事例
東芝ライテック様事例
既存の外観検査装置に適用し未知の不良検出を短期間で実現可能に
徹底した検査体制を整備してきた車載用ソケットLEDの製造ラインにおいて、想定外の未知の不良が発生。導入していたルールベースの自動外観検査装置では拡張が難しく、またどこまでチェック領域を広げていけばいいのかについて正解を導き出すのも困難だった。
既存の検査装置と組み合わせてMeister Apps AI画像自動検査パッケージを導入・運用することで、検出精度の目標値95%を達成。未知の不良も検出できる環境整備によって、確実かつ高精度な生産体制を実現し、顧客の信頼感の醸成を促進。ルールベースでの導入と比較して短期間でのシステム実装が可能になった。
※クリックするとフォームが立ち上がります。
お申し込みいただいたお客様の個人情報は、暗号化され保護されます。
※クリックするとフォームが立ち上がります。
お申し込みいただいたお客様の個人情報は、暗号化され保護されます。
ユースケース
ユースケース1:検査パラメータの設定工数削減例
ダイカスト品の検査
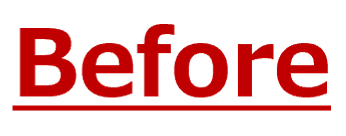
1つのワークの撮像箇所が非常に多いため、画像処理システムでルールベース設定をした場合、膨大な時間がかかってしまう
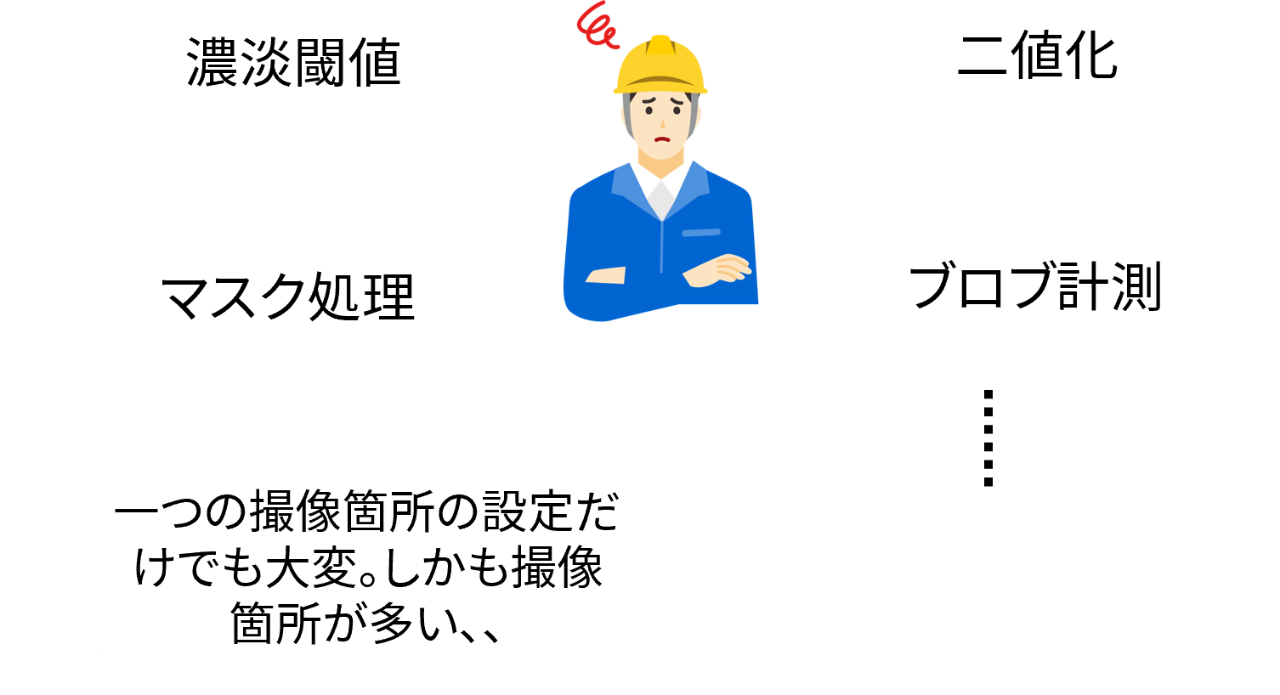
「1:良品画像の収集」、「2:学習・検証」、「3:良品モデル投入」の簡単 “3STEP”により、設定工数を削減
~他社製画像処理システムとの組み合わせによるハイブリッド方式の例~
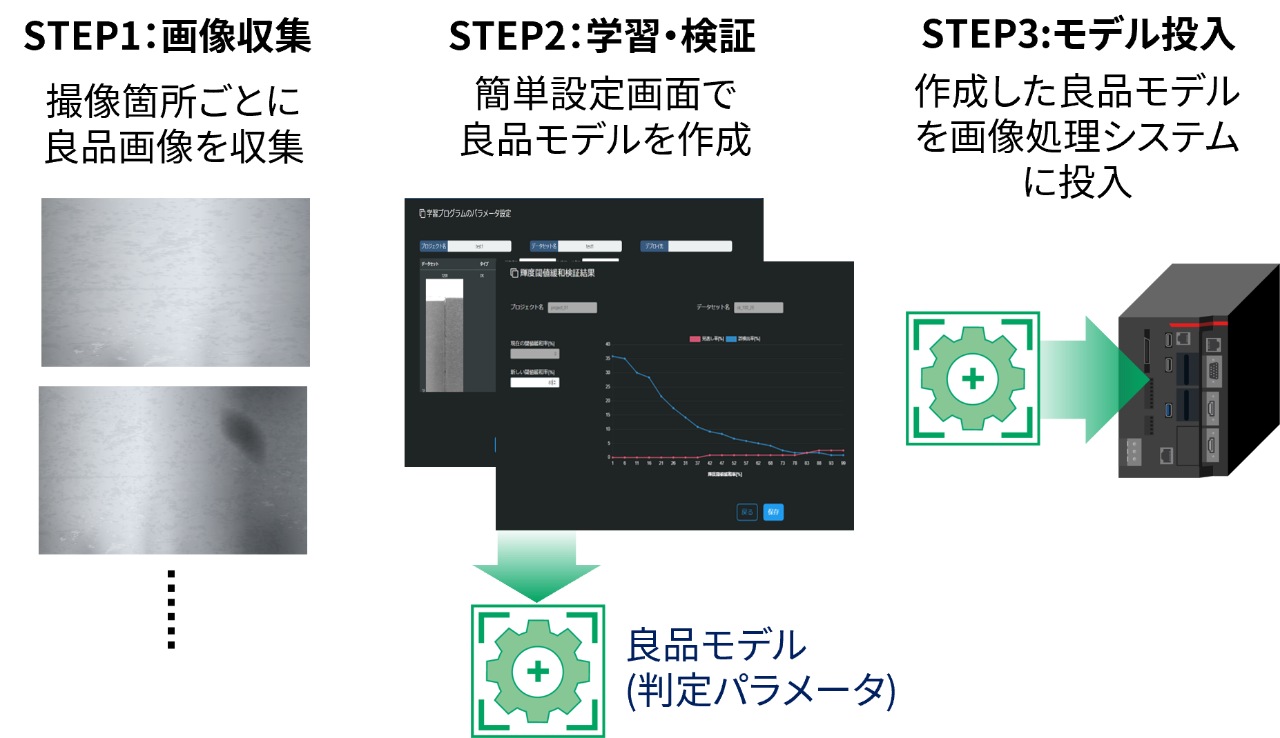

※撮像箇所200以上の検査パラメータ設定をした場合
ルールベースの画像処理システムの検査パラメータを自社で設定している場合、検査パラメータ設定が不要となり設定工数を削減
ユースケース2:再検査の工数削減例
溶接検査(キズ、形状)
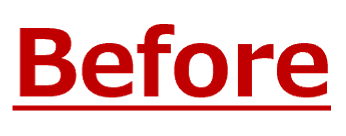
溶接個所の仕上がり状態が一品一様でバラつきが大きいため、ルールベース設定だと過検出が発生しやすく、再検査の工数がかかってしまう
例)溶接個所のバラつきの例
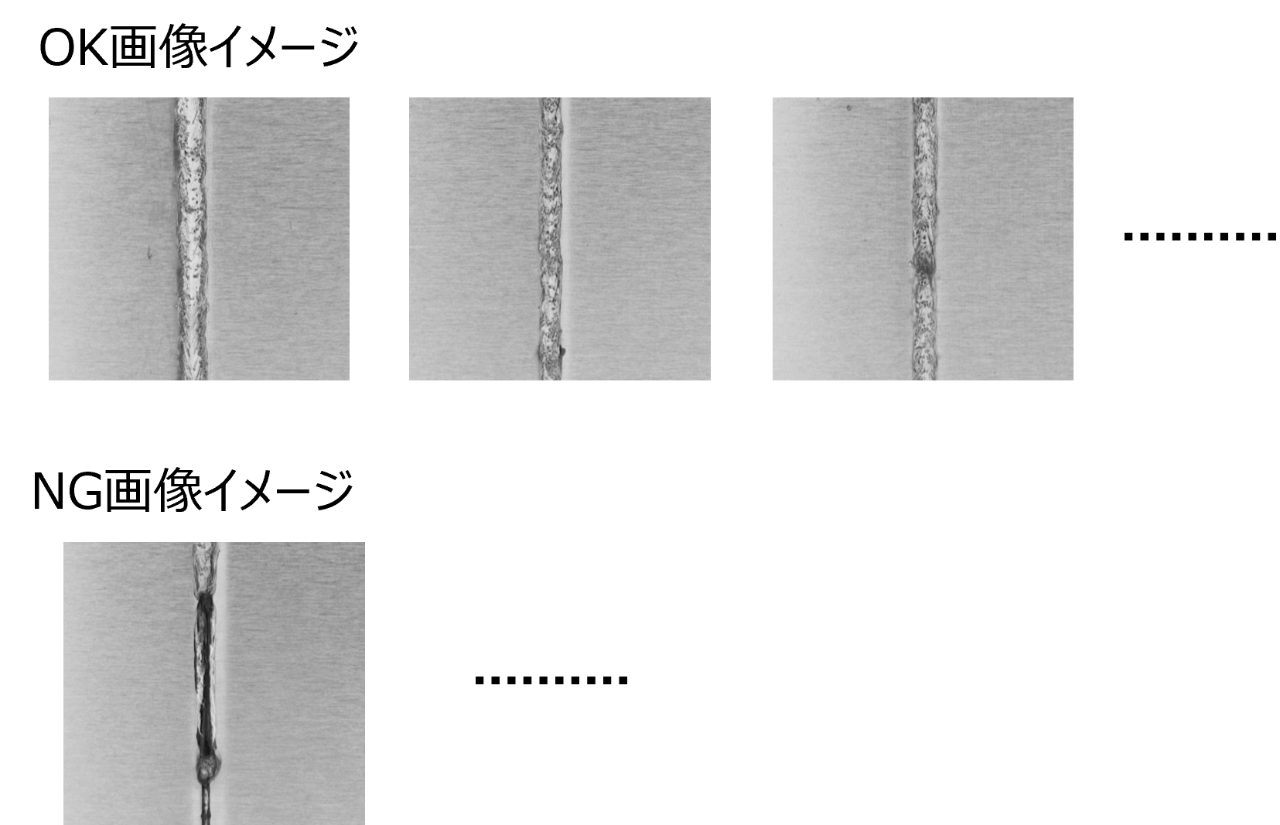
良品のばらつきを学習し良品閾値を最適化することで、溶接個所の過検出を低減し、再検査の工数を削減
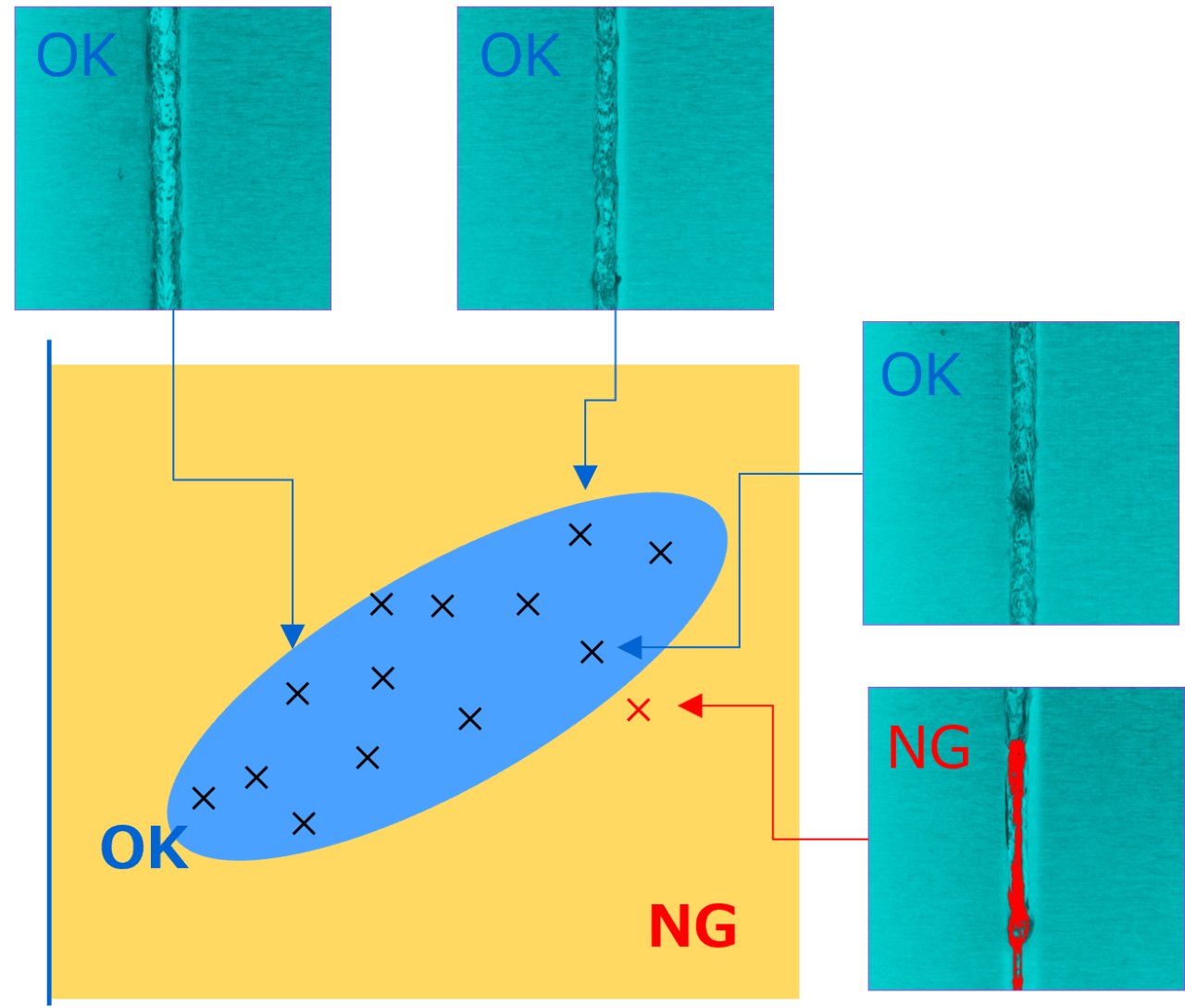

※過検出率10%⇒1%(月産10000個)の場合
過検出発生時に生産ラインを一時的に停止させて作業員が目視で再検査している場合、過検出を低減することで作業員の対応工数を削減
ユースケース3:専門技術者の対応工数削減例
部品取り付け、印字検査他
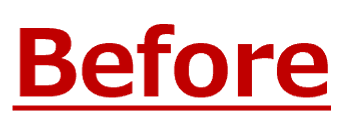
何らかの問題が発生し検査パラメータを調整する場合、生産技術部門に都度対応してもらう必要がある
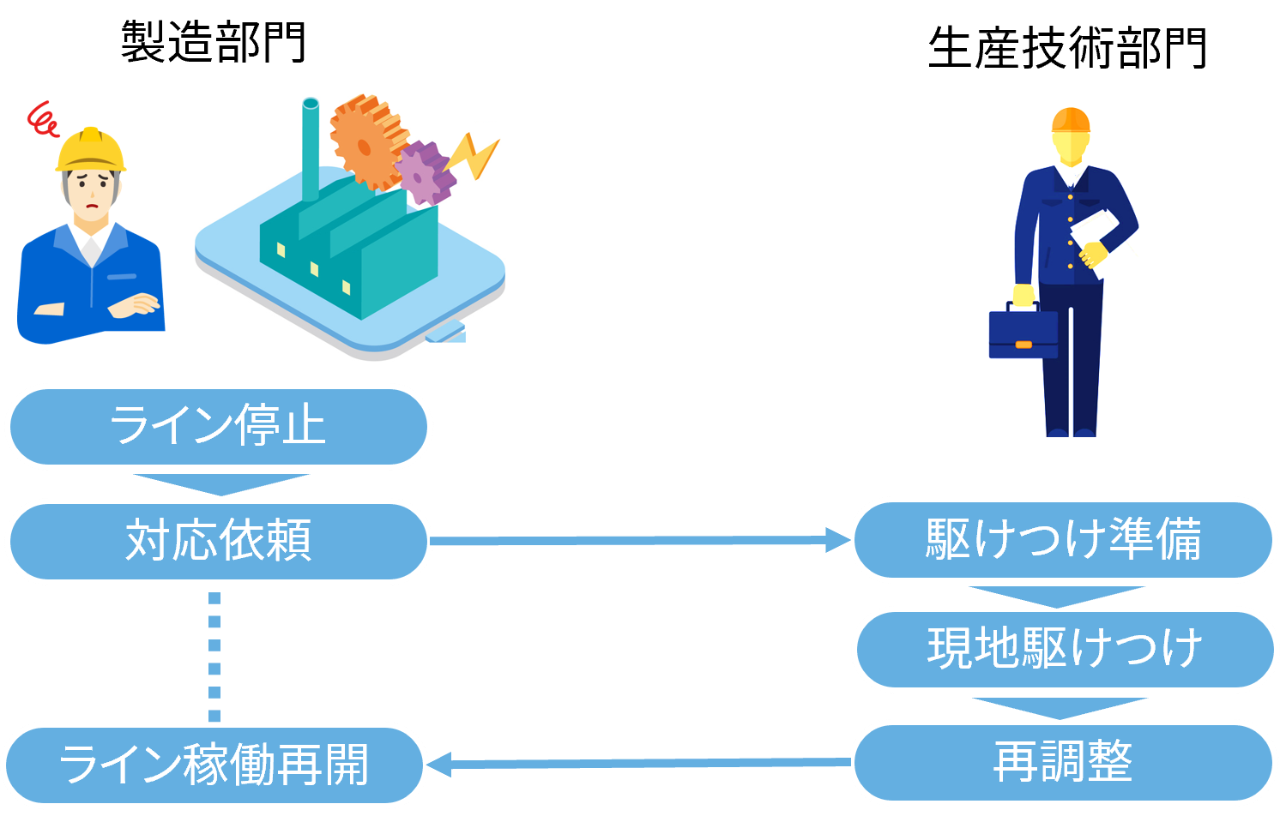
製造部門で調整できるようにすることで、生産技術部門の対応工数を削減
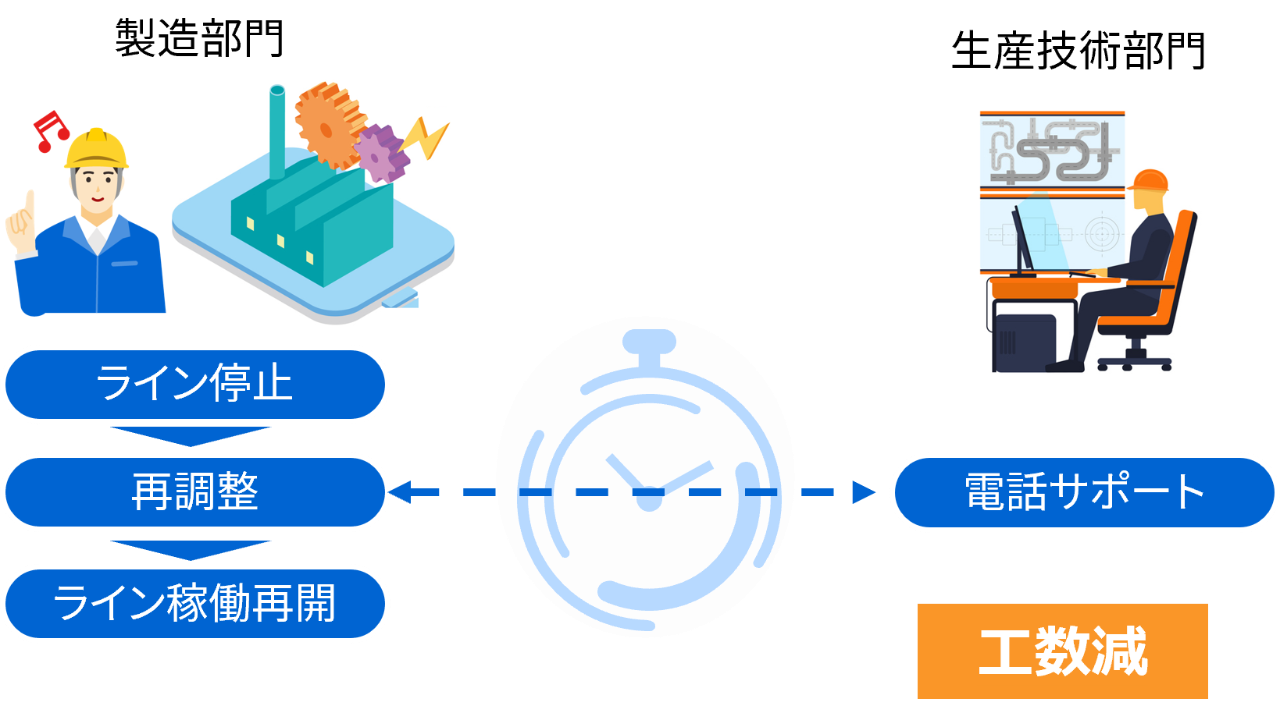

※月2回以上、現地駆けつけ対応した場合
画像処理システムを設定している生産技術部門が、過検出や見逃しが発生したことで都度現地対応をしている場合、製造部門で調整できるようにすることで、対応工数を削減