facilities. We break down equipment importance and failure frequency into multiple levels and use approaches tailored to each level, building a digitalization platform for O&M based on factory and facility features and characteristics.
For equipment which does not support direct sensor connection, we develop contact-free IoT technologies such as diagnosing facility degradation by acoustic analysis, and meter readings by image recognition. These technologies are now in their verification phases. We also enhance security and improve ICT operation efficiency by embedding separation mechanism between information/control layers and integrated management functions for edge hardware and applications in the Meister Series solutions.
We work closely with Toshiba's Corporate Research & Development Center and Manufacturing Engineering Center for the development and deployment of technologies. We have created a system for actively leveraging advanced technologies and expertise.
In the future, Toshiba Digital Solutions will link digital twins to existing operation processes using the Meister Series as a platform, and create a next-generation enterprise asset management (EAM) system to integrate each management data such as facility, inventory, procurement, operation, contract and the like. Our goal is to coordinate facility maintenance processes with related operations in all directions, and to create systems that provide optimization of entire lifecycles, from manufacturing of equipment to its operation, maintenance and disposal (Fig. 2).
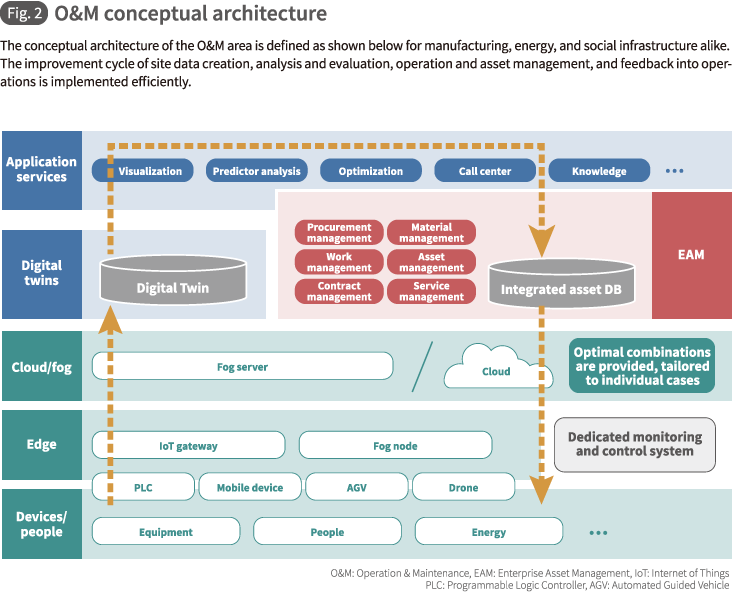
Led by the manufacturing IoT solutions "Meister Series", Toshiba Digital Solutions is drawing together the know-how it has accrued through a diverse range of factories to achieve O&M digitalization. This will not only help customers surmount the challenges they currently face, but offer unlimited future potential.
* The corporate names, organization names, job titles and other names and titles appearing in this article are those as of October 2018.