ユースケース
業務で発生する様々な課題に対し、Aras Innovatorで解決するユースケースをご紹介します。
詳細についてはお問い合わせください。
設計情報管理
工程や部門の情報をつないで製品のライフサイクル全体で共有することで、無駄な業務を削減でき本来の業務に注力できます。

工程や部門ごとにシステムやデータが
サイロ化している
- 別部門のデータを活用できない
- データの重複が発生し、正しい情報を把握できない
- 得られた知見をフィードバックできない
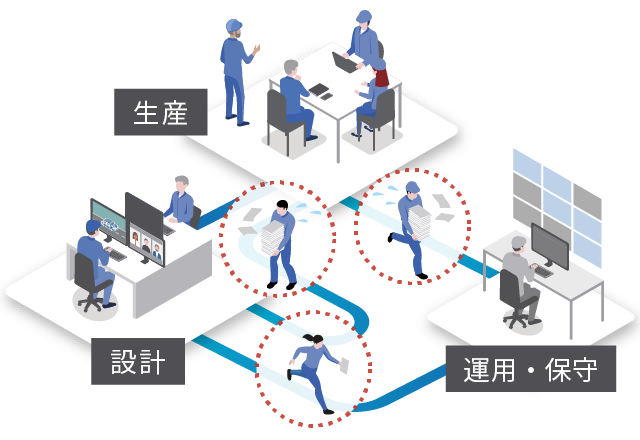

製品のライフサイクル全体で情報共有でき
データの活用により新たな価値を創出
- 工程や部門を跨った情報の一元管理により、必要なデータを活用可能
- コミュニケーションミスがなくなり正しい情報を使ったものづくりが可能
- 部門を跨いだ情報共有による新しいアイデアやイノベーションの創出
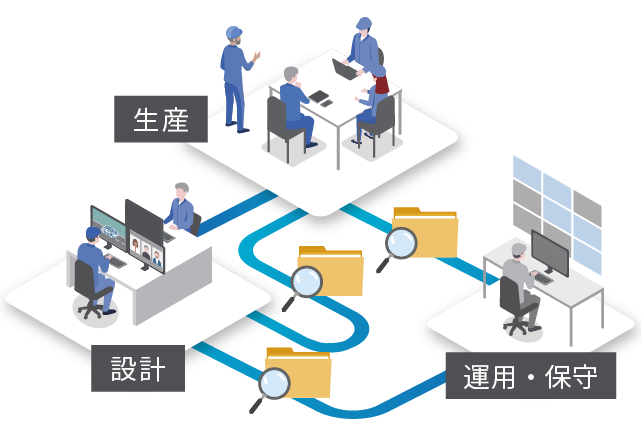

工程や部門ごとにシステムやデータが
サイロ化している
- 別部門のデータを活用できない
- データの重複が発生し、正しい情報を把握できない
- 得られた知見をフィードバックできない
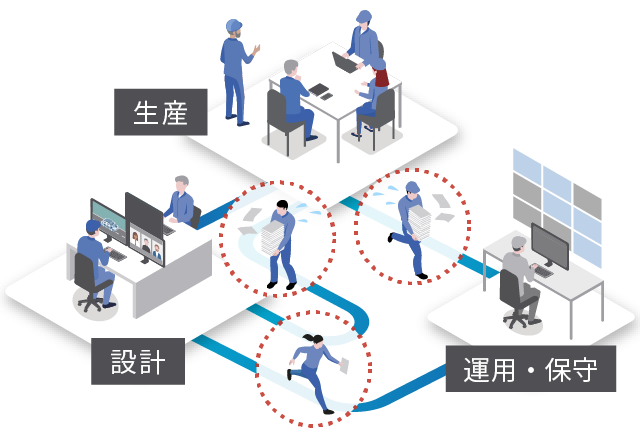

製品のライフサイクル全体で情報共有でき
データの活用により新たな価値を創出
- 工程や部門を跨った情報の一元管理により、必要なデータを活用可能
- コミュニケーションミスがなくなり正しい情報を使ったものづくりが可能
- 部門を跨いだ情報共有による新しいアイデアやイノベーションの創出
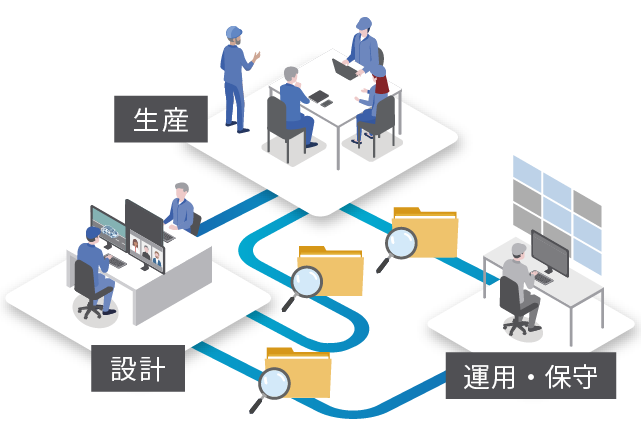
設計品質管理
APQP※1及び設計/プロセスFMEA※2手法のツールを使用してリスク管理・品質改善・再発防止につなげられます。
- APQP(Advanced Product Quality Planning):先行製品品質計画
- 設計/プロセスFMEA(Failure Mode and Effects Analysis):設計/工程の故障モード影響解析

品質問題が頻繁に発生し繰り返されている
- 品質問題が頻繁に発生する
- 品質問題に関する知見が蓄積できず、人、経験に依存する
- 問題発生後の管理が煩雑で、同じ問題が再び発生する
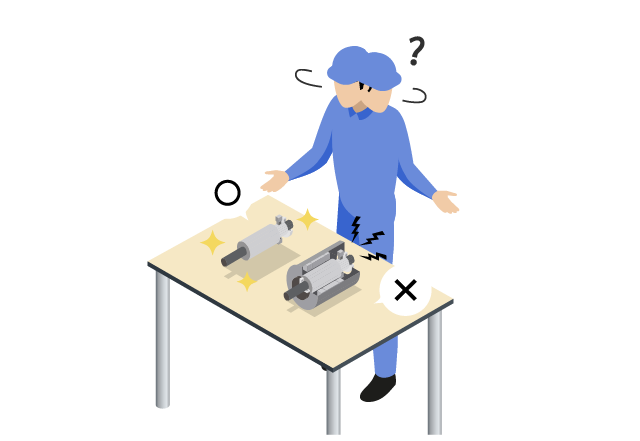

品質問題の発生を低減でき、再発を防止
- APQP、設計/プロセスFMEAにより品質問題を低減
- 知見を蓄積・共有することで、誰でも容易に分析、対応が行える
- 是正・予防措置により品質改善アクションを促進
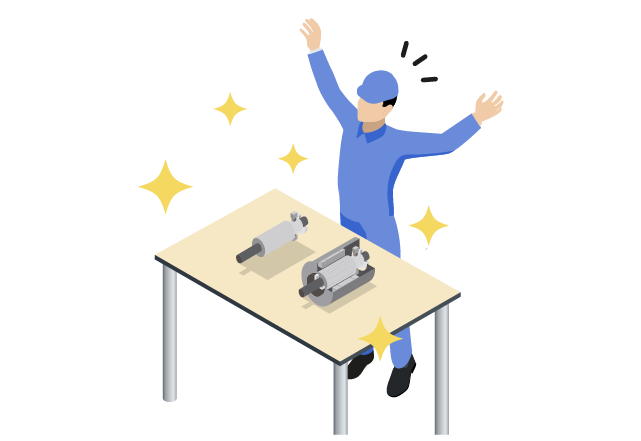

品質問題が頻繁に発生し繰り返されている
- 品質問題が頻繁に発生する
- 品質問題に関する知見が蓄積できず、人、経験に依存する
- 問題発生後の管理が煩雑で、同じ問題が再び発生する
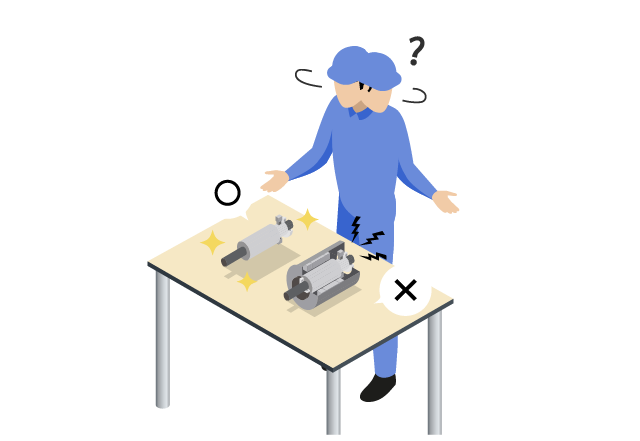

品質問題の発生を低減でき、再発を防止
- APQP、設計/プロセスFMEAにより品質問題を低減
- 知見を蓄積・共有することで、誰でも容易に分析、対応が行える
- 是正・予防措置により品質改善アクションを促進
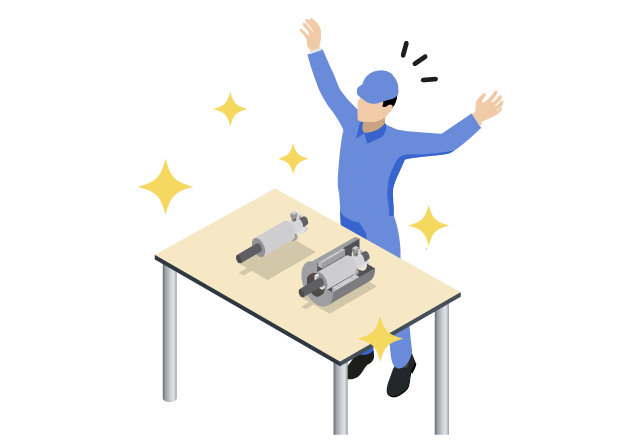
プロジェクト管理と連携した成果物管理
マイルストーン、タスクと成果物を一元管理することで、予実の把握による遅延と成果物の抜け漏れが抑制できます。

開発スケジュールの遅延や
成果物の抜け漏れが発生している
- プロジェクトのマイルストーンが把握できず、計画遅延が発生
- タスク、成果物が把握できず、抜け漏れが発生
- 成果物や設計根拠が個別に保管され、情報共有が困難
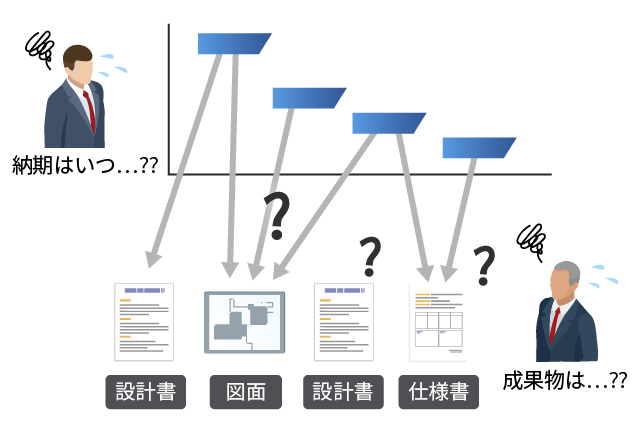

開発スケジュールの遅延や
成果物の抜け漏れを抑制
- 開発計画を基にマイルストーンを設定することで、開発進捗を管理
- プロジェクト全体のタスク・成果物を一元管理でき、抜け漏れが低減
- 成果物や設計根拠を蓄積・共有し、データを別のプロジェクトに活用
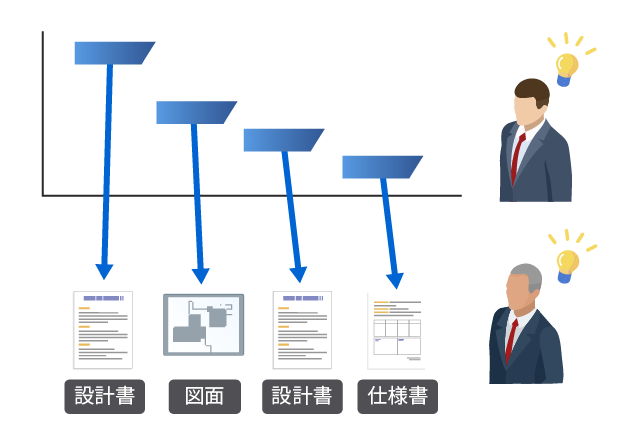

開発スケジュールの遅延や
成果物の抜け漏れが発生している
- プロジェクトのマイルストーンが把握できず、計画遅延が発生
- タスク、成果物が把握できず、抜け漏れが発生
- 成果物や設計根拠が個別に保管され、情報共有が困難
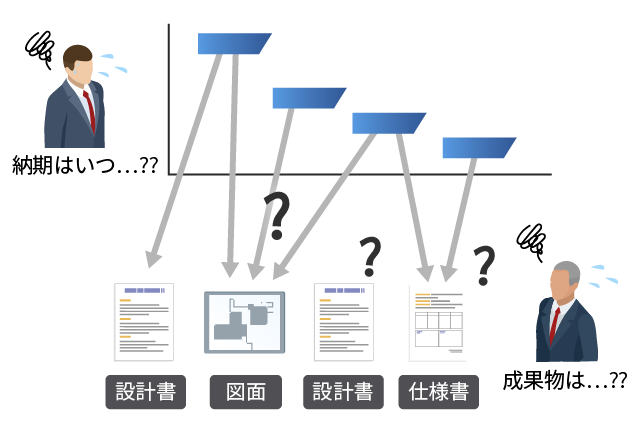

開発スケジュールの遅延や
成果物の抜け漏れを抑制
- 開発計画を基にマイルストーンを設定することで、開発進捗を管理
- プロジェクト全体のタスク・成果物を一元管理でき、抜け漏れが低減
- 成果物や設計根拠を蓄積・共有し、データを別のプロジェクトに活用
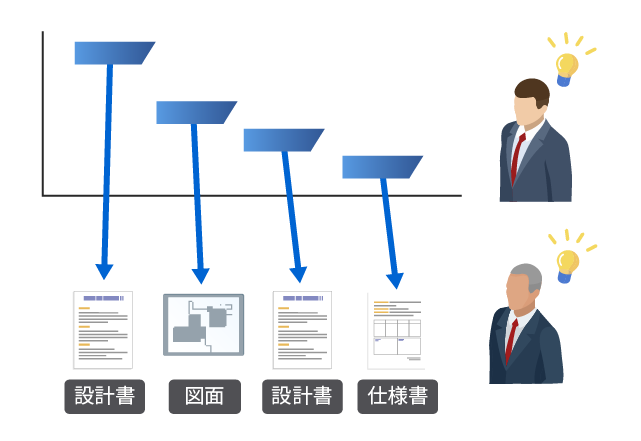
IoTデータと設計データの連携(Meister RemoteX連携)
IoTデータと設計データを紐づけることで、製品の問題を早期に発見し、製品設計に反映できます。
※別途、Meister RemoteXの導入が必要になります。

製品の稼働状況やトラブル原因が分からない
- 製品出荷後の稼働状況やトラブル原因が特定できないことがある
- 製品使用上の改善点、不具合がわからず、新規製品設計に活かすことができない
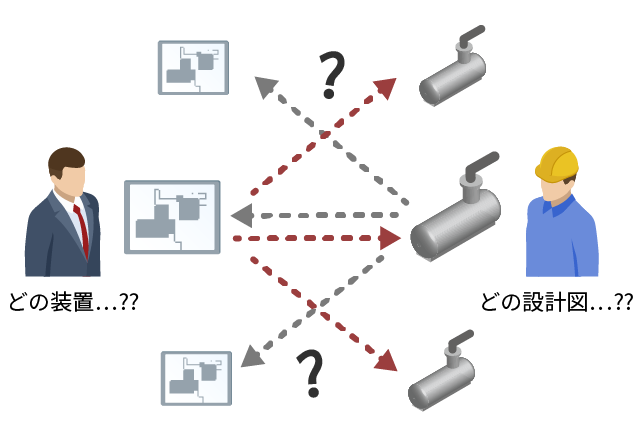

トラブルを早期に特定し、新規製品設計に反映
- 出荷後の製品のシリアルBOMとE-BOMの比較により、問題がある部品の早期特定・早期対応が可能
- 製品の仕様と稼働データから部品の使用状況を推測し、新規製品設計への反映を判断
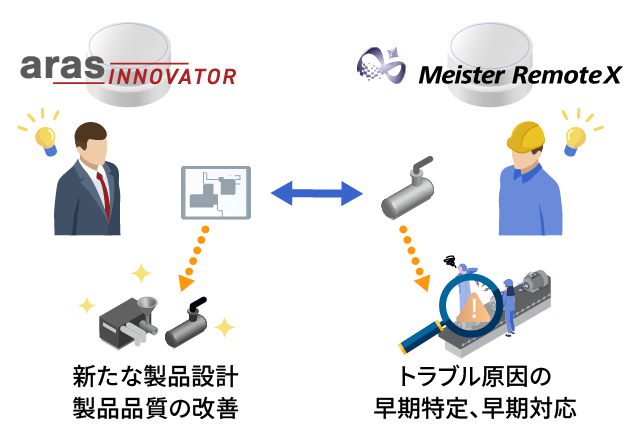

製品の稼働状況やトラブル原因が分からない
- 製品出荷後の稼働状況やトラブル原因が特定できないことがある
- 製品使用上の改善点、不具合がわからず、新規製品設計に活かすことができない
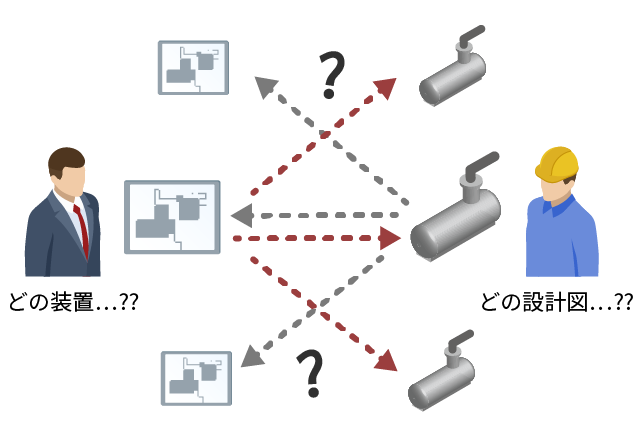

トラブルを早期に特定し、新規製品設計に反映
- 出荷後の製品のシリアルBOMとE-BOMの比較により、問題がある部品の早期特定・早期対応が可能
- 製品の仕様と稼働データから部品の使用状況を推測し、新規製品設計への反映を判断
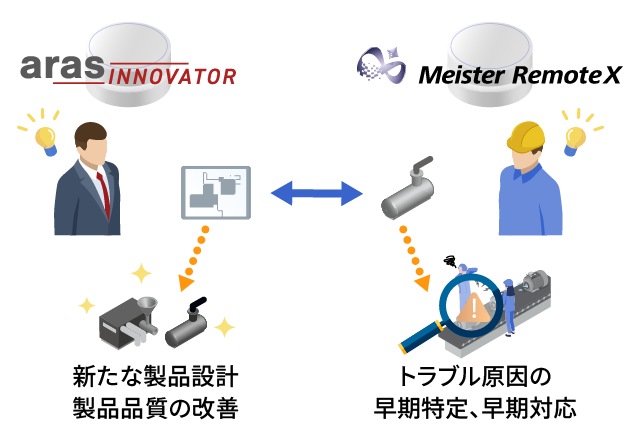
資料ダウンロード
商品紹介のリーフレットをダウンロードいただけます。
関連リンク
「Meister RemoteX」は、納入した設備・機器の稼働データや保守履歴を活用したメンテナンスサービスを実現する、設備・機器メーカー向けアセットIoTクラウドサービスです。
社会インフラなどの遠隔監視の知見を蓄積した東芝が考えるO&Mのデジタル革新について、「アセットIoTクラウドサービス」と合わせてご紹介します。